views
When bringing a new product to market, one of the earliest and most consequential decisions you'll make isn't about marketing strategy or pricing—it's about your design approach. The methodology you choose fundamentally impacts everything from production costs and timelines to your product's ultimate quality and performance.
Today's manufacturing landscape presents two primary design philosophies: traditional Design for Manufacturing (DfM) and the newer, increasingly important Design for Additive Manufacturing (DfAM). These approaches represent fundamentally different ways of thinking about how your product will come to life.
For companies seeking design for manufacturing solutions, understanding the distinction between these methodologies isn't just academic—it's essential to your bottom line. Choose incorrectly, and you might face unnecessary costs, production delays, or even design compromises that affect your product's functionality.
In this comprehensive guide, we'll explore:
-
The fundamental principles behind DfM and DfAM
-
Critical differences in approach and application
-
How to determine which methodology fits your specific product needs
-
Real-world applications in various industries, including medical devices
-
Integration strategies that leverage the best of both worlds
-
Future trends shaping design for manufacturing
Whether you're developing consumer products, medical devices, industrial equipment, or specialized components, understanding these design approaches will empower you to make informed decisions that optimize both production efficiency and product performance. Let's dive into the details that matter.
Ready to optimize your product design process? Schedule a consultation call with our engineering team to identify the ideal design approach for your specific needs.
What is Design for Manufacturing (DfM)?
Design for Manufacturing (DfM) represents a traditional but highly refined approach to product development that focuses on optimizing designs for efficient, cost-effective production using conventional manufacturing methods. This methodology has been the backbone of industrial production for decades, evolving alongside manufacturing technologies to create increasingly sophisticated products.
Core Principles of DfM
At its heart, DfM involves anticipating and addressing manufacturing requirements during the earliest stages of product design. Rather than creating a design and then figuring out how to manufacture it (often leading to costly redesigns), DfM integrates manufacturing considerations from day one.
The fundamental principles of design for manufacturing services include:
-
Material Selection Optimization: Choosing materials that balance performance requirements with manufacturing constraints and cost considerations.
-
Production Process Alignment: Designing components specifically for the intended manufacturing process, whether injection molding, CNC machining, sheet metal fabrication, or other traditional methods.
-
Assembly Simplification: Reducing part count, minimizing assembly steps, and standardizing components to streamline production.
-
Tolerance Management: Designing with appropriate tolerances that maintain functionality while avoiding unnecessarily tight tolerances that drive up costs.
When implemented properly, design for manufacturing solutions lead to products that not only perform as intended but can be efficiently produced at scale with consistent quality.
DfM for Traditional Manufacturing Methods
Different manufacturing processes come with their own design requirements and constraints. Let's explore how DfM principles apply to common production methods:
Injection Molding
Design for Injection Molding requires specific considerations like:
-
Uniform wall thicknesses to prevent warping and sink marks
-
Appropriate draft angles for smooth part ejection
-
Strategic rib placement for structural integrity without excessive material
-
Gate location planning to minimize visible marks and optimize flow
These considerations are particularly important for high-volume production, where minor design inefficiencies can multiply into significant costs across thousands or millions of units.
CNC Machining
DfM for machined parts focuses on:
-
Designing geometries accessible to cutting tools
-
Minimizing the number of machine setups required
-
Avoiding deep pockets that require specialized tooling
-
Planning for fixturing and workholding during fabrication
Here's the thing: while these traditional manufacturing methods have significant limitations, they've been refined over decades to achieve remarkable efficiency when designs properly accommodate their constraints.
DfM in Medical Device Development
One area where traditional DfM remains particularly crucial is in DFM for medical devices. The medical device industry faces unique challenges that make thoughtful design for manufacturing essential:
-
Regulatory requirements demand consistent quality and traceability
-
Patient safety depends on manufacturing precision and reliability
-
Sterilization requirements influence material and design choices
-
High-volume production must maintain exacting standards
For medical device manufacturers, integrating DfM principles early in development helps navigate these challenges while controlling costs. The structured approach of traditional DfM aligns well with the documentation requirements and validation protocols common in regulated industries.
Now let's dive into how additive manufacturing is changing this landscape.
Understanding Design for Additive Manufacturing (DfAM)
While traditional manufacturing methods subtract material (cutting, drilling) or reshape it (molding, forming), additive manufacturing builds objects layer by layer. This fundamental difference requires an entirely different design approach: Design for Additive Manufacturing (DfAM).
Breaking Free from Traditional Constraints
DfAM represents a paradigm shift in how we think about product design. Rather than designing around the limitations of conventional manufacturing processes, DfAM embraces the unique capabilities of additive technologies. This approach offers extraordinary freedom to create previously impossible geometries.
The core advantages of DfAM include:
-
Complex Geometries: Creating internal channels, lattice structures, and organic shapes that would be impossible or prohibitively expensive with traditional methods.
-
Part Consolidation: Combining multiple components into single, complex parts to eliminate assembly steps and potential failure points.
-
Mass Customization: Economically producing variations of a design without the tooling changes required by traditional manufacturing.
-
Weight Optimization: Developing structures that use material only where needed for strength while minimizing weight in non-critical areas.
What does this mean for you? The ability to reimagine products entirely rather than simply adapting existing designs to manufacturing constraints.
DfAM Principles and Methodologies
Effective DfAM requires understanding both the capabilities and limitations of various additive technologies. Each 3D printing process—whether powder bed fusion, material extrusion, vat photopolymerization, or others—comes with its own design considerations.
Topology Optimization
One of the most powerful DfAM approaches is topology optimization, which uses computational algorithms to determine the optimal material distribution within a design space. This data-driven approach creates structures that:
-
Maximize strength-to-weight ratios
-
Distribute stress more effectively
-
Reduce material usage while maintaining performance
-
Often result in organic, non-intuitive geometries
Support Structure Considerations
Unlike traditional manufacturing, many additive processes require support structures for overhangs and other challenging geometries. Effective DfAM addresses this by:
-
Orienting parts to minimize support requirements
-
Designing self-supporting features where possible
-
Creating easily removable supports that don't compromise surface finish
-
Incorporating supports as functional elements of the final design
When DfAM Excels
Design for Additive Manufacturing offers particular advantages in certain scenarios:
-
Low-volume, high-complexity parts where tooling costs would be prohibitive
-
Highly customized products tailored to individual user requirements
-
Lightweighting applications in aerospace, automotive, and other weight-sensitive industries
-
Consolidated assemblies that reduce part count and assembly complexity
-
Fluid flow optimization through complex internal channels and structures
Now that we've explored both approaches individually, let's examine how to determine which one best suits your specific project needs.
Choosing the Right Approach: Decision Factors
Selecting between DfM and DfAM isn't a matter of which approach is universally "better"—it's about identifying which methodology aligns with your specific product requirements, production volumes, and business objectives. Here's a systematic framework to guide your decision.
Production Volume Considerations
One of the most significant factors in your design approach decision is the anticipated production volume:
High-Volume Production
For products produced in thousands or millions of units, traditional design for manufacturing solutions often remain the most cost-effective approach. While initial tooling costs for processes like injection molding can be substantial, these costs amortize across large production runs, resulting in very low per-unit manufacturing costs.
DfM excels here because:
-
Per-part costs decrease dramatically at scale
-
Process consistency and quality control are well-established
-
Production speeds for conventional methods typically outpace additive manufacturing
Low-Volume Production


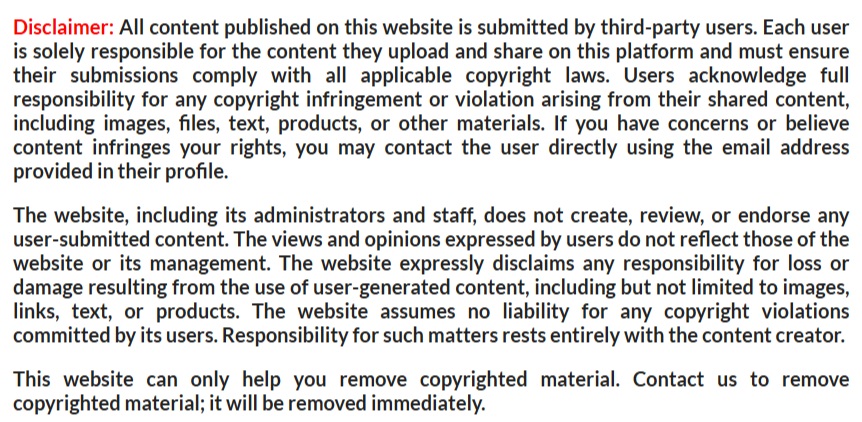
Comments
0 comment