views
Let’s unpack the significance and real-world utility of this technology across various domains of application and the transformations it is driving in the world of fabrication.
The Changing Landscape of Welding
Manufacturing demands have evolved. Industries like aerospace, automotive, electronics, medical devices, and defense now require components that are not just structurally sound but also lighter, more compact, and precisely finished. Traditional welding techniques—like MIG, TIG, and arc welding—while reliable, often fall short when it comes to micro-precision or working with sensitive materials. That’s where laser welding equipment steps in.
Unlike conventional techniques, this method uses a highly focused laser beam to fuse metal surfaces, making it possible to join thin materials or extremely small parts without distortion or overheating adjacent zones. It has redefined what’s possible in sectors where failure or micro-cracks can lead to catastrophic outcomes.
Application Versatility of Laser Welding Equipment
Laser welding isn’t confined to one niche. It is reshaping multiple industries at once:
1. Automotive Manufacturing
Laser welding equipment is heavily used for joining car body parts, battery components, and gear assemblies. With electric vehicles becoming more common, there’s an increased need for lightweight, high-strength connections, especially in battery housing and thermal systems. The technology enables deep penetration welds without the need for pre-heating or multiple passes.
2. Aerospace and Aviation
Aircraft components often involve exotic metals and complex geometries. Laser welding is ideal for working with titanium and Inconel alloys. It ensures precise welds without adding unnecessary weight—a critical factor for airworthiness and fuel efficiency.
3. Electronics and Micro Components
In the electronics industry, size is everything. From mobile device parts to battery connectors and internal components of computers, the joints must be incredibly fine yet durable. Laser welding equipment handles this with pinpoint accuracy.
4. Medical Device Fabrication
Surgical tools, implants, and diagnostic devices are subject to strict safety standards. Weld integrity is non-negotiable. Laser welds are non-porous and free from contaminants, ensuring that medical-grade stainless steel or titanium parts meet all hygiene and strength requirements.
5. Tool and Die Making
Repairing expensive molds and dies with traditional methods used to be time-consuming. Now, laser welding equipment offers localized heat application, which allows precision patching and refurbishing of tools without compromising their geometry.
Why Industries Are Transitioning to Laser Welding Equipment
Many organizations have either switched or are considering the transition toward laser-based joining processes for a few compelling operational reasons—none of which are merely cosmetic improvements. The core motivation is manufacturing excellence. When weld precision equals product reliability, laser technology becomes indispensable.
One of the most common challenges manufacturers face is thermal distortion in fine parts. Traditional welding can cause deformation due to excessive heat input. Laser welding resolves this by offering a concentrated heat source with minimal heat-affected zones. This improves product consistency across high-volume production runs.
Moreover, automation compatibility is another key driver. Laser welding systems integrate seamlessly with robotic arms and CNC platforms. This allows for 24/7 operations without human error, leading to higher productivity and improved ROI over time.
In highly regulated industries, traceability and documentation are important. Laser welding systems often come with software that records parameters such as energy input, weld depth, and duration. This data proves invaluable for audits, certifications, and continuous improvement initiatives.
Types of Laser Welding Equipment in Use
Understanding the different types of laser welding systems helps determine what suits specific applications:
1. Fiber Laser Welding Machines
These are most widely used today. They offer high beam quality and energy efficiency and are great for both thick and thin materials. Their flexibility allows deep penetration welds, ideal for structural and load-bearing parts.
2. CO₂ Laser Welders
Although now less common in industrial use due to fiber laser advancements, CO₂ lasers still find use in certain materials like plastics and ceramics where absorption rates match better.
3. Nd:YAG Laser Welders
These systems are used in applications where pulsed output is beneficial—such as jewelry welding, small part repair, or mold refurbishing.
4. Handheld Laser Welders
Gaining popularity in workshops and field service applications, these portable systems allow for flexible operations where fixed systems aren’t feasible. They're suited for on-site repairs or custom workpieces.
Cost vs. Value: Is the Investment Justified?
The upfront cost of laser welding equipment may be higher compared to traditional machines. However, focusing solely on the initial price tag can be misleading. The real question is: What is the value over the machine’s operational life?
Here’s a straightforward breakdown:
-
Reduced material wastage due to precise targeting
-
Minimal post-processing, as the welds are cleaner
-
Shorter production cycles, thanks to automation and speed
-
Increased component reliability, reducing returns and warranty claims
-
Smaller footprint, since fewer auxiliary tools are needed
Companies that factor in long-term savings, improved output quality, and compliance with international standards often find laser welding equipment to be a strategic asset rather than a sunk cost.
Common Questions Industry Professionals Ask
“Can it replace all my existing welding processes?”
Not necessarily. Laser welding is most effective when the job requires precision, repeatability, and minimal thermal input. For heavy structural fabrication or outdoor work, traditional methods may still be relevant.
“What training is required for operating laser welding equipment?”
Modern systems are increasingly user-friendly. With a short training period, operators can manage interface settings, safety parameters, and routine maintenance. Many machines also offer presets for common materials and joints.
“What about safety?”
Laser systems come with enclosed workstations or protective shielding. Proper eyewear, ventilation, and safety interlocks are part of standard setups. When used correctly, laser welding is safe and more controlled compared to open-arc processes.
Future of Laser Welding Equipment
The integration of AI vision systems, real-time monitoring, and adaptive control is pushing the boundaries of what laser welding equipment can achieve. While this article doesn’t delve into AI specifics, the point is clear: precision manufacturing is heading toward more intelligent, adaptable processes. Laser welding sits at the heart of this evolution.
Industries are also pushing for greener manufacturing. Laser welding reduces consumables like electrodes and shielding gases, lowers power consumption for many applications, and produces cleaner seams that require less finishing—all of which contribute to sustainable operations.
Final Thoughts
Deciding whether laser welding equipment is worth the investment comes down to business goals, manufacturing complexity, and desired quality levels. For companies involved in high-precision, high-throughput, or highly regulated production environments, the move to laser welding is less of an option and more of a necessity. As industries continue to evolve, those equipped with advanced joining technologies will lead the way—not just in output, but in quality, consistency, and future-readiness.
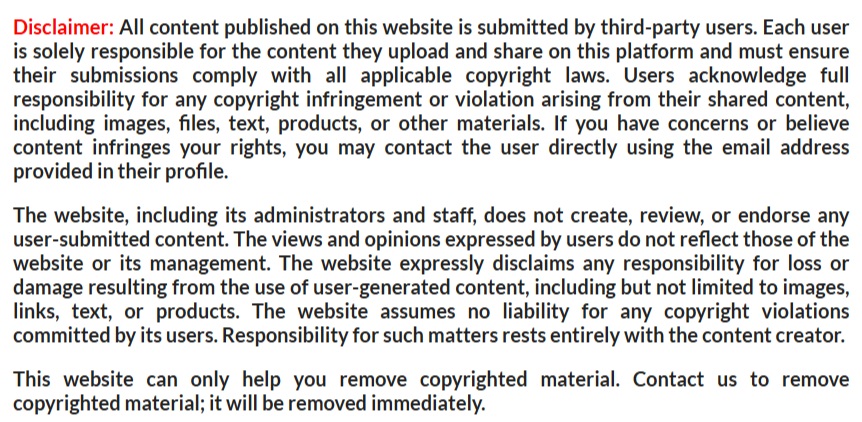