views
In today’s fast-evolving construction industry, choosing the right building material is crucial for durability, cost-effectiveness, and sustainability. For decades, red bricks dominated the market—but with technological advancements and growing environmental concerns, AAC blocks (Autoclaved Aerated Concrete) are rapidly emerging as the smarter alternative.
In this article, we compare AAC blocks and traditional red bricks in terms of strength, cost, installation, and sustainability, helping builders, developers, and contractors make an informed choice.
🧱 What Are AAC Blocks?
AAC Blocks (Autoclaved Aerated Concrete Blocks) are lightweight, precast foam concrete building blocks manufactured using a mixture of fly ash, cement, lime, aluminum powder, and water. These blocks are cured in AAC block machinery using high-pressure steam in autoclaves.
Manufactured in large-scale AAC block plants, these blocks are known for their high thermal insulation, lightweight structure, and eco-friendly properties.
🔴 What Are Red Bricks?
Red bricks are traditional building materials made from natural clay, shaped into rectangular forms and baked in kilns. While still widely used in rural and semi-urban construction, they have several limitations when compared to modern materials like AAC.
⚖️ AAC Blocks vs. Red Bricks: A Detailed Comparison
🏗️ Why AAC Blocks Are Gaining Popularity
✅ 1. Lightweight and Easy to Install
AAC blocks weigh significantly less than red bricks, reducing structural load and allowing for quicker construction. Many contractors working with small AAC block plants report up to 30% faster building time.
✅ 2. Energy Efficiency
AAC provides excellent insulation, keeping interiors cooler in summer and warmer in winter—reducing the need for air conditioning and saving energy.
✅ 3. Sustainability Matters
With increased focus on green construction, AAC blocks made in AAC block machinery using fly ash and less water are a clear winner. Leading AAC plant suppliers now offer fully automated AAC plant machinery that ensures minimal waste generation.
✅ 4. High ROI with Lower Long-Term Costs
Although AAC block plant cost may seem higher upfront, the overall building cost is reduced due to lower labor, faster construction, and long-term energy savings.
🏭 AAC Block Manufacturing: How It Works
AAC blocks are manufactured in industrial AAC block plants using specialized AAC machines and AAC plant machines. The process includes:
-
Batching and Mixing: Raw materials are mixed precisely.
-
Pouring and Pre-curing: The mix is poured into molds and allowed to set.
-
Cutting: High-precision cutting machines shape the blocks.
-
Autoclaving: Blocks are steam-cured in autoclaves for strength and durability.
-
Packaging: Finished blocks are stacked and shipped.
Whether it’s a small AAC block plant or a large-scale unit, automation and efficiency are ensured with modern AAC plant machinery. Leading companies are even establishing AAC plants in Hyderabad, Gujarat, and across India to meet growing demand.
💸 AAC Block Plant Cost vs. Traditional Brick Kilns
Setting up an AAC block manufacturing plant involves investing in specialized AAC machines and infrastructure. While the AAC block plant cost is higher than a traditional brick kiln, the profit margin, scalability, and demand make it a wise long-term investment.
Additionally, AAC blocks in India are supported by various green building programs, increasing market potential.
🔚 Conclusion: AAC Blocks Are the Future of Sustainable Construction
From durability and thermal efficiency to faster construction and eco-friendliness, AAC blocks clearly outshine traditional red bricks in almost every aspect. Backed by reliable AAC block machinery, modern AAC block plants, and superior AAC plant machines, builders today have access to a revolutionary material that meets both economic and environmental goals.
If you're considering setting up an AAC plant or upgrading your production capacity, trust industry leaders like Buildmate. As one of the most trusted AAC plant suppliers in India, Buildmate offers end-to-end solutions—from AAC plant machinery to custom-built small AAC block plants tailored to your requirements.
Explore their offerings, compare AAC block plant cost, and take a step toward sustainable construction today.

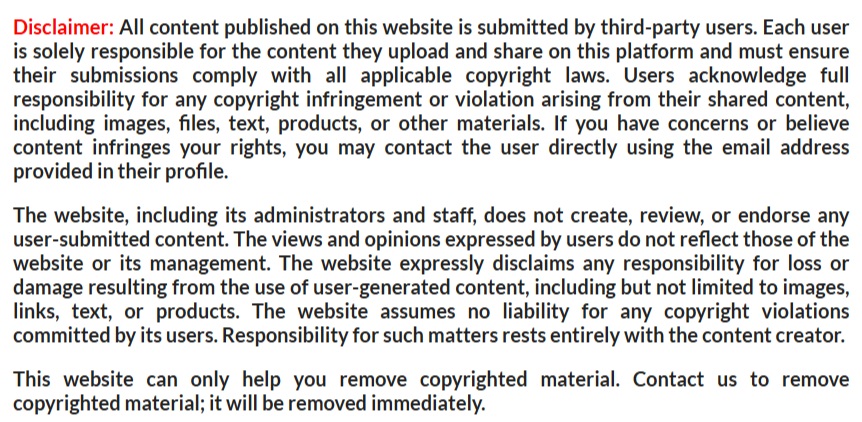