views
In pharmaceutical drug manufacturing, pure water is not just important—it’s essential. It is used in nearly every step of the process: from cleaning of equipment and production vessels to acting as a solvent or raw material in drug formulation. The purity of this water has a direct impact on product quality, patient safety, and regulatory compliance. Contaminated or inadequately treated water can introduce microorganisms, endotoxins, and chemical residues that compromise drug stability and safety. Therefore, pharmaceutical manufacturers rely on high-performance water systems like Pharmaceutical Pretreatment Water Plants, Purified Water Generation Systems, Ultrafiltration Water Systems, WFI Systems,and Pure Steam Generator System, many of which are developed by expert WFI System Manufacturers in India.
Purified Water Generation Systems: Backbone of Non-Sterile Drug Manufacturing
A Purified Water Generation System plays a central role in producing water that is suitable for use in the manufacture of non-sterile pharmaceutical products such as tablets, syrups, creams, and ointments. These systems combine multiple advanced technologies to achieve the required purity levels. Typically, the process begins with Reverse Osmosis (RO), which removes dissolved salts and organics from water. This is followed by Electrodeionization (EDI), which ensures consistent removal of ionic contaminants without the need for chemical regeneration.
In addition to the RO-EDI system, most systems also include Ultraviolet (UV) disinfection units, which inactivate bacteria and viruses by damaging their DNA. Finally, an Ultrafiltration Water System is often integrated to remove endotoxins and microscopic impurities. The purified water produced is then used for various manufacturing steps including dissolution of active pharmaceutical ingredients (APIs), equipment cleaning, and preparation of excipients. These systems ensure the water complies with pharmacopeial standards like USP and EP, which are critical for drug safety and international approvals.
WFI (Water for Injection) System: For Sterile and Injectable Products
When it comes to producing injectable drugs, IV fluids, ophthalmic solutions, or biopharmaceutical products, water purity must meet the highest possible standards. This is where Water for Injection (WFI) comes in. WFI is free from bacteria, endotoxins, and all dissolved impurities. It is usually generated by Multi-Effect Distillation (MED) or Vapor Compression Distillation (VCD).
A WFI System Manufacturer in India, such as SWJAL PURE PROCESS, designs these systems to operate under cGMP guidelines, ensuring continuous and validated production. WFI is typically stored in sanitary stainless-steel tanks and circulated in loop systems with hot water sanitization or ozone/UV disinfection to prevent microbial regrowth.
The WFI system is essential for the production of:
Injectable medications (ampoules, vials, pre-filled syringes)
Ophthalmic solutions and nasal sprays
Vaccines and plasma-based products
Biotech and biosimilar drug formulations
Pharmaceutical Pre treatment Water Plant: The First Defense Line
Before any water enters a high-end purification or WFI system, it must be pretreated to ensure it doesn’t damage sensitive membranes or equipment. A Pharmaceutical Pretreatment Water Plant removes basic but harmful impurities like suspended particles, chlorine, hardness, and organic matter. If not treated properly, these contaminants can clog membranes and lead to microbial fouling in downstream systems.
One essential step in this process is NaOCl dosing in water treatment. Sodium hypochlorite (NaOCl) is a powerful disinfectant that kills bacteria and prevents biofilm formation in storage tanks and piping. In pretreatment, NaOCl dosing ensures that microbial load is controlled before the water reaches RO membranes. Additionally, activated carbon filters are used to remove excess chlorine to protect the membranes, and softeners are used to reduce scaling caused by calcium and magnesium.
These pretreatment stages play a vital role in protecting the core purified water and WFI, ensuring long-term operational efficiency, reduced maintenance, and superior water quality.
Ultrafiltration Water Systems: Endotoxin and Microbial Control
Even after primary purification, microbial control remains a challenge, especially in the water distribution loops and storage tanks. This is where Ultrafiltration comes in. These systems are designed to remove extremely small particles, including bacteria, endotoxins, viruses, and pyrogens, which are critical in injectable product safety.
Ultrafiltration membranes act as a final barrier before water enters the manufacturing area or during loop recirculation. In both Purified Water and WFI, UF modules ensure consistent microbial control without using chemicals. These systems are also beneficial for maintaining low endotoxin levels during Clean-in-Place (CIP) and Sterilization-in-Place (SIP) processes. This is especially vital in manufacturing biotech products, sterile injectables, and ophthalmics, where microbial contamination can be life-threatening.
Conclusion: Pure Water Ensures Pure Medicine
Purified water treatment systems are central to every pharmaceutical manufacturing process. From pretreatment with NaOCl dosing, to Purified Water Generation, Ultrafiltration, and WFI production, each stage of water treatment protects drug quality and public health. These plants ensure adherence to global regulatory standards while enhancing operational efficiency and minimizing risks.
Partnering with an experienced WFI System Manufacturer in India ensures access to validated, automated, and compliant systems that meet the highest industry expectations. With patient safety on the line, investing in pharmaceutical-grade water systems is not just a requirement—it’s a responsibility.
Swjal pure process is the one of the best Ultrafiltration Water System Manufacturer in India. Providing advanced solutions tailored to modern industrial and pharmaceutical demands.
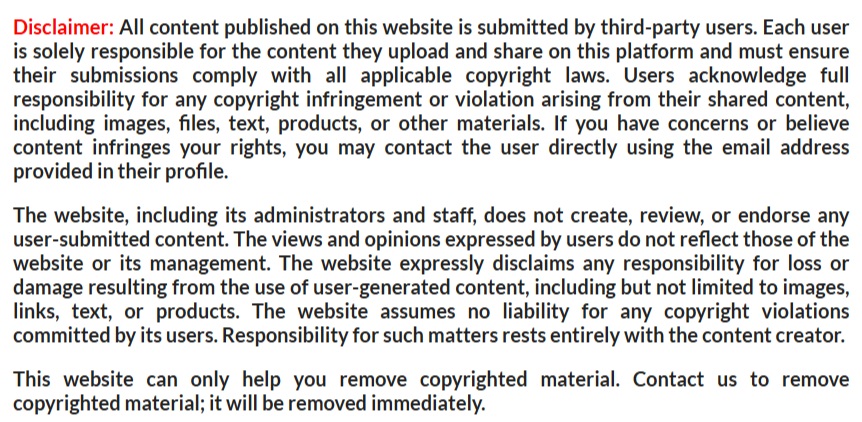