Advanced Blade Technologies Revolutionizing Industrial Applications and Wind Energy Sector Worldwide
views
Industrial blade technology has undergone remarkable transformation in recent decades, fundamentally reshaping manufacturing processes, energy generation, and precision cutting applications across multiple sectors. From aerospace manufacturing to renewable energy systems, advanced blade solutions continue to drive innovation while addressing complex industrial challenges through enhanced materials science, aerodynamic engineering, and manufacturing precision.
Modern Blade Manufacturing Processes Transforming Industrial Production Standards
Contemporary Blade manufacturing has evolved far beyond traditional forging and machining techniques, incorporating sophisticated computer-controlled processes that ensure unprecedented precision and consistency. Advanced manufacturing facilities now employ multi-axis CNC machining centers capable of producing complex blade geometries with tolerances measured in micrometers, enabling applications in high-performance turbomachinery and precision cutting systems.
The integration of additive manufacturing technologies has revolutionized prototype development and small-batch production, allowing engineers to create intricate internal cooling channels and optimized aerodynamic profiles previously impossible through conventional manufacturing methods. Investment casting processes utilizing ceramic shell molds enable the production of single-crystal blade structures, eliminating grain boundaries that could compromise structural integrity under extreme operating conditions.
Quality control systems incorporating coordinate measuring machines and non-destructive testing methods ensure every manufactured blade meets stringent specifications before deployment. Advanced surface treatments including physical vapor deposition and thermal barrier coatings extend operational lifespan while maintaining optimal performance characteristics across diverse operating environments.
Cutting-Edge Materials Science Enhancing Blade Performance and Durability
Materials science breakthroughs have fundamentally transformed blade design possibilities, introducing superalloys and composite materials capable of withstanding extreme temperatures, corrosive environments, and high-stress operating conditions. Nickel-based superalloys incorporating rhenium and ruthenium demonstrate exceptional creep resistance and thermal stability, enabling operation at temperatures approaching material melting points while maintaining structural integrity.
Carbon fiber reinforced polymer composites offer exceptional strength-to-weight ratios, making them ideal for applications requiring lightweight yet robust blade structures. These advanced composites can be tailored through fiber orientation and resin selection to optimize specific performance characteristics including stiffness, fatigue resistance, and environmental durability.
Ceramic matrix composites represent the cutting edge of high-temperature blade applications, combining ceramic fibers with ceramic matrices to create materials capable of operating at temperatures exceeding conventional superalloy limits. These materials enable next-generation turbine designs with improved efficiency and reduced cooling requirements, translating to enhanced overall system performance.
Recent developments in nanostructured coatings provide enhanced wear resistance and reduced friction coefficients, extending operational lifespan while maintaining sharp cutting edges in industrial applications. Smart materials incorporating shape memory alloys enable adaptive blade geometries that automatically adjust to changing operating conditions.
Aerodynamic Engineering Principles Optimizing Blade Design for Maximum Efficiency
Aerodynamic optimization represents a critical aspect of modern blade design, utilizing computational fluid dynamics to analyze complex flow patterns and pressure distributions across blade surfaces. Advanced modeling techniques account for three-dimensional flow effects, boundary layer interactions, and tip vortex formation to maximize lift generation while minimizing drag penalties.
Sophisticated blade profiling techniques incorporate variable chord lengths, twist distributions, and camber adjustments along the span to optimize performance across diverse operating conditions. These design approaches enable consistent performance whether operating under steady-state conditions or dynamic load variations common in real-world applications.
Leading-edge and trailing-edge modifications including micro-vortex generators and serrated edges help control boundary layer separation and reduce noise generation while maintaining aerodynamic efficiency. These features prove particularly valuable in applications where acoustic considerations play important roles in system acceptance and regulatory compliance.
Multi-element blade designs incorporating slats and flaps enable enhanced performance across broader operating ranges, automatically adjusting effective blade camber and angle of attack through passive or active control systems. Such designs prove particularly beneficial in variable-speed applications where maintaining optimal efficiency across diverse operating points presents significant engineering challenges.
Wind Energy Applications Driving Innovation in Large-Scale Blade Development
Wind energy applications have emerged as major drivers of blade technology advancement, pushing the boundaries of size, efficiency, and durability requirements. Modern wind turbine blades incorporate sophisticated aerodynamic designs optimized for specific wind conditions and installation locations, utilizing detailed wind resource assessments to tailor blade characteristics for maximum energy capture.
Large-scale wind turbine blades present unique engineering challenges related to transportation, installation, and structural dynamics. Innovative solutions including segmented blade designs and on-site assembly techniques enable deployment of increasingly large blade structures while managing logistical constraints associated with ground transportation and crane capacity limitations.
Get more insights on, Blade
Get This Report in Japanese Language: ブレード
Get This Report in Korean Language: 블레이드
Read More Articles Related to this Industry- Emerging Trends in Consumer Goods: The Rise of Meal Kit Services
About Author:
Ravina Pandya, Content Writer, has a strong foothold in the market research industry. She specializes in writing well-researched articles from different industries, including food and beverages, information and technology, healthcare, chemical and materials, etc. (https://www.linkedin.com/in/ravina-pandya-1a3984191)
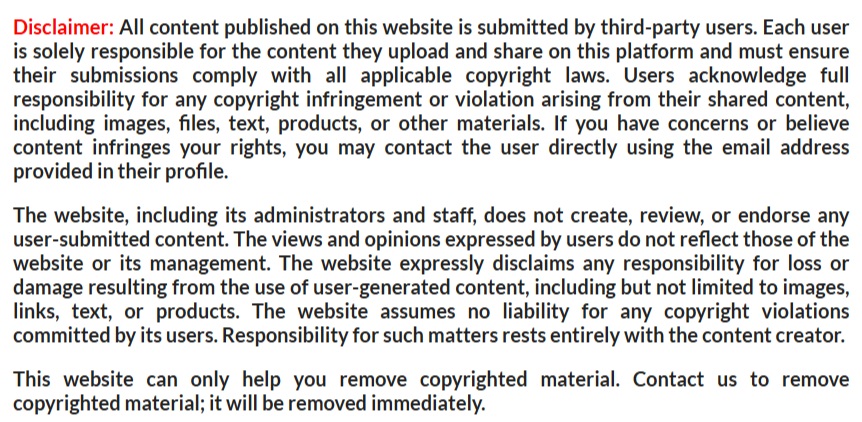