views
Real-time optimizations and overall improvements have been the highlights of AI adoption in operational and manufacturing ecosystems. However, far ahead of these temporary benefits, Artificial Intelligence (AI) is quietly weaving a cognitive industrial revolution. Though it is a slightly subdued pattern, the gradual shift from rigid automation is already visible in how adaptive systems are redefining human participation, supply chains, and production lines.
The integration of predictive maintenance and generative designs has delivered annual efficiency gains of up to 40% while reducing inventory costs by 20-30%, along with a 35-50% optimization of changeovers. In this article, we explore the current state, future scope, and stalling factors, as well as the type of strategic planning that could help industry players stay ahead of the curve.
AI in the Manufacturing Industry – The Status Quo
AI adoption in manufacturing has acquired significant momentum in the last few years. According to reports, 51% of manufacturers in the USA are currently employing AI in their operations, while over 61% expect increased investment in related technologies by 2027. These adoption patterns vary as per business function, application, and industry requirements.
Nevertheless, a substantial gap still exists between pilot projects and scaled-up global implementation. While stakeholders are taking initiatives to bridge this gap, a high percentage of companies still consider themselves amateurs when it comes to AI deployment. Therefore, a close assessment of advanced AI technologies’ impact on manufacturing is required to facilitate their adoption.

Which Advanced AI Technologies are Reshaping the Manufacturing World?
Machine Learning
A comprehensive array of breakthrough technologies is powering the cognitive industrial revolution. Most of these technologies are reaching market maturity and signaling a more intelligent and responsive industrial ecosystem in the near future.
- Deep Learning Algorithms: Now, they can process the most complicated manufacturing data with utmost precision, empowering manufacturers with predictive insights that are far ahead of traditional approaches. They capture complex relationships autonomously from high-dimensional data, including sensor streams, point clouds, and images, thereby eliminating the need for handcrafted extraction
- Neural Networks: In manufacturing applications, neural networks enable sophisticated automation capabilities, including quality control, predictive maintenance, and process optimization. They can analyze massive sets of sensor data to decode patterns indicating quality deviations and potential failures. Recent research demonstrated that neural networks are capable of achieving up to 96.58% accuracy in assessing the quality of the manufactured components, impacting over a dozen performance indicators directly
- Reinforcement Learning: A very promising frontier when it comes to manufacturing, as systems self-teach optimal behavior through trial-and-error interaction with their ecosystem. Studies demonstrate that reinforcement learning-powered control systems achieve up to a 30.5% reduction in task completion timeline, 41.2% fewer error rates, and approximately 20.5% improved energy efficiency
Generative AI in Manufacturing: Reviving Design and Production
Gen AI is transforming production and design processes in the industrial sector. The advanced machine learning techniques employed assist in creating new designs, content, solutions, and simulations based on identified data patterns. From automating design generation to enabling performance-driven prototyping and large-scale optimization, it is writing a new playbook for manufacturing. Leading industry players, such as Bosch, are utilizing it to compress their design cycles, optimize material usage, and enhance product performance through AI-based iteration and simulation.
Also read GenAI Changing the Manufacturing Landscape
Edge AI and Distributed Intelligence
Edge AI has emerged as one of the key enablers of cognitive manufacturing by bringing AI-powered processing directly to assembly lines and factory floors. The extensive range of its benefits encompasses real-time processing, enhanced security, scalability, and reliability. As 5G connectivity joins the mainstream world, its convergence with edge AI is weaving ultra-high-speed networks that can support the most demanding AI workloads on manufacturing equipment.

Infusing Intelligence: Most Promising AI Applications in Manufacturing
Predictive Maintenance: The Shift from Reactive to Cognitive
The use of AI for predictive maintenance in manufacturing represents one of the most mature applications of advanced intelligence in this space. AI-based predictive maintenance frameworks assess sensor data relayed from machinery to predict failures on a prior basis. It can reduce downtime by 30-50% while extending the lifespan of machinery. A fine example of this cognitive approach can be witnessed in Siemens Industrial Copilot, which can decipher machine error codes in natural language and recommend corrective measures to technicians, narrowing the average repair time by 30-40%.
Quality Control: Defect Detection and Computer Vision
Quality control systems anchored in computer vision promise a huge leap in manufacturing consistency and precision. These frameworks encompass machine learning algorithms and sophisticated image processing techniques for defect, deviation, and anomaly detection, with accuracy levels exceeding 90%. Deep learning approaches, such as ResNet algorithms, promise optimal performance in quality prediction, along with precisely tuned hyperparameters. Other benefits of computer vision include dimensional inspection, surface quality assessment, and real-time defect detection.
Supply Chain Optimization: Cognitively Aware Logistics Networks
AI-based supply chain optimizations open up doors to dynamic adaptation of real-time market scenarios, geopolitical shifts, and weather patterns. For perishable industries, such as food & beverage, it means inventory cost reduction by 20-30% while enhancing on-time delivery performance through rational demand estimation and logistics optimization.
Similarly, the federated learning approach empowers manufacturers to engage in cross-vertical collaborations without sharing sensitive operational data, leading the way for collective intelligence while upholding data privacy and security protocols. Adoption of this approach addresses the most critical challenges to data confidentiality and IP protection, which is of utmost importance.
AI Agents: Rising Workforce in Manufacturing
- Virtual AI Agents: A novel category of manufacturing intelligence that promises natural language communication with the most complicated manufacturing systems. These agents are capable of interpreting operational data, identifying problems, and recommending solutions in formats ideal for human understanding. A real-life example can be witnessed in Siemens’ Mindsphere platform, a cluster of cloud-based AI operating systems that connect digital intelligence with physical manufacturing assets.
- Embodied AI Agents: They are breeding autonomous systems by combining physical robotics with AI. These are smart systems capable of carrying out complex, manipulative, and interactive tasks. Imitation learning, vision-language-action models, and reinforcement learning are some of the basic systems used by them. In 2023, BMW deployed 294 industrial robots in its Neutraubling facility. These robots can perform up to 4700 welding tasks per vehicle unit with 238 welding guns placed on robotic arms.
- Multi-agent Systems: These are collaborative intelligence networks that can coordinate planning, execution, and monitoring functions to formulate collaborative workflows, ensuring seamless interaction between physical and digital systems. They are enablers of autonomous production ecosystems where machines can self-optimize, self-diagnose, and collaborate without human intervention. Tesla’s AI-powered factory automation is a fine example of this approach.
Laying Foundations for the Human-Centric Industry 5.0
Beyond AI replacing mundane, risky human jobs, the rising integration of AI in manufacturing ecosystems represents an evolutionary phase where AI is augmenting capabilities instead of replacing them. This paradigm-altering conclusion stems from the fact that 71% of manufacturing tasks are categorized as dangerous, dirty, or dull, and more than 80% of workers report injuries. The human-centric element of Industry 5.0 will be based on three fundamentals: sustainability, resilience, and human-centricity.
Cognitive Simulation and Digital Twins
Digital twins integrate IoT, AI, and data analytics to produce self-learning production ecosystems that evolve constantly to achieve higher levels of efficiency and productivity. For example, NVIDIA’s Omniverse platform offers large-scale digital twin implementations, promising data-center-scale computing systems to drive industrial digital twins. The platform combines complex manufacturing environment simulations with precise time synchronization across virtual and physical worlds, enabling the owners to optimize operations and train autonomous systems prior to physical deployment. Apart from this, digital twins powered by AI capabilities are also empowering manufacturers with predictive scenario modeling, real-time performance optimization, autonomous decision-making, failure prediction, and prevention.
Sustainability and Circular Manufacturing
Sustainable manufacturing practices facilitated by AI are a critical spoke of the wheel of the cognitive industrial revolution. AI integration can optimize energy consumption as well as resource utilization, leading to closed-loop recycling and waste recycling strategies, reducing carbon footprints by 25-40%. Similarly, AI platforms for circular manufacturing are integrating sustainability protocols across product lifecycles. For instance, the Circular TwAIn project has been a fine example of how AI can open doors to end-to-end sustainability with cognitive digital twins that can optimize circular value chains.
Implementation Challenges and Strategic Recommendations
- Data Quality & Accessibility: One of the primary barriers has been a hurdle for approximately 65% of manufacturers in the USA. Poorly formatted and unstructured data has been reported by more than 62% of manufacturers as an obstacle to this application. This situation can be resolved with comprehensive Industrial DataOps platforms that can unify varied data sources across information technology and operational technology ecosystems.
- Cybersecurity Considerations: These, too, have been a critical barrier as AI systems integrate with operational frameworks. Manufacturers must implement AI-powered cybersecurity models to detect anomalies in real time without hampering operational continuity.
- Workforce Upgrade: Human capital development still lags behind, as most workers are apprehensive about AI-related work opportunities. It might be a good time for companies to alter their management strategies and include gamified training programs to align workforce skills with AI literacy requirements.
- Regulatory Complexities: AI governance frameworks need to be transparent, ethically sound, and compliant with regulatory systems. Thus, there is an urgent need for policy frameworks that can support AI growth while streamlining innovation with compliance requirements. Explainable AI, therefore, gains a central role in this context for its ability to enable transparent decision-making and clear rationales for AI-based operations.
The Bottomline
The cognitive industrial revolution is far beyond technological advancement; it is paving the path for the swift adoption of Industry 4.0 while developing a perspective on Industry 5.0. It also highlights the need for an imminent shift to the next industrial revolution, for the present version lacks a human-centric, intelligent approach.
The convergence of cognitive AI, human creativity, and physical robotics possesses untapped opportunities for achieving operational excellence while incorporating human well-being and sustainability. While meeting its demands for better approaches, capabilities, and human-machine collaboration, it will open the path to a new realm of manufacturing that builds the world in alignment with human and environmental exigencies.
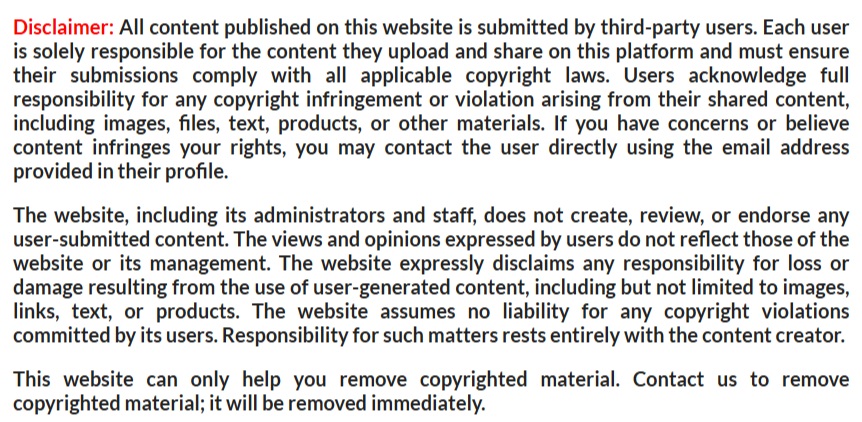