views
Fundamentals of Quality Management
A strong quality management framework is generally built on four foundational components:
- Quality Planning – Establishing processes, criteria, and goals to align with customer requirements.
- Quality Assurance (QA) – Implementing systematic practices to ensure processes are structured to prevent errors.
- Quality Control (QC) – Monitoring outputs to detect and resolve issues prior to delivery.
- Quality Improvement – Ongoing analysis of performance metrics and process refinement to drive enhanced results.
The Seven Quality Management Principles
- Customer Focus – Tailoring products and services to meet customer needs and expectations.
- Leadership – Promoting a unified vision and quality-oriented culture through organizational leadership.
- Engagement of People – Enabling employees across all levels to actively participate in quality efforts.
- Process Approach – Coordinating activities and resources through interconnected systems to optimize efficiency.
- Improvement – Instilling a culture of ongoing improvement throughout the organization.
- Evidence-Based Decision Making – Basing decisions on factual information and analytical insights.
- Relationship Management – Developing and maintaining strategic partnerships with suppliers and stakeholders to ensure sustained success.
The Plan‑Do‑Check‑Act (PDCA) Cycle
Central to many quality systems is the PDCA cycle, a four‑step iterative model for achieving continuous improvement:
- Plan – Identify objectives and processes required to deliver results.
- Do – Implement the plan on a small scale to test its effectiveness.
- Check – Monitor and measure the results against expected outcomes.
- Act – Standardize successful improvements or revisit the cycle to refine further
Quality Management Systems (QMS) and ISO 9001
A Quality Management System (QMS) is a systematic framework of organizational processes designed to fulfill customer needs and improve satisfaction. It integrates policies, documented procedures, resources, and information required to establish, execute, and sustain quality objectives.
ISO 9001, the most globally recognized and extensively implemented QMS standard, defines requirements that empower organizations to ensure reliable delivery of products and services aligned with customer expectations and regulatory obligations.
Quality Assurance vs. Quality Control
Though often used interchangeably, QA and QC serve distinct roles within quality management:
- Quality Assurance (QA) is process‑oriented and proactive, focusing on preventing defects through well‑defined standards and guidelines.
- Quality Control (QC) is product‑oriented and reactive, emphasizing inspection and testing to identify and correct defects in outputs.
Total Quality Management (TQM) and Continuous Improvement
Total Quality Management (TQM) represents an organization‑wide commitment to continuous improvement and customer focus. By integrating quality principles into every process and engaging all employees, TQM fosters a culture where excellence becomes a shared responsibility. Originating from quality pioneers such as Deming and Juran, TQM remains a cornerstone of long‑term organizational success.
Tools and Techniques for Quality Excellence
Organizations employ diverse methodologies and tools to enhance quality initiatives, including:
• Six Sigma – A data-driven methodology to reduce process variations and defects.
• Lean Management – Focuses on eliminating waste and streamlining workflows to boost efficiency.
• Statistical Process Control (SPC) – Monitors and regulates processes using statistical analysis.
• Fishbone (Ishikawa) Diagrams & Pareto Analysis – Tools to pinpoint root causes and prioritize issues for resolution.
When integrated with the PDCA (Plan-Do-Check-Act) cycle, these approaches collectively create a robust framework for maintaining high-quality outcomes.
Implementing a Quality Management Strategy
Successful deployment of a QMS involves:
- Gap Analysis – Assess current processes against desired quality standards.
- Process Definition – Document workflows, responsibilities, and performance metrics.
- Training & Engagement – Equip teams with the knowledge and tools to uphold quality standards.
- Measurement & Monitoring – Use KPIs and audits to track quality performance.
- Management Review – Conduct regular executive reviews to drive strategic improvements.
Benefits of Effective Quality Management
Investing in quality management delivers tangible benefits:
- Enhanced Customer Satisfaction through reliable, high‑quality products and services.
- Regulatory Compliance by meeting industry and statutory requirements.
- Operational Efficiency via reduced rework, waste, and downtime.
- Competitive Advantage gained from a reputation for excellence.
- Continuous Improvement embedded into company culture, driving sustainable growth
Choosing the Right Quality Management Software
Modern quality challenges demand digital solutions. ToolkitX’s Quality Management platform centralizes document control, audit management, CAPA workflows, and analytics—all within an intuitive interface. By automating routine tasks and providing real‑time insights, ToolkitX empowers teams to focus on strategic quality initiatives rather than administrative overhead.
Ready to elevate your quality processes?
Discover how ToolkitX’s Quality Management solution can streamline your QMS, boost compliance, and drive continuous improvement.
👉 Get started with ToolkitX Quality Management https://toolkitx.com/campaign/quality-management/
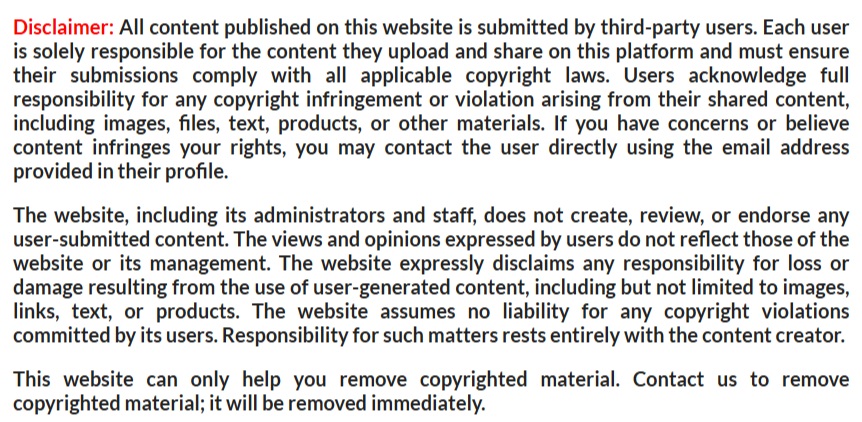