views
Every transformer tells a story. Not the kind with words—but with wire, steel, and purpose.
In a power-hungry world where downtime costs money, the journey from raw material to finished transformer is more than a factory process—it’s a promise of performance. And that journey, across India’s growing industrial hubs, starts with a clear goal: reliable, efficient, long-lasting power for industries like textile processing, OEMs, utilities, and exporters.
1. The Problem First
Great transformer manufacturing begins with a conversation. What's the voltage range? What kind of load will it handle? Will it run 24/7 or in bursts? These details help tailor each design to real-world needs—whether it’s a dyeing unit in Coimbatore or an automation plant in Pune.
2. Design is the Brain
Once the need is clear, engineers design the heart of the machine. They run tests and models, tweak specs, and optimize the transformer for efficiency and durability. The blueprint becomes the brain of the build.
3. Materials Matter Most
No shortcuts. The best makers use top-grade copper, laminated steel cores, and high-grade insulation—sourced from tested suppliers. These parts may seem small, but they decide whether the final transformer lasts 10 years—or 25.
4. Making the Coil
In the winding section, copper wires are coiled with precision. The tension, spacing, and insulation must be just right. Each turn affects performance. Skilled technicians guide the machines, checking each layer for accuracy.
5. Assembly & Drying
The wound coils go through drying ovens to remove moisture—because even a small trace can ruin performance. After that, vacuum pressure impregnation (VPI) adds extra protection.
Then, it all comes together: core, windings, tank, and clamps—assembled into one strong unit.
6. Testing Without Compromise
Now comes the moment of truth. Transformers are tested for insulation, heating, voltage stability, and short-circuit resistance. Some makers go beyond standard checks—because reputation depends on zero-failure rates.
7. Packing, Shipping & Support
The final transformer is sealed, packed, and delivered. But it doesn’t end there. Reliable manufacturers offer on-site support, spares, and servicing. Because customers don’t just want a transformer—they want someone who stands behind it.
In a world moving fast, power can’t afford to fail. The next time you pass a working plant or an export machine, remember: there’s a transformer inside, quietly doing its job—built by people who take every coil seriously.
👉 Want to see how it's done right?
🔗 Jindal Electric & Machinery Corporation
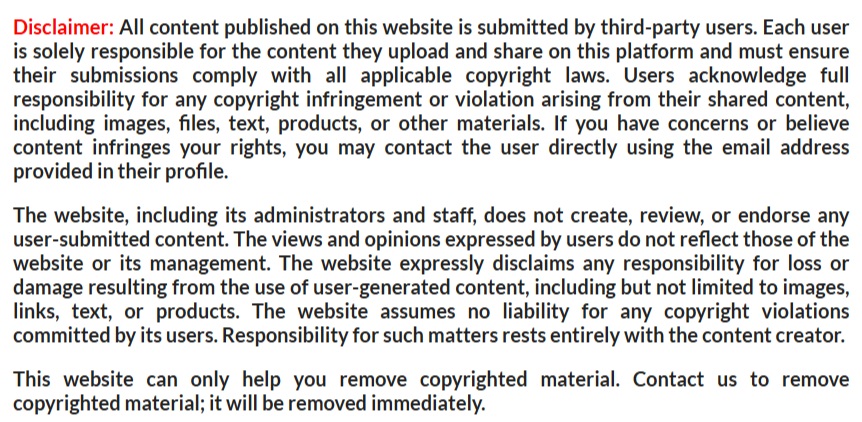