views
How to Troubleshoot and Repair Electrical Problems in Heavy Equipment
Question:
What are common electrical problems in heavy equipment, and how can I effectively troubleshoot and repair these issues?
Answer:
Electrical problems in heavy equipment can be frustrating and lead to significant downtime. These issues often arise from faulty wiring, dead batteries, or malfunctioning components, causing the equipment to malfunction or stop working altogether. Knowing how to identify and fix these problems can help keep your machinery running efficiently. Here’s a detailed guide on troubleshooting and repairing common electrical issues in heavy equipment.
1. Dead or Weak Battery
A dead or weak battery is one of the most common electrical issues in heavy equipment. It can prevent the engine from starting or cause intermittent electrical failures.
How to Fix It:
Start by checking the battery voltage with a multimeter. A fully charged battery should read around 12.6 volts or higher. If the voltage is low, recharge the battery and test it again. Inspect the battery terminals for corrosion and clean them if necessary. Ensure the connections are tight and secure. If the battery doesn’t hold a charge, it may need to be replaced.
Pro Tip: Regularly check the battery and clean the terminals to prevent starting issues.
2. Faulty Alternator
The alternator is responsible for charging the battery and supplying power to the electrical system. A faulty alternator can lead to a drained battery and electrical malfunctions.
How to Fix It:
To test the alternator, start the engine and measure the voltage at the battery terminals. It should read between 13.5 and 14.5 volts. If the voltage is below this range, the alternator may be failing. Check the alternator belt for proper tension and condition. If the alternator is not functioning properly, it will need to be repaired or replaced.
Pro Tip: Keep the alternator belt in good condition and check the charging system regularly to avoid electrical failures.
3. Blown Fuses or Relays
Blown fuses or faulty relays can disrupt power to various components, causing them to stop working.
How to Fix It:
Locate the fuse box and check for blown fuses. Replace any blown fuses with ones of the correct rating. Inspect the relays by swapping them with identical ones from another circuit. If the problem moves with the relay, it may be defective and should be replaced.
Pro Tip: Keep spare fuses and relays on hand for quick replacements during breakdowns.
4. Damaged Wiring or Loose Connections
Damaged wiring or loose connections can cause intermittent electrical issues, short circuits, or complete power loss.
How to Fix It:
Inspect the wiring harness for any visible signs of damage, such as frayed wires, cuts, or burn marks. Check all connectors for tightness and corrosion. Repair or replace any damaged wires and clean or replace corroded connectors. Ensure all connections are secure and protected from moisture and debris.
Pro Tip: Regularly inspect the wiring and connectors, especially in areas exposed to harsh conditions, to prevent electrical failures.
5. Malfunctioning Sensors or Switches
Faulty sensors or switches can cause incorrect readings or prevent the equipment from operating correctly.
How to Fix It:
Use a diagnostic tool to check for error codes related to sensors or switches. Inspect the sensors and switches for physical damage or loose connections. Test the components with a multimeter to ensure they are functioning correctly. Replace any faulty sensors or switches with OEM parts to ensure proper operation.
Pro Tip: Follow the manufacturer’s diagnostic procedures to accurately identify and replace faulty components.
6. Starter Motor Issues
A failing starter motor can cause the engine to crank slowly or not start at all.
How to Fix It:
Check the starter motor by turning the key to the start position and listening for any unusual noises, such as clicking or grinding. Inspect the starter connections for tightness and corrosion. Test the starter motor with a multimeter to ensure it is receiving the proper voltage. If the starter motor is faulty, replace it with a compatible unit.
Pro Tip: Ensure the starter motor is properly maintained and inspect it during routine service checks.
7. Grounding Issues
Poor grounding can lead to erratic electrical behavior, such as flickering lights, intermittent failures, or sensor malfunctions.
How to Fix It:
Inspect the ground connections for tightness and cleanliness. Clean any corroded ground points and ensure the connections are secure. Test the grounding system with a multimeter to confirm there is minimal resistance. Strengthen or replace weak or damaged ground connections to restore proper function.
Pro Tip: Regularly check ground connections, especially after working in wet or corrosive environments.
8. Control Module Failures
Control modules, such as the ECM (Engine Control Module), manage various electronic functions. A malfunctioning control module can cause a range of issues, from engine performance problems to complete system failures.
How to Fix It:
Use diagnostic tools to read any fault codes stored in the control module. Inspect the module for physical damage or loose connections. If the control module is faulty, it may need to be reprogrammed or replaced. Consult the equipment’s service manual for specific instructions on testing and replacing control modules.
Pro Tip: Keep the control modules updated with the latest software versions as recommended by the manufacturer.
Conclusion:
Electrical problems in heavy equipment can be complex but are often preventable with regular maintenance and inspections. By addressing issues such as dead batteries, faulty alternators, damaged wiring, and malfunctioning sensors, you can keep your equipment running smoothly. For detailed repair guides and troubleshooting tips, visit pdfmanualsshop.com, where you can find comprehensive manuals for all your heavy equipment needs.
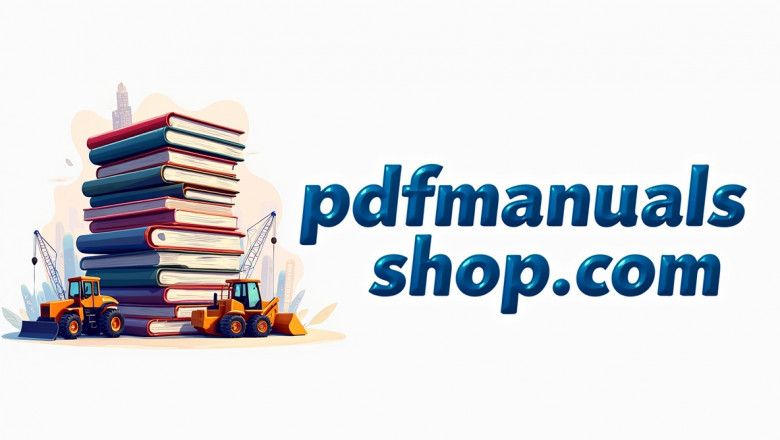

Comments
0 comment