views
Introduction
Lathe chucks play a major role in machining, but it's the lathe chuck jaws that do the real gripping work. These jaws hold the workpiece tightly so it can be machined accurately and safely. Whether you're a professional machinist or a hobbyist, understanding different types of chuck jaws can help you improve performance and reduce costly errors.
Choosing the right jaws affects precision, safety, and efficiency. In fact, many machine shops overlook this essential detail, even though the global metalworking market is worth over $80 billion. Often, a simple upgrade to the right jaws can lead to big improvements.
Expert Tip: “Right jaws = better grip, fewer errors, faster work.”
Let’s dive into the types, materials, and applications of lathe chuck jaws so you can make smarter choices for your machine shop or project.
Types of Lathe Chuck Jaws
1. Standard Jaws
Standard jaws are the most common type used in general machining. They are typically included with most lathe chucks and are designed for a variety of everyday tasks.
-
Ideal for basic turning, facing, and drilling operations.
-
Quick setup and easy to use.
-
Usually reversible (internal and external gripping).
Example: A small machine shop uses plain standard jaws for batch work on steel rods and aluminum blocks.
These jaws are a good starting point, but they may not be ideal for specialized jobs or high-volume production.
2. Quick-Change Jaws
If your shop handles many different parts in a day, quick-change jaws can be a game changer. They allow you to swap jaws rapidly without disassembling the chuck.
-
Great for repetitive tasks that involve changing part sizes.
-
Reduces downtime and increases throughput.
-
Often used with power chucks and automation setups.
Case Study: A mid-size factory increased production speed by 15% after switching to quick-change jaws for their CNC lathes.
These jaws are perfect for high-mix, low-volume operations where flexibility matters.
3. Custom or Special Jaws
Sometimes, standard jaws won’t do the job. That’s when custom or special jaws come into play. These are designed to fit non-standard or complex-shaped parts.
-
Can be made from steel, aluminum, or even polymers.
-
Used in aerospace, medical, and jewelry applications.
-
Perfect for delicate or highly detailed parts.
Real-World Example: An aerospace manufacturer uses special jaws to hold turbine blades during precise finishing work. These jaws are custom-shaped to the part’s complex profile.
Custom jaws ensure a secure grip without damaging the workpiece.
4. Under-Size and Over-Size Jaws
These jaws are made to handle parts that don’t fit the “normal” range of sizes.
-
Under-size jaws securely grip smaller components, preventing slippage.
-
Over-size jaws offer more clearance and stability for large or oddly shaped parts.
Such jaws are critical for applications where tight tolerances or special setups are needed.
Materials Used in Lathe Chuck Jaws
Choosing the right jaw material is just as important as the jaw type. The material affects everything from durability to part quality.
1. Steel
Steel is the most common material for lathe chuck jaws.
-
High strength and wear resistance.
-
Suitable for heavy-duty and repetitive use.
-
Long-lasting but heavier than other materials.
Expert Insight: “Steel jaws last longer and provide excellent grip, but may be too heavy for delicate parts.”
Great for production shops working with hard metals.
2. Cast Iron
Cast iron is a cost-effective and vibration-dampening material.
-
Good for light-duty jobs and softer materials.
-
Helps reduce noise during machining.
-
Can crack under high stress or impact.
Best suited for hobbyist setups or low-volume runs.
3. Aluminum
Aluminum jaws are lightweight and easy to machine.
-
Excellent for small or delicate parts.
-
Prevents marring on soft metals.
-
Less durable and wears faster than steel.
Ideal for electronics, jewelry, or precision hobby work.
4. Specialty Materials
In some cases, manufacturers use special materials to meet unique machining needs:
-
Tungsten carbide: Extremely hard and wear-resistant, ideal for abrasive or ultra-precise work.
-
Rubber or polymers: Used to grip fragile parts like glass or soft plastics.
Usage Tip: Always match your jaw material to your workpiece for best results. This prevents slippage, damage, and unnecessary tool wear.
Applications of Lathe Chuck Jaws
Chuck jaws are used in many industries and for many purposes—from mass manufacturing to delicate handmade crafts.
1. Manufacturing
Lathe chuck jaws are essential in high-volume manufacturing.
-
Used for holding metal rods, shafts, and discs during turning or drilling.
-
Quick-change and custom jaws help speed up cycle times.
Illustration: In the automotive industry, chuck jaws are used to grip bolts, gears, and shafts for mass production with tight tolerances.
2. Repair and Maintenance
Repair shops often handle irregular or worn-out parts. Standard jaws may not provide the grip needed.
-
Custom jaws can be shaped to hold broken or asymmetrical parts.
-
Jaws made of aluminum or polymer help protect delicate components.
Example: A repair technician uses custom soft jaws to hold a bent shaft during straightening without adding more damage.
3. Artistic and Hobbyist Work
Artists and hobbyists often work with small, delicate items.
-
Use soft jaws or aluminum jaws to avoid scratching.
-
Ideal for shaping wood, brass, copper, and precious metals.
Case: Jewelry makers prefer soft aluminum jaws to securely hold gold or silver rings without leaving tool marks.
Soft jaws offer both control and protection during creative work.
Industry Insights
Lathe chuck jaws might seem like a small part of machining, but they make a big difference in the quality and speed of your work.
-
The right jaws reduce setup time—you can start machining faster and finish with better precision.
-
Material choice affects quality—soft materials protect parts, while hard ones extend tool life.
-
Jaw design matches your workflow—quick-change jaws help scale operations, and custom jaws solve niche problems.
Expert Quote: “Choosing the right jaws cuts setup time and improves finish. It’s one of the smartest upgrades any machinist can make.”
Conclusion
Lathe chuck jaws are critical to safe, precise, and efficient machining. Whether you're working on large industrial parts or delicate craft pieces, choosing the right type and material of jaw can make all the difference.
Here’s a quick recap:
-
Use standard jaws for general work.
-
Choose quick-change jaws to save time during production.
-
Go with custom jaws for special shapes or fragile parts.
-
Pick steel for strength, aluminum for softness, and cast iron for light-duty jobs.
Also, don’t forget about jaw maintenance. Regular inspection, cleaning, and alignment will extend jaw life and protect your machine.
Final Tip: Always match the jaw to the task. This small step can lead to better finishes, faster output, and fewer machining problems.
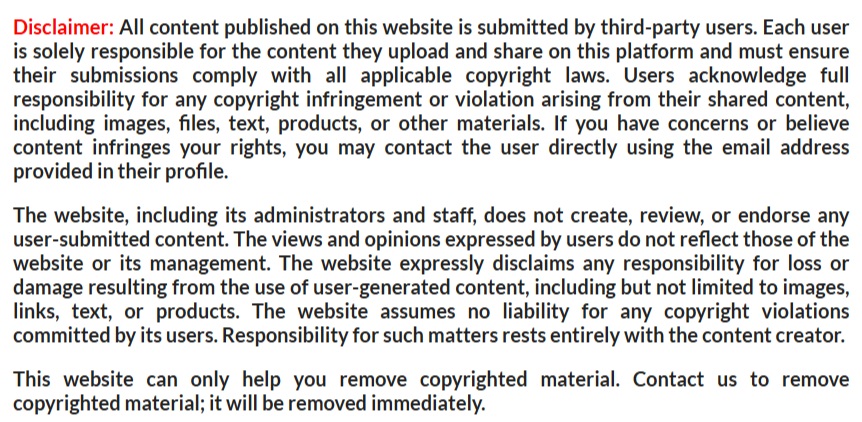