views
Leaf springs play a crucial role in vehicle suspension systems, particularly in trucks, buses, trailers, and off-road vehicles. These components endure extreme mechanical stress, repeated flexing, and constant exposure to harsh environmental conditions. Among the many challenges they face, corrosion is one of the most significant, directly affecting durability, safety, and performance.
This article provides a comprehensive overview of corrosion in leaf springs, its causes, effects, and the best strategies—both traditional and advanced—used to protect leaf springs from corrosion and extend their service life.
Understanding Corrosion in Leaf Springs
Corrosion is a chemical or electrochemical process that leads to the deterioration of metals due to reactions with their environment—primarily oxygen, moisture, and road salts.
Why Leaf Springs Are Vulnerable:
- Made predominantly of carbon steel, which is highly reactive with moisture and salts
- Constant exposure to mud, rain, snow, road salts, and chemicals
- Surface wear due to inter-leaf friction and vibration, which removes protective coatings
- Installation in low-airflow, high-debris zones (near axles, wheels, and undercarriage)
Effects of Corrosion:
- Loss of mechanical strength, increasing the risk of spring breakage
- Reduced fatigue life, as corrosion pits become crack initiation points
- Poor ride quality due to stiffness changes and irregular deformation
- Increased maintenance costs and downtime due to early replacement
Key Corrosion Protection Strategies
Protecting leaf springs from corrosion requires a combination of material selection, surface treatment, coating technology, and proper maintenance. Below are the most effective strategies used in modern manufacturing and field applications.
Material Selection and Alloying
The choice of steel greatly influences corrosion resistance and fatigue life.
Common Steel Grades:
- SAE 5160, 6150 (chromium alloys)
- EN 45, EN 47 (used in European markets)
- SUP 9, SUP 10 (Japanese equivalents)
Alloying Additives:
- Chromium (Cr): Enhances corrosion and oxidation resistance
- Molybdenum (Mo): Improves strength and pitting resistance
- Nickel (Ni): Adds toughness and better resistance to environmental attack
While higher alloy content improves corrosion resistance, it also increases cost. Manufacturers often balance performance with affordability, especially in commercial vehicle markets.
Shot Peening
Shot peening is a surface treatment that involves bombarding the spring with small spherical media to induce compressive residual stresses.
Benefits:
- Improves fatigue resistance by preventing crack propagation
- Closes microscopic surface cracks and corrosion pits
- Removes surface contaminants that accelerate rusting
Shot peening is typically applied after heat treatment and before painting or coating, serving as a foundational protection method.
Surface Coatings and Paint Systems
One of the most important lines of defense against corrosion is protective coating.
Common Types:
a) Zinc Phosphate Coating
- Applied as a base layer to enhance paint adhesion
- Provides sacrificial protection (zinc corrodes before steel)
b) Electrostatic Powder Coating
- Offers a uniform, thick, durable finish
- Resistant to chips and abrasion
- Commonly used in OEM spring production
c) Cataphoretic (E-Coating) Painting
- An immersion-based coating technique that provides full coverage, even in internal gaps
- Excellent corrosion resistance and adhesion
- Preferred in automotive and heavy-duty spring manufacturing
d) Bituminous or Rubberized Undercoating
- Applied on heavy-duty trucks or trailers
- Helps resist stone chipping and water ingress
. Interleaf Liners and Anti-Friction Pads
Interleaf corrosion is a major concern in multi-leaf springs, where leaf-to-leaf contact traps moisture and road debris.
Solutions:
- Nylon or polyurethane pads are inserted between leaves
- Reduces metal-to-metal contact
- Prevents water and salt accumulation
- Allows better articulation, reducing wear and tear
Modern parabolic springs often use single or fewer leaves, reducing this corrosion source significantly.
Hot-Dip Galvanization
In this method, springs are dipped into molten zinc to form a thick, adherent zinc layer.
Advantages:
- Long-lasting (15–25 years in moderate environments)
- Excellent protection in coastal or salty conditions
- Zinc sacrificially corrodes before steel does
Limitations:
- Adds weight
- May affect dimensional tolerances and spring stiffness
- More common in infrastructure (bridges, utility poles) than in high-performance springs
Advanced Composite Coatings
In recent years, manufacturers have begun to explore composite and ceramic-based coatings for premium corrosion resistance.
Examples:
- Epoxy-ceramic coatings
- PTFE (Teflon) infused surfaces
- Hybrid nano-coatings with graphene or carbon nanotubes
These offer ultra-high resistance to chemical attack and abrasion, though they remain expensive and are currently limited to specialty applications like aerospace or military vehicles.
Sealing and Welding Spring Ends
Corrosion often initiates at the spring eyes or bolt holes, where moisture and dirt accumulate.
Preventive Techniques:
- Proper sealing of spring eyes using bushings and O-rings
- Closed-eye designs to reduce entry points
- Welding or sealing clips and clamps to prevent debris entrapment
Attention to design details can significantly minimize crevice and pitting corrosion.
Regular Cleaning and Inspection
No coating or material can guarantee lifelong protection. Routine cleaning and maintenance are crucial, especially in salt-rich winter environments.
Maintenance Tips:
- Wash the undercarriage regularly, especially after snow or off-road trips
- Inspect for rust spots, flaking paint, and surface pitting
- Reapply touch-up coatings or anti-rust sprays seasonally
- Keep drain holes (if present) unblocked
Fleet operators often implement seasonal inspections to catch early signs of corrosion.
Design Optimization for Corrosion Resistance
Engineering design can influence how susceptible a spring is to corrosion.
Design Practices:
- Use fewer, thicker leaves (parabolic designs) to reduce inter-leaf spaces
- Rounded corners and smooth surfaces reduce stress concentrations and water pooling
- Avoid sharp bends, which are crack initiation points
- Drainage grooves in spring clamps or seats to channel out water
Such strategies reduce the likelihood of water retention and micro-corrosion.
Storage and Handling Best Practices
Even before installation, improper storage can lead to early corrosion.
Best Practices:
- Store leaf springs in dry, covered areas
- Avoid direct contact with the ground
- Use rust-preventive oils or sprays during storage
- Avoid scratching or damaging factory coatings
Springs damaged during transport or mishandled during installation may develop corrosion much faster than expected.
Real-World Industry Practices
Automotive OEMs:
- Typically use e-coating + powder coating combinations
- Conduct salt spray tests (ASTM B117) for quality validation
- Employ robotic coating systems for consistency
Commercial Fleets:
- Apply aftermarket undercoating
- Schedule biannual corrosion inspections
- Replace anti-friction liners as part of preventive maintenance
Military and Off-Road Vehicles:
- Favor galvanized or ceramic coatings
- Use sealed spring assemblies
- Include corrosion-resistance as part of military spec standards (e.g., MIL-STD-810)
Corrosion is an inevitable challenge for leaf spring , especially in demanding environments. However, through smart material selection, effective coating systems, innovative designs, and diligent maintenance, the service life of leaf springs can be significantly extended.
With increasing demands on vehicle performance and longevity—particularly in commercial and off-road sectors—investing in corrosion protection is not optional; it's essential. Whether you're a fleet operator, vehicle manufacturer, or service technician, integrating these strategies can help you reduce costs, improve reliability, and ensure safety on the road.
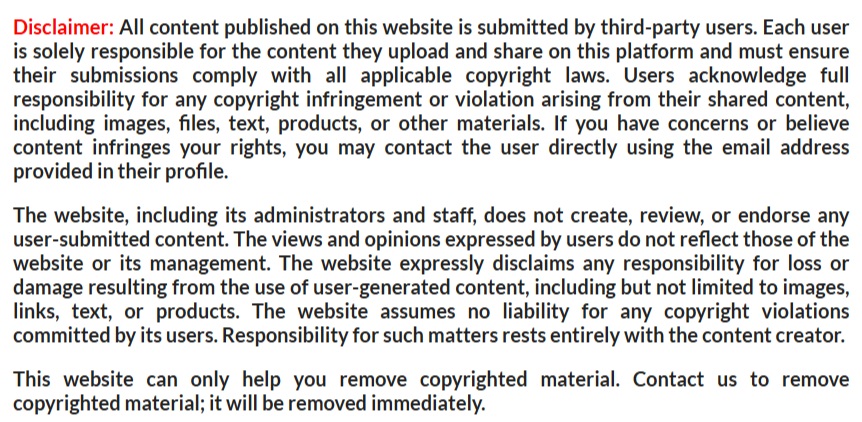