views
The Laser Welding Machine Market is gaining traction as manufacturers adopt environmentally sustainable practices. The demand for eco-friendly welding technology is on the rise, and laser welding stands out as a cleaner, energy-efficient alternative to traditional methods.
Eco-Friendly Production Becoming a Global Priority
Across industries, there is increasing emphasis on reducing environmental impact. Manufacturers are under pressure to meet carbon emission targets, minimize material waste, and comply with environmental regulations. These demands are driving the search for greener technologies on the production floor.
Laser welding supports this shift by using less energy, reducing emissions, and eliminating the need for filler materials and fluxes. Unlike arc or gas welding methods, laser welding operates with higher precision, reducing rework and improving energy efficiency. It generates less spatter and fumes, contributing to cleaner and safer work environments.
Advantages of Laser Welding for Sustainability
Laser welding offers several features that make it environmentally beneficial:
-
Lower energy consumption: The focused beam allows faster welds with minimal heat input.
-
Minimal material waste: High precision leads to fewer rejected parts and less scrap.
-
No consumables: It eliminates the need for filler rods, shielding gas, and other welding additives.
-
Cleaner operation: The process produces less smoke and fewer emissions, reducing air contamination.
-
Extended equipment life: Laser systems typically require less maintenance and have longer lifespans than conventional machines.
These advantages help manufacturers align with sustainability goals while improving operational efficiency.
Industry Sectors Leading the Green Transition
Automotive industry: Automakers are adopting laser welding for battery packs, lightweight chassis, and safety-critical joints. This shift supports both production speed and carbon footprint reduction. Electric vehicle production, in particular, benefits from cleaner, high-precision joining processes.
Electronics manufacturing: Laser welding is used in assembling compact electronic parts with minimal energy use and waste. The clean nature of the process is vital in sensitive environments like semiconductor and sensor production.
Medical device sector: Sterile manufacturing processes demand clean, particulate-free welds. Laser welding meets hygiene and sustainability needs, making it ideal for producing surgical instruments, implants, and diagnostic devices.
Consumer goods and appliances: Manufacturers of appliances and electronics are turning to laser welding to meet environmental compliance requirements while delivering high product quality and longevity.
Alignment with Global Sustainability Regulations
Governments and international bodies are tightening environmental regulations across the board. Emission caps, energy efficiency standards, and green manufacturing mandates are prompting industries to reconsider their processes. Laser welding allows companies to demonstrate compliance while maintaining productivity.
For example, the European Union’s Green Deal and various national-level decarbonization plans incentivize investment in cleaner technologies. Laser welding’s energy efficiency and clean operation help companies qualify for tax benefits, green certifications, and export readiness under stricter environmental norms.
Innovations Supporting Eco-Friendly Welding
Technological innovation is further enhancing the environmental credentials of laser welding machines. Fiber lasers, in particular, are more energy-efficient than older CO₂ laser systems. They offer better beam quality, faster processing speeds, and lower operational costs.
Some systems now include AI-powered process controls that reduce energy usage by adjusting power levels in real-time. Others incorporate hybrid welding functions that combine laser and arc welding for improved efficiency in thicker materials.
Portable and compact laser welding units also consume less energy and take up less space, reducing the total environmental footprint of manufacturing operations.
Challenges and Cost Considerations
Although the environmental advantages are clear, some challenges remain. The initial investment for laser welding machines is higher than that for traditional welding equipment. Additionally, integrating them into existing lines may require technical expertise and operator training.
However, these upfront costs are often offset over time through reduced energy bills, lower material consumption, minimal rework, and increased machine uptime. The long-term return on investment (ROI) makes laser welding a financially and environmentally sound decision.
Vendors are also working to lower the entry barrier by offering modular systems, flexible financing, and on-site training programs.
Market Outlook and Future Growth
The outlook for the laser welding machine market remains strong as sustainability becomes a top priority for manufacturers globally. From small enterprises to large-scale OEMs, companies are recognizing the need to reduce their environmental impact without sacrificing quality or efficiency.
As eco-labeling and green procurement practices gain prominence in global supply chains, using clean technologies like laser welding can enhance a company’s brand reputation and market access. Demand is expected to rise further as businesses look to align with environmental, social, and governance (ESG) goals.
In emerging markets, growing awareness and access to green technologies are also fueling adoption. International collaborations, government incentives, and rising consumer awareness are encouraging manufacturers to upgrade to laser-based systems.
Conclusion
The laser welding machine market is expanding, driven by a growing commitment to eco-friendly and sustainable manufacturing practices. With reduced energy usage, minimal waste, and cleaner operation, laser welding stands out as a responsible choice for industries aiming to lower their environmental footprint while maintaining operational excellence. As global sustainability standards tighten, adoption of this technology is expected to accelerate across sectors.
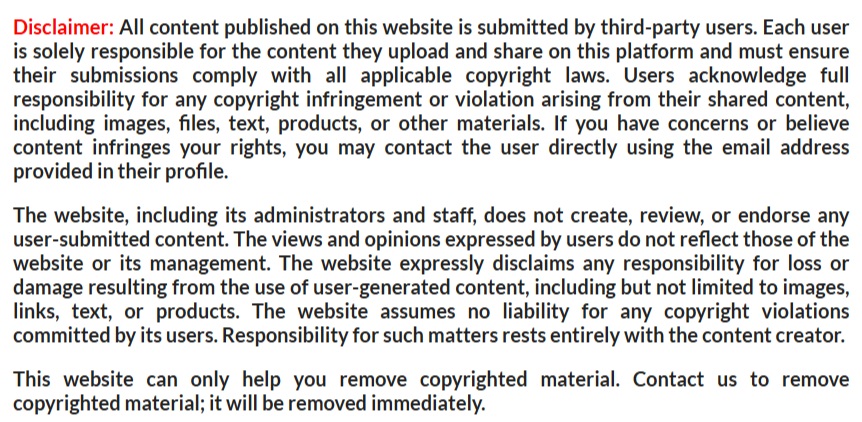