views
Understanding Pressure Vessels: Design, Types, and Applications
Pressure vessels are containers designed to hold gases or liquids at a pressure substantially different from the ambient pressure. These critical components are used across a wide range of industries including oil and gas, chemical processing, power generation, pharmaceuticals, food and beverage, and aerospace. Their primary function is to store, process, or transport fluids under pressure in a safe and efficient manner.
Given their importance and the potential hazards associated with pressurized systems, pressure vessels are designed with stringent standards and codes to ensure structural integrity, safety, and efficiency.
Basic Principles of Pressure Vessels
A pressure vessel must be strong enough to contain the internal pressure without rupturing or deforming. It should also be durable enough to withstand environmental factors like corrosion, temperature variations, and mechanical stresses over its intended lifespan.
Key Parameters
-
Internal Pressure (P): Pressure exerted by the fluid inside the vessel.
-
Wall Thickness (t): Thickness of the vessel walls, influencing its strength.
-
Diameter (D): Affects stress distribution and wall thickness requirements.
-
Material Strength (σ): The yield or tensile strength of the construction material.
The basic formula used for cylindrical pressure vessels is derived from thin-wall or thick-wall pressure vessel theory, with the most common being:
t=P⋅D2⋅σ⋅E−Pt = \frac{P \cdot D}{2 \cdot \sigma \cdot E - P}
Where:
-
tt = wall thickness
-
PP = internal pressure
-
DD = inside diameter
-
σ\sigma = allowable stress of the material
-
EE = weld efficiency
Types of Pressure Vessels
1. Based on Shape
-
Cylindrical Pressure Vessels: Most common; often used in boilers and storage tanks.
-
Spherical Pressure Vessels: Ideal for high-pressure applications due to uniform stress distribution.
-
Conical and Ellipsoidal Heads: Used as end caps; ellipsoidal heads provide better stress distribution than flat ones.
2. Based on Function
-
Storage Vessels: Store compressed gases or liquids (e.g., LPG tanks, cryogenic tanks).
-
Heat Exchangers: Transfer heat between fluids while maintaining pressure boundaries.
-
Reactors: Conduct chemical reactions under pressure (e.g., in petrochemical industries).
-
Separators: Separate components of fluid mixtures under pressure.
Materials Used in Pressure Vessels
The choice of material significantly impacts the safety and performance of pressure vessels. It depends on the application, pressure, temperature, and the nature of the contained fluid.
Common Materials:
-
Carbon Steel: Economical and strong; used widely for moderate temperatures and pressures.
-
Stainless Steel: Offers excellent corrosion resistance; ideal for food, pharmaceutical, and corrosive environments.
-
Aluminum and Titanium: Lightweight, corrosion-resistant; used in aerospace and specialized chemical applications.
-
Composite Materials: Used in modern pressure vessels where weight reduction is critical.
Design Standards and Codes
Pressure vessel design is governed by strict codes and standards developed by regulatory bodies to ensure safety and reliability.
Major Standards:
-
ASME Boiler and Pressure Vessel Code (BPVC): Widely used in the United States and internationally.
-
EN 13445: European standard for unfired pressure vessels.
-
PD 5500: UK standard for unfired pressure vessels.
-
IS 2825: Indian standard for pressure vessels.
These codes define design, fabrication, inspection, testing, and certification processes for pressure vessels.
Manufacturing and Fabrication
The fabrication process for pressure vessels is complex and involves:
-
Material Selection and Testing
-
Cutting and Shaping (rolling plates into cylindrical or spherical shapes)
-
Welding: Ensuring full penetration, defect-free joints.
-
Heat Treatment: To relieve residual stresses.
-
Non-Destructive Testing (NDT): Radiographic, ultrasonic, or magnetic particle testing to detect internal flaws.
-
Hydrostatic and Pneumatic Testing: Pressure testing with water or air to ensure structural integrity.
-
Surface Treatment and Coating: To resist corrosion and improve longevity.
Applications of Pressure Vessels
Pressure vessels are used in various sectors:
-
Petroleum and Gas: For separation, storage, and refining processes.
-
Chemical Processing: Reactors, digesters, and containment systems.
-
Power Plants: Steam generators and nuclear reactor vessels.
-
Pharmaceutical and Food Industries: Sanitary vessels for mixing and storage.
-
Marine and Aerospace: Propellant tanks and life-support systems.
Safety and Risk Management
Pressure vessels, if not properly designed or maintained, can fail catastrophically, leading to loss of life and property. Hence, safety is paramount.
Risk Mitigation Includes:
-
Regular inspections and maintenance
-
Use of safety valves and rupture discs
-
Adherence to operational limits
-
Monitoring for corrosion, fatigue, and stress
Failure modes include:
-
Brittle Fracture
-
Fatigue Failure
-
Corrosion and Stress Corrosion Cracking
-
Overpressure and Explosions
Accidents like the Texas City Refinery explosion (2005) highlight the importance of strict adherence to design, operation, and maintenance protocols.
Future Trends in Pressure Vessel Technology
-
Smart Monitoring: IoT-enabled sensors for real-time monitoring of pressure, temperature, and corrosion.
-
Advanced Materials: Use of composites and high-performance alloys for better strength-to-weight ratios.
-
Additive Manufacturing: Emerging role of 3D printing for custom or complex geometries.
-
Green Technologies: Pressure vessels for hydrogen storage and carbon capture systems.
Conclusion
Pressure vessels are indispensable to modern industry and daily life. Their design and operation must balance performance, safety, and cost-efficiency. As technology advances, so too do the materials, design methods, and safety protocols, ensuring pressure vessels continue to serve safely and effectively across a broad spectrum of applications.
The future holds promise for lighter, smarter, and more resilient pressure vessels that can withstand extreme conditions while supporting emerging technologies and sustainability goals.
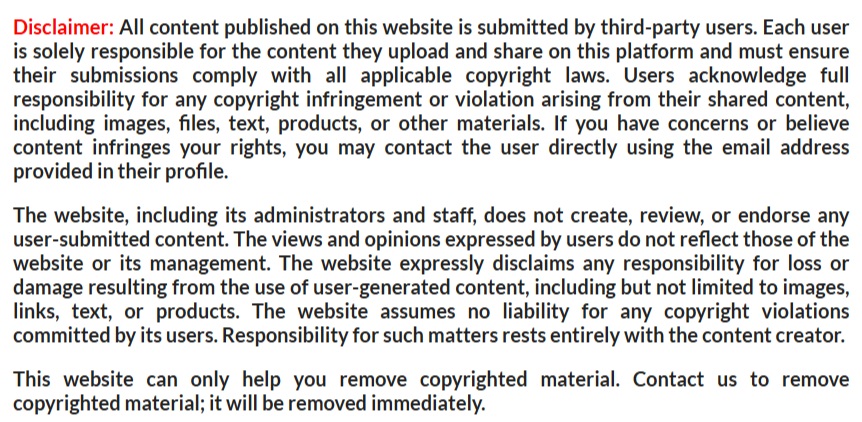