views
In the intricate landscape of industrial processing, the lobe pump stands out as a highly specialized and remarkably effective solution for fluid transfer. Distinguished by its gentle handling capabilities and precise volumetric displacement, this positive displacement pump is an indispensable tool across a vast array of demanding applications. From maintaining the delicate texture of food products to ensuring the safe transfer of corrosive chemicals, the lobe pump's unique design guarantees both product integrity and operational reliability, cementing its critical role in contemporary manufacturing paradigms.
The Essence of Positive Displacement: Unpacking Volumetric Efficiency
The fundamental principle governing the operation of a lobe pump is positive displacement, a characteristic that sets it apart from dynamic pumps like centrifugals. Unlike centrifugal pumps, which impart velocity to a fluid, a lobe pump traps a fixed volume of fluid between its rotating lobes and the pump casing, then positively displaces that volume with each revolution. This inherent design ensures that a precise quantity of fluid is moved per cycle, largely independent of changes in discharge pressure or variations in fluid viscosity.
This "positive" action translates directly to high volumetric efficiency, particularly when handling viscous fluids. For thick liquids, where centrifugal pumps might struggle to generate sufficient head or could experience cavitation, the lobe pump maintains a consistent and predictable flow rate. This volumetric consistency makes it an ideal choice for metering, dosing, and transfer applications where precise control over the fluid volume is paramount. The internal clearances, while minimal, are crucial for allowing the lobes to rotate without contact, preventing wear and preserving the pump's gentle handling capabilities. This distinct operational mode ensures minimal slippage, especially with higher viscosity liquids, contributing significantly to its overall efficiency and reliability in challenging fluid environments.
Advanced Materials and Surface Engineering: Beyond Standard Solutions
While stainless steel (particularly 316L for sanitary applications) is a common material for lobe pump construction, the demands of specialized industries necessitate a deeper dive into advanced material science and surface engineering. The longevity and performance of a lobe pump are profoundly influenced by the materials chosen for its wetted parts and the quality of their surface finish.
-
Corrosion Resistance: For highly corrosive chemicals, exotic alloys like Hastelloy, Titanium, or Duplex Stainless Steels may be employed. These materials offer superior resistance to aggressive media, extending the pump's service life and ensuring process safety.
-
Abrasive Resistance: When handling abrasive slurries or fluids containing hard particles, specialized coatings (e.g., ceramic, hardened chrome) or robust elastomers for the lobes can significantly reduce wear on pump components. These engineered solutions mitigate the abrasive effects that could otherwise lead to premature failure.
-
Elastomer Selection: For certain lobe designs or specific sealing applications, the choice of elastomer (e.g., EPDM, Viton, PTFE) is critical, considering chemical compatibility, temperature resistance, and compliance with sanitary standards (e.g., FDA, 3-A).
-
Surface Finish (Ra Values): In hygienic applications, the internal surface finish (measured in Ra, roughness average) of the pump casing and lobes is meticulously controlled. Extremely smooth surfaces (low Ra values) prevent microbial growth, facilitate thorough CIP/SIP cleaning, and minimize product adhesion, ensuring purity and preventing contamination. Manufacturers like ACE LOBE PUMP often highlight their commitment to these material and surface quality standards, crucial for certifications and performance.
Temperature Management: The Role of Jacketing in Lobe Pumps
Maintaining the optimal temperature of the fluid during transfer is critical for many processes, and lobe pumps can be equipped with specialized features to facilitate this. Heating or cooling jackets are integrated into the pump casing or front cover to provide temperature control.
-
Heating Jackets: These are essential for fluids that solidify or become excessively viscous at ambient temperatures, such as chocolate, asphalt, waxes, or heavy oils. By circulating hot water, steam, or thermal oil through the jacket, the pump maintains the fluid's temperature, ensuring it remains in a pumpable state and prevents solidification within the pump.
-
Cooling Jackets: Conversely, cooling jackets can be used for shear-sensitive fluids that might degrade or exothermic processes where heat buildup needs to be dissipated. Cooling helps maintain product integrity and stability, especially in pharmaceutical or fine chemical applications.
-
Applications: The use of jacketing highlights the lobe pump's adaptability, ensuring consistent viscosity and preventing process disruptions, thus expanding its utility in complex thermal management scenarios.
Installation Best Practices: Laying the Foundation for Performance
Optimal performance of a lobe pump begins long before operation, rooted in proper installation. Meticulous attention to installation best practices is crucial for preventing issues like excessive vibration, premature wear, and inefficient operation.
-
Foundation and Leveling: A rigid, level foundation is paramount to support the pump, motor, and gearbox assembly. Proper leveling ensures correct alignment and minimizes stress on components.
-
Piping Design: Suction and discharge piping should be adequately sized to minimize pressure drops and ensure optimal flow conditions. Long runs, excessive bends, or restrictive fittings on the suction side can lead to cavitation. Support for piping should be independent of the pump to avoid transmitting pipe stress to the pump casing.
-
Alignment: Precise alignment of the pump and motor shafts is critical. Misalignment can cause excessive vibration, premature bearing and seal failure, and increased power consumption. Laser alignment tools are often used for maximum precision.
-
Commissioning: Proper commissioning, including checking rotation, lubricating bearings, and ensuring correct seal flush/barrier fluid systems are operational, sets the stage for reliable long-term performance.
Energy Efficiency and Environmental Stewardship
The lobe pump contributes significantly to energy efficiency and environmental sustainability within industrial operations. Its positive displacement nature means it consumes energy directly proportional to the work done in moving a specific volume of fluid, rather than dissipating energy as heat through excessive fluid agitation, which can occur in some centrifugal pump applications, especially with viscous fluids.
Furthermore, its gentle handling characteristics reduce product shear and degradation, minimizing product waste and improving yield, particularly for high-value or sensitive materials. The pump's robust construction and long operational lifespan also reduce the need for frequent replacements, lowering material consumption and waste generation. By minimizing spills through effective sealing and preventing contamination through hygienic design, the lobe pump supports cleaner production processes and reduces environmental impact, aligning with modern sustainability goals.
In conclusion, the lobe pump's sophisticated engineering, adaptability to diverse materials and temperatures, and its inherent operational efficiencies underscore its status as a vital component in modern industrial infrastructure. Its ability to provide precise, gentle, and reliable fluid transfer makes it not just a pump, but a strategic asset contributing to product quality, process efficiency, and environmental responsibility.
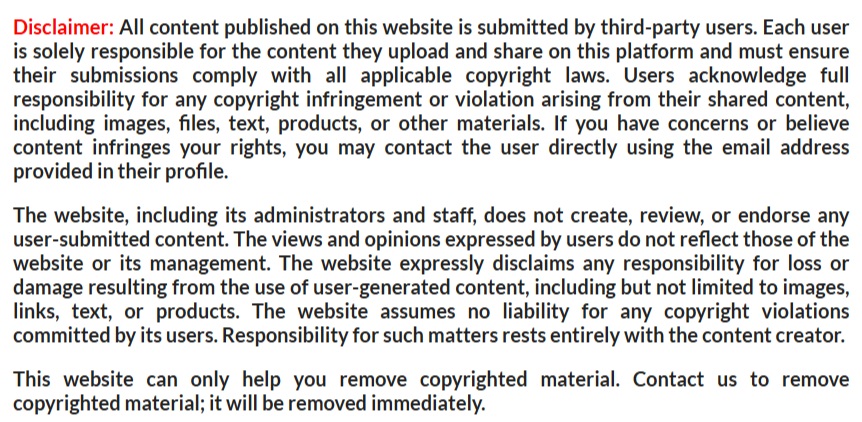