views
Composite Manufacturing Meets Aerospace Product Development: Innovative Materials in Flight
Introduction
The future of air travel is being reshaped by a powerful alliance between composite manufacturing and aerospace product development. As aircraft demand greater fuel efficiency, strength, and safety, traditional materials like aluminum and steel are no longer enough. Engineers and designers now turn to composites—engineered materials made by combining two or more distinct substances—to deliver next-generation aircraft. These innovative materials offer a blend of strength, flexibility, and lightness that is transforming how we design, build, and fly planes today.
What Are Composite Materials?
Composite materials are made by combining a matrix (such as plastic or resin) with a reinforcing material (like carbon fiber or glass fiber). This combination forms a material that is stronger, lighter, and often more durable than either component alone. Some common examples include:
-
Carbon fiber reinforced polymer (CFRP): Lightweight and extremely strong, ideal for aircraft wings and fuselages.
-
Glass fiber reinforced polymer (GFRP): Less expensive and used in less load-sensitive parts.
-
Aramid fiber (Kevlar): Known for its toughness and often used in military and aerospace applications.
These materials can be tailored to meet specific needs, offering flexibility in design without compromising strength or performance.
The Role of Composite Manufacturing in Aerospace
Composite manufacturing plays a crucial role in the aviation sector by enabling the production of lighter aircraft. Lighter aircraft use less fuel, produce fewer emissions, and are more cost-effective to operate. In aerospace product development, this weight advantage is a major benefit that influences nearly every design decision.
Key Advantages of Composites in Aerospace:
-
Weight Reduction – Composites weigh significantly less than metals, helping improve fuel efficiency.
-
High Strength-to-Weight Ratio – Despite being lightweight, composites offer excellent strength.
-
Corrosion Resistance – Unlike metals, composites do not rust or corrode, which improves durability.
-
Design Flexibility – Composite materials can be molded into complex shapes that are hard to achieve with traditional metals.
Applications in Aircraft Design
Today, composite manufacturing is widely used in the production of commercial, military, and even private aircraft. Modern planes like the Boeing 787 Dreamliner and Airbus A350 have over 50% of their structure made from composite materials.
Common Applications Include:
-
Fuselage sections: Lighter materials help reduce total aircraft mass.
-
Wings and tail fins: Composites provide the necessary aerodynamic strength.
-
Interior components: Lightweight panels and seating structures contribute to overall weight savings.
-
Engine components: Heat-resistant composites are now used in turbine parts.
By integrating these materials into various components, manufacturers can build aircraft that are safer, more fuel-efficient, and cheaper to maintain.
Innovative Trends in Composite Manufacturing
With ongoing research, newer and smarter composite materials are being developed. These innovations include:
-
Thermoplastic composites – Easier to recycle and faster to manufacture.
-
Nano-reinforced composites – Improved strength and performance at a microscopic level.
-
Self-healing composites – Materials that can repair small cracks and damages automatically.
-
Automated fiber placement (AFP) – Robotics and automation are speeding up composite layup processes while reducing errors.
Such advancements are driving the aerospace industry to embrace even more sustainable and efficient manufacturing processes.
Challenges and Future Outlook
Despite their advantages, composites also present challenges. Manufacturing them requires specialized equipment and skilled labor. Quality control can be more complex, and repair techniques differ from those used with metals. Furthermore, recycling composites remains a significant hurdle for the industry.
However, aerospace product development continues to push the boundaries of material science. As technologies improve, the cost and complexity of using composites will decrease. Research is underway to create recyclable composites and faster manufacturing methods. These efforts will make composites even more dominant in the skies.
Conclusion
Composite manufacturing has become a cornerstone of modern aerospace product development. By replacing heavier metals with lighter, stronger, and more durable materials, manufacturers are building aircraft that are more efficient, environmentally friendly, and capable of meeting the high demands of today’s aviation industry.
As innovative materials continue to evolve, the bond between composite manufacturing and aerospace product development will only grow stronger, taking flight into a future where performance meets sustainability at every altitude.
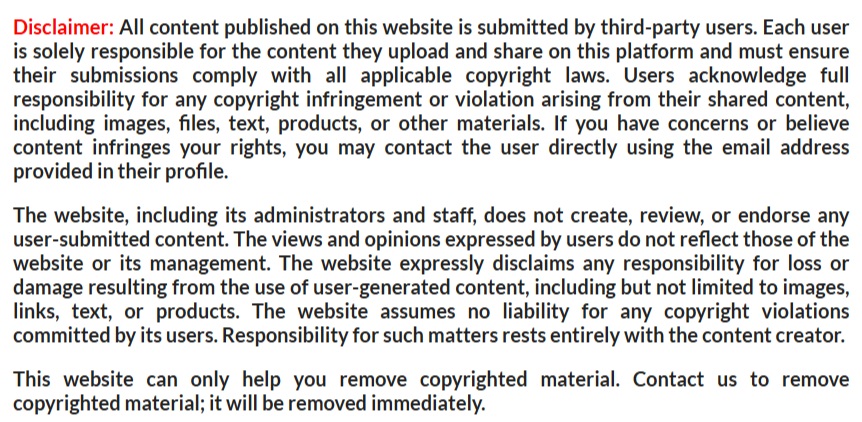