Precision Laser Resistor Trimming Machines and Their Advantages in Thick Film Resistor Manufacturing
views
In the modern electronics manufacturing industry, resistors play a fundamental role in ensuring circuit stability and performance. To meet the growing demand for accuracy and reliability, laser resistor trimming machines and laser trimming equipment have become essential tools, especially in the production of thick film resistors. These advanced technologies provide precise control over resistor values, improving product quality and manufacturing efficiency.
What Is a Laser Resistor Trimming Machine?
A laser resistor trimming machine uses a focused laser beam to precisely adjust the resistance value of a resistor after it has been manufactured. Unlike traditional mechanical or chemical trimming methods, laser trimming offers a non-contact, highly accurate, and efficient way to fine-tune resistor values. This ensures the components meet exact specifications required for high-performance electronic devices.
How Does Laser Trimming Equipment Work?
Laser trimming equipment operates by selectively ablating (removing) part of the resistive film on the resistor using a controlled laser beam. By changing the geometry of the resistive path, the resistance value can be adjusted with high precision. The non-contact nature of laser trimming prevents mechanical damage and contamination, common issues in other trimming methods.
Advantages of Laser Trimming in Thick Film Resistor Processes
Thick film resistors are typically made by screen-printing a resistive paste onto a ceramic substrate and then firing it at high temperatures. The thick film process offers cost-effectiveness and design flexibility but requires precise trimming to meet resistance tolerance requirements. Laser trimming enhances this process by:
-
High Precision: Enables resistance adjustments within tight tolerance levels, often less than 1%.
-
Improved Stability: Non-contact laser trimming minimizes mechanical stress, improving long-term stability.
-
Efficiency: Automated laser trimming equipment increases throughput and reduces labor costs.
-
Flexibility: Suitable for a wide range of resistor sizes and designs.
Key Resistor Advantages Enabled by Laser Trimming
Using laser trimming in resistor production brings several critical benefits:
-
Enhanced Accuracy: Laser trimming machines can fine-tune resistors to exact values, essential for sensitive circuits.
-
Reduced Defects: The precise control reduces rejects and rework, improving yield.
-
Compact Designs: Enables smaller resistor footprints by optimizing resistance patterns.
-
Better Performance: Improves thermal stability and reduces noise in resistors.
Conclusion
The integration of laser resistor trimming machines and laser trimming equipment in the thick film process significantly advances resistor manufacturing quality and efficiency. These technologies ensure resistors meet strict electrical specifications, supporting the development of reliable and high-performance electronic products across various industries.
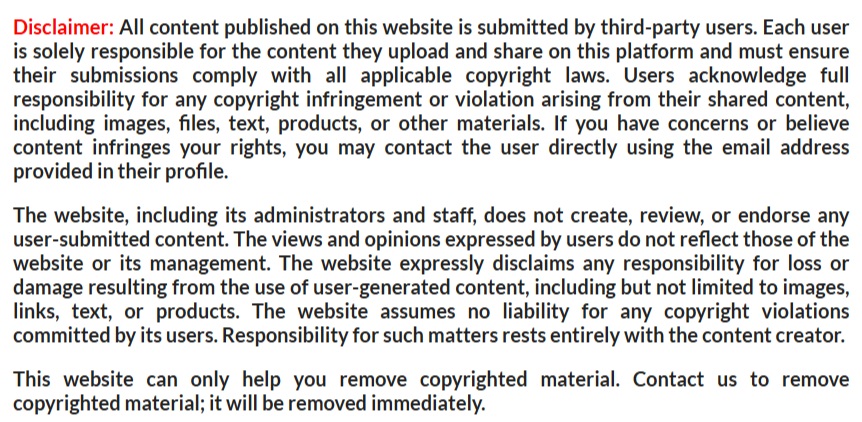