views
In the world of precision manufacturing, clear and accurate communication is essential to building components that meet functional and assembly requirements. That’s where GD&T—Geometric Dimensioning and Tolerancing—comes into play. It’s more than just symbols and numbers on a drawing; GD&T is a universal language that enables design intent to be effectively conveyed from engineers to machinists and inspectors. For those unfamiliar with this powerful system, our detailed guide on what is gd&t will provide everything you need to understand its value, structure, and application.
Understanding the Basics of GD&T
GD&T stands for Geometric Dimensioning and Tolerancing, a standardized system (defined by ASME Y14.5) used to describe the allowable variation in part geometry. Unlike traditional tolerancing, which relies on linear dimensions with ± values, GD&T specifies allowable deviation zones through geometric symbols and datum references.
Why GD&T Matters:
-
Improves communication across departments and suppliers
-
Ensures interchangeability of parts
-
Reduces inspection ambiguity
-
Enhances design functionality and intent
It enables designers to define exactly how features should be manufactured and measured—based on how they function within an assembly.
Traditional Tolerancing vs GD&T
Traditional Tolerancing
Uses ± values to define the size and location of a feature. It assumes interpretation in a 2D space, which can lead to multiple components passing inspection but still failing to assemble properly.
GD&T
Defines a tolerance zone that limits the allowable deviation of a feature’s shape, orientation, and location—typically in a 3D space—relative to reference datums. It is more precise and aligns better with functional intent.
Key Elements of the GD&T System
GD&T operates through a system of symbols, feature control frames, datums, and tolerance modifiers, each of which plays a specific role in describing how a feature is controlled.
1. Geometric Symbols
There are 14 primary symbols, grouped into five tolerance types:
Tolerance Type | Symbols |
---|---|
Form | Flatness, Straightness, Circularity, Cylindricity |
Orientation | Perpendicularity, Parallelism, Angularity |
Location | Position, Concentricity, Symmetry |
Profile | Profile of a Line, Profile of a Surface |
Runout | Circular Runout, Total Runout |
Each symbol represents a specific kind of geometric control applied to a feature.
2. Feature Control Frame (FCF)
The FCF is a rectangular box containing:
-
The geometric symbol
-
Tolerance value
-
Material condition modifier (optional)
-
Datum references (if needed)
It defines how the feature is controlled and relative to what references.
3. Datums
Datums are theoretical planes, lines, or points used as references for measuring features. These act like the coordinate system for a part. They ensure consistent interpretation between design, manufacturing, and inspection.
4. Material Condition Modifiers
These include:
-
MMC (Maximum Material Condition)
-
LMC (Least Material Condition)
-
RFS (Regardless of Feature Size)
Modifiers allow for bonus tolerance and flexibility during inspection depending on the actual size of the feature.
Benefits of Using GD&T
Using GD&T over traditional tolerancing offers a range of functional, economic, and quality-based benefits:
1. Functional Clarity
GD&T focuses on how a part fits and functions, not just its measured location or size. This reduces ambiguity during manufacturing.
2. Improved Quality
Features are held to the specific geometric tolerances required, which leads to fewer nonconforming parts.
3. Cost Efficiency
GD&T allows for more generous tolerances in non-critical areas and tighter control only where needed—reducing unnecessary precision costs.
4. Better Supplier Communication
Because GD&T is standardized, international suppliers and partners can interpret drawings without confusion.
5. Enhanced Inspection
It aligns with modern inspection methods like CMMs (Coordinate Measuring Machines), allowing automation and faster throughput.
Common GD&T Applications
GD&T is widely used across high-precision industries, including:
-
Aerospace: Where alignment, fit, and function are critical to safety and performance.
-
Automotive: Ensures parts fit within the vehicle system and reduces vibration.
-
Medical Devices: Demands ultra-high tolerances and repeatability.
-
Defense: Maintains part reliability under extreme conditions.
-
Robotics & Automation: Parts must be interchangeable and responsive to movement.
Real-World Example
Let’s say a hole must be drilled into a part to accept a pin from another part. In traditional tolerancing, the hole location might be given as X and Y coordinates with ±0.05 mm tolerance. However, this does not control how “true” the hole position is relative to a reference feature.
In GD&T, this same hole could use a Position tolerance with MMC and datum references, ensuring the hole is located precisely, functions correctly, and can still pass inspection if it's at its maximum size.
Common Mistakes to Avoid
1. Over-Tolerancing
Specifying unnecessarily tight tolerances increases production costs and inspection complexity.
2. Poor Datum Selection
Datums should reflect how the part is functionally assembled, not just convenient measurement locations.
3. Ignoring Measurement Capability
Tolerances must be practically measurable using the shop’s inspection equipment.
4. Misinterpretation
Without GD&T training, misreading a control frame could lead to part rejection or poor assembly performance.
Integrating GD&T in Modern Engineering
Most modern CAD software such as SolidWorks, AutoCAD, Siemens NX, and CATIA support GD&T annotation, enabling you to define tolerances directly within the 3D model. CAM software can then generate appropriate toolpaths, and inspection software can evaluate tolerances automatically using CMMs.
This digital integration reduces human error, speeds up production, and improves traceability across the product lifecycle.
Who Should Learn GD&T?
Anyone working in engineering or manufacturing should understand GD&T fundamentals:
-
Design Engineers – to communicate functional intent
-
CNC Machinists – to produce parts that meet design requirements
-
Quality Inspectors – to verify tolerances during inspection
-
Suppliers & Vendors – to interpret drawings without delays
Formal GD&T certification is available from organizations such as ASME, SAE, and third-party platforms like GD&T Basics.
Conclusion
GD&T is not just for large manufacturers—it's a critical tool for any company that designs or produces parts requiring precision, consistency, and performance. From improving design communication to streamlining inspection and reducing costs, GD&T offers immense value across the product development cycle.
By adopting GD&T, organizations can reduce scrap rates, shorten lead times, and maintain the dimensional quality of parts throughout manufacturing and assembly. It’s an investment in quality and professionalism that pays off in both productivity and performance.
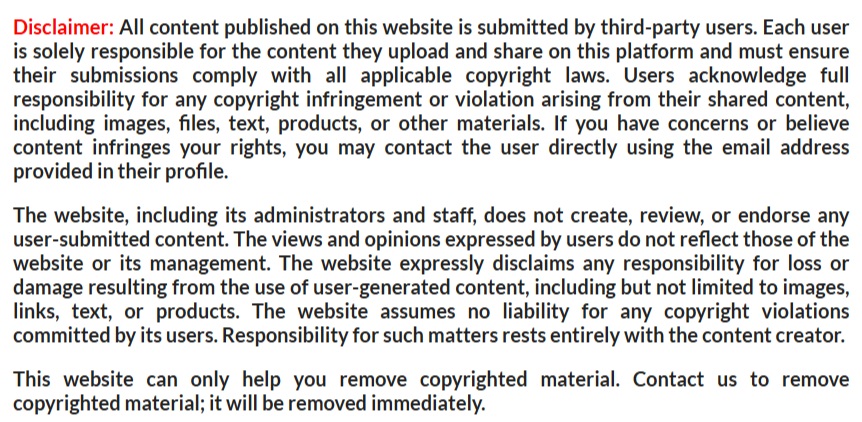