views
A wide spectrum of industries implements air and gas compression systems from manufacturing and healthcare to energy and transportation. The technology behind industrial air compressors technology has undergone substantial advancement to deliver better system effectiveness together with reliable operation and improved performance capabilities. But what exactly makes these machines indispensable? Which gas compression technologies match business needs in specific industrial sectors? The article explains compressor classifications together with their utilization scenarios and shows how their working systems function.
Understanding Industrial Air Compressors
The fundamental function of industrial air compressors consists of transforming power into pressurized air energy through compression. The compressed air becomes a power source for both industrial tools and essential industrial manufacturing applications in automotive, pharmaceutical and food processing plants. Many aspects of industrial compression systems determine what type of compressor should be applied among pressure demands and operation durations and production requirements.
The Science behind Gas Compression Technology
The fundamental principle of gas compression technology serves multiple economic sectors such as the oil and gas industry combined with chemical processing and heating ventilation air conditioning (HVAC) systems. These compressors increase gas pressure levels of oxygen, nitrogen, natural gas to support their transportation, storage and use throughout different industrial applications. Industrial systems use gas compression efficiency to determine energy consumption levels as well as operational costs.
- Exploring Reciprocating Compressor Types
Several industries depend on reciprocating compressors for their compression operations. Multiple-stage compression occurs when air or gas gets compressed using cylinders that contain pistons to perform this operation. Manufacturing plants together with refineries depend on reciprocating compressor types because these devices possess strong construction along with capability to work as needed. Sound operation of reciprocating compressors depends on scheduled maintenance combined with appropriate lubrication of air compressors.
2. The Reliability of Rotary Screw Compressors
Machine operations with continuous demand find their perfect solution through rotary screw compressors because they deliver exceptional reliability performance. The efficient compression process from helically arranged interlocking screws makes these compressors optimal for use in factories and processing plants requiring stable air supply.
The compressor range of Atlas Copco includes both oil-free and oil-injected models which customers can select based on operational purity standards. Low maintenance expenses for rotary screw compressors outnumber those of reciprocating compressors which drives industries toward their selection.
Read full Article: https://www.plantautomation-technology.com/articles/a-complete-guide-to-air-gas-compressors

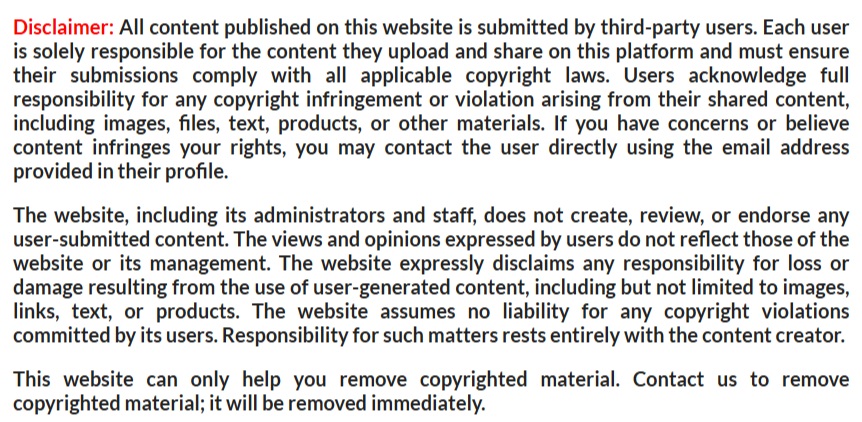
Comments
0 comment