The surge in connected vehicles, electric powertrains, and smart mobility platforms is significantly impacting the Conductive Inks Market, especially in the automotive electronics domain. As vehicle architecture becomes increasingly digitized, demand for high-performance printed circuitry is growing, and conductive inks are playing a pivotal role in enabling these innovations.
Expanding Role of Printed Electronics in Vehicles
Automotive electronics are evolving beyond traditional components like engine control units and infotainment displays. Today’s vehicles incorporate printed sensors, lighting systems, heating elements, antennas, and flexible touch interfaces across dashboards, mirrors, and seats. Conductive inks, being lightweight, flexible, and cost-efficient, offer an ideal solution to meet these applications' functional and design needs.
Flexible circuits printed with silver or copper inks are replacing conventional wire harnesses, reducing vehicle weight and complexity. As electrification and automation accelerate, printed solutions allow automakers to integrate electronic functionalities seamlessly into plastic, glass, and textile surfaces—an engineering feat made possible by conductive ink technologies.
Demand Patterns Across Ink Types
Silver-based inks dominate the automotive electronics space due to their superior conductivity and reliability, particularly in safety-critical systems such as ADAS modules, battery management systems, and smart lighting. These inks are used in defogging heaters, capacitive touch panels, and printed pressure sensors for tire monitoring.
Meanwhile, copper inks are gaining traction in applications where cost efficiency and bulk deployment are essential, such as in energy storage units, printed busbars, and high-volume circuit assemblies. Innovations in oxidation-resistant copper formulations are gradually expanding their usability in long-life automotive electronics.
Graphene-based inks are still emerging but show promise in niche segments like printed heating films and transparent electronics. Their flexibility and mechanical resilience make them attractive for curved surfaces, foldable displays, and components exposed to frequent motion.
Integration into Electric Vehicles and ADAS
Electric vehicles (EVs) present a high-growth avenue for conductive inks, particularly in battery systems, power electronics, and control modules. Printed electronics allow for compact, lightweight, and scalable circuit integration—key to improving EV efficiency, reducing cost, and increasing driving range.
ADAS (Advanced Driver Assistance Systems) also rely heavily on embedded sensors, cameras, and radar modules that require precision electronics. Conductive inks enable these functionalities to be integrated into non-traditional areas like bumpers, side mirrors, and windshields, enhancing vehicle aesthetics and aerodynamics.
The integration of conductive ink-based electronics in heads-up displays, e-mirrors, and capacitive switches enhances driver interaction while reducing mechanical components. This is critical in autonomous vehicle platforms, where safety, responsiveness, and fail-safe electronics are paramount.
Production Benefits and Design Freedom
One of the key reasons automotive manufacturers are turning to conductive inks is the design freedom they allow. Printed electronics can be directly applied to flexible and curved surfaces, enabling new form factors and reduced part counts. Unlike traditional rigid PCBs, conductive inks can conform to three-dimensional surfaces inside the vehicle cabin, allowing electronics to become more invisible and ergonomic.
This advantage is particularly important for integrating ambient lighting, touch-sensitive panels, and control switches into trim panels and dashboards. In addition, printed heating elements using conductive inks offer more efficient and uniform heating for mirrors, seats, and steering wheels.
The cost benefits are also notable. While initial investment in screen or inkjet printing lines may be significant, the ability to mass-produce flexible circuits with fewer materials and simplified assembly reduces long-term production costs.
Regional Demand Dynamics
Asia-Pacific leads the global automotive electronics market, with countries like China, Japan, and South Korea investing heavily in smart vehicle infrastructure. These markets are seeing widespread use of conductive inks in both domestic and exported vehicles, driven by dense OEM ecosystems and policy support for EV adoption.
Europe, known for its strong automotive innovation hubs in Germany and Scandinavia, is investing in printed electronics to improve EV battery packs and enable vehicle-to-infrastructure connectivity. EU regulations on sustainability and electronic waste reduction further incentivize automakers to adopt recyclable and non-toxic conductive ink formulations.
North America, home to legacy automotive giants and emerging EV startups, is integrating conductive inks primarily in infotainment, autonomous driving systems, and premium interiors. U.S. automakers are also collaborating with material science firms to create custom ink solutions optimized for extreme environmental performance and long lifecycle durability.
Innovation and Collaboration in the Supply Chain
As automotive requirements become more specialized, collaboration between ink manufacturers, OEMs, and electronics integrators is intensifying. Companies like Henkel, DuPont, and Heraeus are working closely with automotive tier-1 suppliers to develop customized ink formulations tailored for temperature resistance, vibration tolerance, and environmental stability.
Startups and university spin-offs are pushing innovation in graphene inks and hybrid formulations, aiming to bring lab-scale discoveries into commercial vehicle platforms. In many cases, these partnerships accelerate technology transfer and reduce development timelines.
Supply chain integration is also key. With semiconductor shortages and logistics challenges in the post-pandemic landscape, having a reliable, scalable, and geographically diversified ink supply chain is becoming critical to automakers' electronics strategies.
Outlook: Printed Electronics to Become Standard
The role of conductive inks in automotive electronics will only grow as vehicles become more intelligent, connected, and electrified. Printed electronics are expected to become standard in cabin electronics, exterior systems, battery management, and even chassis-integrated sensors.
Long-term, innovations in 3D printing, AI-driven ink design, and sustainable materials will reshape how automotive electronics are designed and manufactured. The ability of conductive inks to reduce wiring complexity, lower production costs, and enhance functionality aligns perfectly with the future of mobility.
#conductiveinks #automotiveelectronics #electronicvehicles #printedelectronics #grapheneink #copperink #silverink #adas #connectedcars #smartvehicles #flexcircuits #vehicletechnology #mobilityinnovation
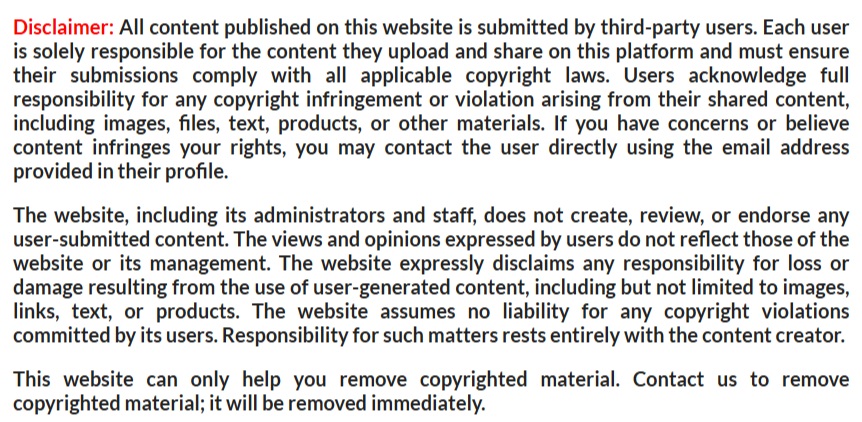