views
Exploring the PUF Panel Manufacturing Process: From Raw Material to Final Product
In the evolving world of construction, energy efficiency, speed, and sustainability are now essential. One innovation that’s making waves in both commercial and residential construction is the PUF panel. Known for their insulation properties, durability, and ease of installation, PUF (Polyurethane Foam) sandwich panels are now widely used across India in homes, factories, cold storages, offices, and more.
But have you ever wondered how these panels are made? In this article, we’ll walk you through the PUF panel manufacturing process, from raw material selection to the final product ready for installation. We’ll also explore how companies like BNAL Prefabs, a leading PUF panel manufacturer in India, are setting new benchmarks in quality and innovation.
What is a PUF Panel?
A PUF panel (Polyurethane Foam panel) is a composite construction material made from two outer layers of metal sheets (usually pre-painted galvanized iron or aluminum) with a rigid polyurethane foam core in the center. These panels are primarily used for wall cladding, roofing, cold rooms, clean rooms, and prefabricated structures in India.
PUF panels are praised for:
-
Thermal insulation
-
Lightweight structure
-
Fire resistance
-
Quick installation
-
Energy efficiency
Step-by-Step: The PUF Panel Manufacturing Process
1. Raw Material Selection
The manufacturing journey begins with the careful selection of raw materials:
-
Outer Sheets: These are typically galvanized steel (GI) or aluminum sheets, often pre-coated for rust and corrosion resistance.
-
Polyol and Isocyanate: The two main chemicals that form polyurethane foam.
-
Adhesives & Coatings: Optional additives for bonding and protection.
Top PUF panel manufacturers in India like BNAL Prefabs ensure all materials meet industry standards and are sourced from reliable suppliers.
2. Surface Preparation and Sheet Feeding
The metal sheets are uncoiled and cleaned to remove any dust, oil, or surface impurities. The sheets then enter the continuous panel production line, a fully automated system that feeds the top and bottom metal sheets simultaneously.
The alignment must be precise to avoid defects in the final panel, especially for PUF wall panels and roof panels used in precision-driven projects like hospitals and laboratories.
3. Polyurethane Foam Injection (Foaming Process)
The core of the panel is formed by injecting a mixture of polyol and isocyanate between the two metal sheets. This reaction creates polyurethane foam (PUF), which expands quickly and bonds to the inner sides of the sheets.
This step is critical because:
-
It determines the thermal insulation efficiency
-
It impacts structural strength
-
It ensures uniform density and bonding
BNAL Prefabs, one of the top PUF sandwich panel manufacturers in India, uses high-pressure foaming machines that maintain uniform foam density (usually around 40±2 kg/m³).
4. Heating and Curing
Once the PUF mixture is injected, the panel enters a heated press or conveyor system. This allows the foam to expand and cure (harden), ensuring strong adhesion between the foam and the metal sheets.
Curing ensures:
-
Consistent insulation performance
-
Long-lasting strength
-
No delamination or sagging over time
This is where automated systems offer a major advantage—helping top PUF panel manufacturers maintain product consistency.
5. Panel Cutting and Sizing
After curing, the continuous panel is cut into customized lengths and sizes as per project requirements. Typical thicknesses range from 30mm to 150mm depending on the application (e.g., cold storages, modular homes, prefabricated offices, etc.).
BNAL Prefabs, a top PUF wall panels manufacturer in India, offers complete customization including:
-
Panel length and width
-
Thickness of foam core
-
Color and coating of metal sheets
-
Joint type (tongue & groove or cam-lock)
6. Quality Control and Testing
Every PUF panel undergoes strict quality testing before dispatch:
-
Thermal conductivity test
-
Compressive strength
-
Fire resistance
-
Dimensional accuracy
-
Adhesion test (bonding strength)
Manufacturers like BNAL Prefabs, a best PUF panel manufacturing company in Chandigarh, have ISO-certified quality checks to ensure panels meet national and international building standards.
7. Packaging and Delivery
The finished panels are carefully packed to avoid any transportation damage. Protective films, foam sheets, and wooden pallets are used to ensure safe delivery to client sites across India.
BNAL Prefabs delivers PUF panels to major cities and states including:
-
Chandigarh
-
Maharashtra
-
Gujarat
-
Kerala
-
Mumbai
-
Rajasthan
-
Himachal Pradesh
Why BNAL Prefabs is a Trusted PUF Panel Manufacturer
BNAL Prefabs is one of the few companies in India offering both PUF panel manufacturing and pre-engineered building (PEB) solutions under one roof. Here’s why they’re trusted by clients nationwide:
-
Continuous line production for seamless quality
-
Custom-built PUF panels and structures
-
Timely delivery across India
-
Experienced team and on-site installation
-
Eco-friendly and energy-efficient practices
Whether you're searching for PUF panel manufacturers in Mumbai, prefab construction in India
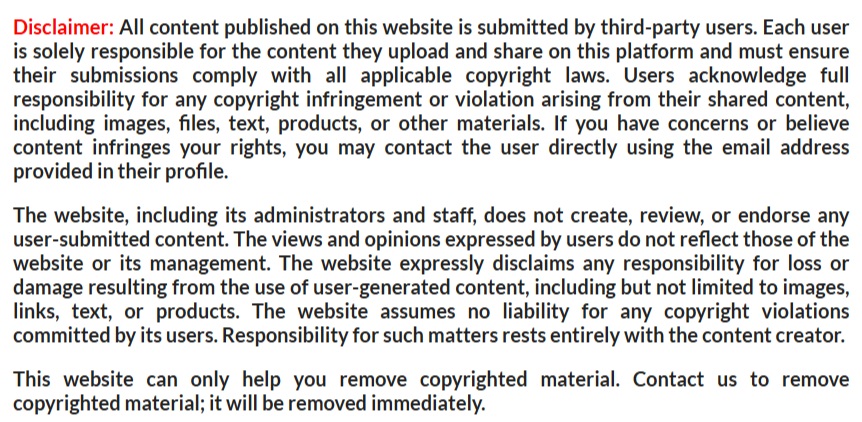