views
Future of 3D Printing Speed: What’s Fastest in 2025
Innovation fuels the medical device industry—and when lives are on the line, speed is everything. By 2025, 3D printing has become the go-to solution for prototyping, empowering manufacturers to accelerate development, compress design cycles, and produce precise, test-ready models faster than ever.
The shift is undeniable: medical prototypes now account for over 40% of all industrial 3D printing activity. In a space where every moment counts, slow iteration is no longer an option. With rapid advancements in robotics, sensors, and miniaturized components, fast, dependable prototyping is critical to transforming breakthrough ideas into life-saving medical technologies—without delay.
Why Fast Prototypes Matter
Traditionally, developing medical devices meant waiting months for the first CNC-cut test unit to come off the line. That timeline collapsed during the COVID-19 pandemic. Ventilator parts, swab guides, and face shields were designed, printed, and on the road in days instead of months.
Rapid prototyping services have become essential for medical device companies wanting to lead the field. Shorter design cycles help teams test more, gather user feedback sooner, and move more quickly through regulatory steps. When every hour counts for a life-saving product, picking the right 3D printing method matters a lot.
5 Fastest 3D Printing Technologies for Medical Prototypes in 2025
1. Stereolithography (SLA) – Still the Fastest
SLA remains the top choice for medical prototyping in 2025. The newest printers can make smooth, detailed parts in just 2 to 4 hours, depending on the design and size.
Key Advantages: Modern SLA systems can print at nearly 50 mm/hour and create surfaces so smooth that many parts do not need sanding or polishing. Biocompatible resins are widely available, and the printers maintain accuracy within ±0.1 mm, vital for devices that must fit together and work perfectly.
Best Applications: SLA is ideal for surgical guides, dental models, hearing aid shells, and detailed anatomical models used in surgical planning.
2. Carbon DLS (Digital Light Synthesis) – Super Fast, Super Strong
Carbon DLS prototyping revolutionizes additive manufacturing. By using continuous liquid interface production (CLIP), it trades the slow layer-by-layer method for a continuous flow, letting parts form 25 to 100 times faster than before.
Since its launch, Carbon DLS has become the standard for the medical device sector. Giants like Johnson & Johnson and Riddell trust it for critical components. Fast production counts, but strength and reliability do too, and Carbon DLS excels at both. That makes it ideal for medical prototypes that must move straight from the printer to the clinic.
Performance Numbers: Carbon DLS speeds can top 100 mm/hour while still meeting production-grade material specs. Parts emerge with smooth surfaces and zero layer lines. Plus, you can choose FDA-approved resins, so you’re ready from the start.
Best Application Areas: Carbon DLS shines in functional prosthetics, orthopedic implants, surgical tools, and wearable medical devices.
3. Multi Jet Fusion (MJF) – High-Speed Batch Production
HP’s Multi Jet Fusion is built to boost prototype output fast.
It prints entire batches of medical devices at once by using inkjet heads to spray fusing and detailing agents onto a powder bed. This fast process produces strong and reliable parts without compromise.
Designed for production, MJF also fits the fast design loops that medical device R&D squads depend on. With the same printer, you can move from a handful of prototypes to hundreds of final parts in one go. The process produces tight tolerances and excellent mechanical strength, meeting the needs of devices that must perform under real conditions.
Key Benefits: HP’s Multi Jet Fusion technology combines speed and scale without the need for support structures. Parts have uniform mechanical properties in every direction, making them ideal for quick iterations and larger production runs without raising costs.
Ideal Applications: Enclosures for medical devices, complex internal mechanisms, and high-volume batches of functional prototypes for testing.
4. Selective Laser Sintering (SLS) - Fast and Flexible
SLS is still the top choice for early-stage medical device prototypes. It offers a large range of biocompatible powders and makes it easy to build complex geometries without the hassle of support materials. Latest laser upgrades and better powder-handling methods have pushed the build speed even higher.
Key Benefits: SLS can create detailed internal geometries and hollow channels while running without support. The latest advancements speed up layer times and powder recovery without sacrificing quality, keeping SLS a proven choice for medical applications.
Best Uses: Brokering complex assemblies, designing moving parts, and making devices that combine several material properties.
5. PolyJet Technology - Multi-Material Potential
PolyJet 3D printing excels when a prototype must show several materials, hardness levels, or colors in one part. The printer can jet rigid and flexible resins simultaneously, producing prototypes that look and feel just like the final device.
Strengths: The ability to mix materials in a single build cycle leads to smooth surfaces and tight tolerances. With a wide library of resins, PolyJet is ideal for prototypes that require realistic function and finish right off the printer.
Applications: This is an excellent fit for devices that need soft outer skins and rigid inner frames, for components that flex and hold their shape, and for medical touch controls that respond to gentle swipes.
Design for Additive Manufacturing (DfAM) in Medical Applications
Come 2025, Design for Additive Manufacturing (DfAM) is even more intuitive. AI-driven design platforms coach engineers to refine prototypes so they print quicker and shine brighter. Learning DfAM rules is the first step to unlocking the full power of next-generation printers.
Core DfAM Rules for Medical Devices
Geometric Optimization: 3D printing opens doors for shapes that dies and molds can’t achieve. We can craft featherweight lattice scaffolds, smooth-curved cooling ducts in surgical handpieces, and winding fluid channels all in one build.
Material Considerations: Each printing process offers a unique set of material behaviors. DfAM steers teams to the right resin, metal, or polymer and lets them design features that leverage that material’s greatest strengths, while still meeting medical standards and ensuring biocompatibility.
Support Structure Minimization: New DfAM strategies enable engineers to cut down or completely eliminate scaffolding. That’s transformative for devices with delicate inner cavities or thin walls that risk damage when supports come off.
Cost of Rapid 3D Printing for Medical Prototypes
Understanding the cost structure of the latest 3D printing methods helps med-device companies select the best path for prototypes. In 2025, here’s how the numbers now line up.
SLA Printing Costs: Resin now runs between $150 and $300 per kilogram. When you add overhead and print time, most prototypes land between $25 and $150 each. Setup still takes about 30 to 60 minutes.
Carbon DLS Prototyping Costs: Resin for this approach is pricier, at $200 to $400 per kilogram. Still, finished parts usually run $50 to $200 each. The lower cost comes from a faster finishing workflow that trims labor time.
MJF Printing Costs: Nylon powder sits at $80 to $150 per kilogram. This method pays off for medium-to-large batches, bringing per-part costs down when you run several prototypes at once.
Don’t forget TCO. Include post-processing, inspection, and how fast you can pivot a design. Technologies that print faster can outweigh higher material costs by shrinking the product timeline and getting devices to market sooner.
How to Get Started with Medical Device Rapid Prototyping
Starting in medical device prototyping requires smart planning and the right team. Follow these steps, and you’ll be on the right path:
1. Define Requirements
Begin by writing down the key needs for your prototype:
-
The device’s intended function and the performance benchmarks it must hit
-
Biocompatibility and regulatory guidelines must be satisfied
-
A clear timeline and budget that you can stick to
-
Testing and validation phases, including when each will happen
2. Technology Selection
Choose the best 3D printing method based on these factors:
-
The complexity of the part geometry
-
The material properties and biocompatibility you demand
-
The number of prototypes you want and how quickly you want to change them
-
The surface finish and size accuracy are non-negotiable
3. Partner Selection
Pick a rapid prototyping firm by checking:
-
Their available technologies and machines
-
Their experience with medical devices and necessary certifications
-
Their quality management systems and how they align with regulatory needs
-
Their lead times and whether they can meet your volume
Top Providers of Medical Device Rapid Prototyping in 2025
In 2025, these firms are leading the way in speed and reliability for medical device prototypes:
-
MediPrint Prototypes: Known for biocompatible polymers and quick iteration cycles.
-
ExactMed Solutions: Offers a full suite of certifications and a wide material library.
-
3DMed Labs: Specializes in complex geometries and precision finishing.
-
RapidMed Partners: Strong in low-volume production and regulatory filing support.
-
ProtoMed Dynamics: Combines metal and polymer printing for hybrid prototypes.
Choose a provider that lines up with your project needs, and you’ll have the support to turn your idea into a working prototype.
As of 2025, the medical device prototyping market features several leading companies known for customised support:
APRIOS continues to set the standard by combining the latest 3D printing technology with years of medical device know-how. They offer complete service, from refining the initial design and picking the best materials to steering you through the regulatory maze.
Carbon remains the leader in DLS printing, providing advanced printers and direct support for prototype development. Their deep materials expertise and ability to transition to full-scale production make them the partner of choice for parts that must match the final product’s performance.
Stratasys delivers a comprehensive suite of PolyJet and FDM printers made specifically for the medical field. Their FDA-cleared resins and extensive library of biocompatibility documents streamline the compliance process from the start.
EOS supports the market with durable SLS and SLM systems that use certified medical-grade powders, making them the top choice for metal implants and customized surgical tools.
Why APRIOS Stands Out for Medical Device Prototyping
APRIOS is the trusted source for medical device companies that require quick, accurate prototypes in a single pass. Their experts understand every phase of the product lifecycle, from the first design sketch to the final FDA documentation checklist.
Why Choose APRIOS? APRIOS merges SLA, SLS, MJF, and Carbon DLS into one smooth process, supported by a crew fluent in engineering and regulatory speak. Their ISO 13485 quality system keeps the pace fast, runs on-time shipping promises, and carves out design changes using DfAM smarts.
Whether you’re a fresh startup designing your first implant or a major OEM launching the latest diagnostic system, APRIOS is the trusted partner that turns bench ideas into clinical-ready prototypes.
Future Trends in Medical Device 3D Printing
By 2025, several exciting trends will change how we prototype medical devices:
AI-Driven Design Tweaks: Smart machine-learning programs are now adjusting 3D-printing designs on the fly, reducing the number of trial-and-error loops and making it much more likely that the first print will work perfectly.
Green Materials: Biopolymer filaments and photopolymers that come from renewable resources, along with fully recyclable powders, are fast becoming the standard. These help medical companies meet sustainability targets while still delivering safe, high-performance components.
Hybrid Manufacturing: Combining 3D printing with injection molding and CNC machining allows engineers to create prototypes that look, feel, and perform like the finished device. These parts are still easy to change, making iterative testing quicker.
Real-Time Quality Checks: New sensors, cameras, and AI algorithms monitor every single layer as it prints, spotting defects the moment they happen. This means less wasted material and fewer costly reprints.
Conclusion
In 2025, medical device prototyping stands ready for dramatic leaps. Breakthrough platforms like Carbon DLS, the latest SLA printers, and Multi Jet Fusion have pushed the limits of speed, precision, and functional performance, empowering innovators to turn ideas into on-the-bench prototypes faster than ever.
Success now hinges on more than the fastest machine. Device developers must balance materials science, clever geometry, regulatory insight, and scalable production strategy. By collaborating with partners like APRIOS and embedding Design for Additive Manufacturing from day one, teams can compress the schedule while protecting quality and compliance.
As the technology landscape keeps evolving, early adopters of these advanced printers and proven workflows will be the first to place life-saving devices into the hands of clinicians and patients. The future of healthcare depends on our ability to prototype, test, and refine with unprecedented speed, and the 3D printing solutions of 2025 have already brought that future into the present.
FAQs
1. What is the fastest 3D printing method for medical prototypes in 2025?
The fastest method is Carbon DLS (Digital Light Synthesis), which uses a continuous printing process to produce strong, high-quality parts up to 100 mm/hour. It's ideal for functional, clinic-ready medical prototypes.
2. Why is SLA still popular for medical device prototyping?
Stereolithography (SLA) remains a favorite due to its high precision, smooth surface finish, and availability of biocompatible resins. It's especially useful for surgical guides, dental models, and anatomical replicas.
3. How do I choose the right 3D printing method for my medical prototype?
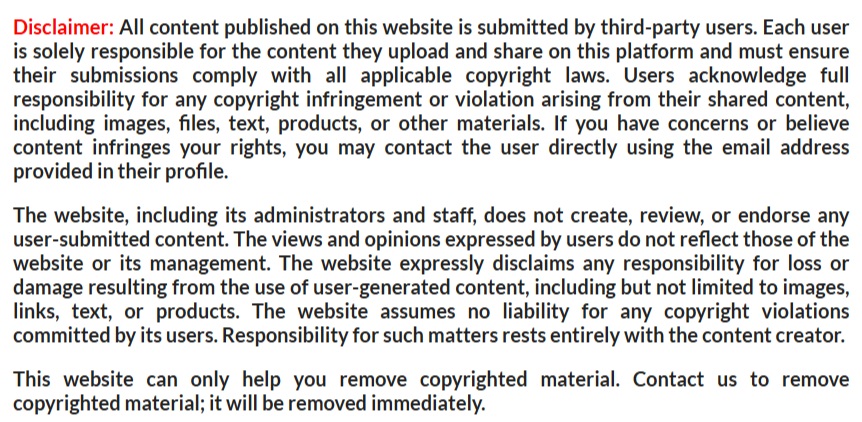