views
MTBF Prediction Tool: A Practical Guide to Enhancing Product Reliability
In today’s competitive technology-driven world, product reliability is more critical than ever. Manufacturers and developers face immense pressure to produce dependable systems that perform flawlessly over time. One of the most trusted methods to measure and forecast system reliability is through MTBF prediction and tools designed for this purpose have become essential across industries.
If you’re an engineer, quality assurance manager, or product developer looking to improve the reliability of your electronic or mechanical systems, understanding and using an MTBF prediction tool can make a significant difference in how you design, test, and refine your products.
What is MTBF?
MTBF, or Mean Time Between Failures, is a key reliability metric used to estimate the average operational time between inherent failures of a system or component. Typically measured in hours, it offers insights into the expected lifespan and performance stability of a product.
For example, if a circuit board has an MTBF of 200,000 hours, it means on average one failure is expected after every 200,000 hours of operation (assuming the failure is random and not due to wear-out).
Why MTBF Matters
-
Predictability: Knowing when a failure might occur helps in proactive maintenance and risk mitigation.
-
Cost Savings: Reduces warranty claims, downtime, and maintenance costs.
-
Product Confidence: Customers trust products with high MTBF ratings.
-
Compliance & Standards: Many industries, like aerospace and telecommunications, require MTBF values as part of safety and compliance checks.
What is an MTBF Prediction Tool?
An MTBF prediction tool is a specialized software or platform that calculates the expected MTBF of a product based on various inputs — component-level data, usage environments, failure rate databases, and design specifications.
Rather than performing manual calculations (which can be time-consuming and error-prone), these tools automate the process, using established reliability prediction standards such as:
-
Telcordia SR-332 (formerly Bellcore)
-
MIL-HDBK-217F (U.S. Military Handbook)
-
IEC TR 62380 / FIDES
-
NSWC Mechanical Handbook
How It Works
The tool gathers input from:
-
Component part numbers
-
Electrical and thermal stress factors
-
Environmental conditions (temperature, humidity, vibration)
-
Operating time
-
Reliability prediction standard selected
It then processes the data using failure rate models to deliver a predicted MTBF value, failure rates (FIT – Failures in Time), and confidence levels.
Key Features of an Effective MTBF Prediction Tool
When choosing an MTBF prediction tool, look for these features to ensure reliable outcomes:
1. Support for Multiple Standards
A robust tool should offer predictions using Telcordia, MIL-HDBK-217, and IEC standards to suit different industry requirements.
2. Component Libraries & Databases
Built-in access to comprehensive parts databases (like Siemens, Vishay, TI, etc.) can streamline data entry and improve accuracy.
3. Environmental Stress Profiles
The tool should model real-world operational environments such as airborne, ground-mobile, naval, or telecom conditions — to reflect actual use cases.
4. Thermal Analysis
MTBF calculations are highly sensitive to temperature. Tools with thermal modeling or integration with PCB layout software can enhance prediction accuracy.
5. User-Friendly Interface
Whether it's a desktop application or a cloud-based platform, an intuitive interface helps users efficiently upload BOMs (Bill of Materials), configure settings, and retrieve reports.
6. Exportable Reports
PDF or Excel reports with full failure rate breakdowns, assumptions, and MTBF charts aid internal reviews or client documentation.
Benefits of Using an MTBF Prediction Tool
Faster Time-to-Market
Design teams can assess and refine product reliability early in the design phase, speeding up development cycles.
Reduced Risk of Field Failures
Accurate predictions enable better quality control and minimize costly recalls or failures in mission-critical applications.
Informed Component Selection
By comparing component reliability, engineers can make smarter sourcing decisions that balance cost and durability.
Compliance Made Easy
Organizations can easily meet reliability requirements for industries like automotive, aerospace, telecom, and defense.
Who Should Use an MTBF Prediction Tool?
These tools are vital for a wide range of professionals and industries:
Role | How MTBF Prediction Helps |
---|---|
Design Engineers | Select components and materials with optimal reliability. |
Quality Assurance Teams | Ensure products meet or exceed reliability benchmarks. |
Maintenance Planners | Forecast maintenance schedules and reduce downtime. |
Procurement Teams | Choose suppliers offering reliable parts with lower failure rates. |
Product Managers | Validate product performance expectations before launch. |
Real-World Applications
Aerospace
Aircraft and satellite systems demand extreme reliability, where even one failure can have catastrophic consequences. MTBF tools ensure compliance with strict reliability standards.
Telecommunications
Service uptime is critical. MTBF prediction helps network equipment manufacturers optimize the reliability of routers, switches, and servers.
Automotive
From ECUs to infotainment systems, car manufacturers use MTBF predictions to extend vehicle lifespans and reduce warranty issues.
Medical Devices
MTBF helps predict equipment lifespans in high-usage environments where precision and uptime are vital for patient care.
Common Challenges with MTBF Predictions
While powerful, MTBF prediction tools also come with a few limitations:
-
Assumptions Matter: Predictions rely on estimated operating conditions. If these assumptions are inaccurate, so is the MTBF.
-
Not for Wear-Out Failures: MTBF doesn’t capture aging or wear-out mechanisms only random failures.
-
Requires Up-to-Date Libraries: Tools must be maintained with updated component failure data for accuracy.
To address these challenges, many companies rely on MTBF consultants or reliability engineers to fine-tune inputs and validate outcomes.
Choosing the Right MTBF Prediction Tool
Here’s a quick checklist when evaluating MTBF tools:
-
Supports your required standards (e.g., MIL-HDBK-217F, Telcordia)
-
Offers easy integration with your BOM or CAD tools
-
Regularly updated parts library
-
Suitable for your product type (electronics, mechanical, systems)
-
Provides support and training
If you’re unsure, working with a reliability consulting firm can help you choose the best tool and guide you through the analysis process.
Conclusion: Make MTBF Prediction Part of Your Design Workflow
Investing in an MTBF prediction tool is not just about avoiding failures it’s about building better, longer-lasting products. Whether you're developing a new consumer electronic device or mission-critical aerospace hardware, predicting reliability upfront empowers your team to make smarter design choices.
At Relteck we specialize in MTBF calculations, component analysis, and full-scale reliability assessments. Our experts use industry-leading MTBF tools to help clients predict, prevent, and outperform. Want to simplify your reliability strategy? Contact us today and let’s make your products more resilient, together.
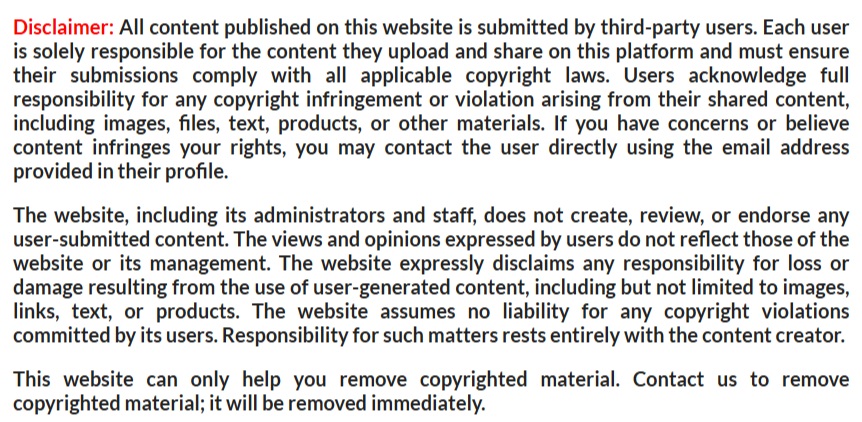