views
Introduction
The Distributed Control Systems market is undergoing a transformation driven by Industry 4.0 and the Internet of Things (IoT). As industries embrace digitalization, DCS solutions are evolving to integrate real-time data analytics, machine learning, and cloud connectivity. This article explores how Industry 4.0 and IoT are shaping the future of the DCS market.
Role of Industry 4.0 in DCS Evolution
1. Smart Automation and Connectivity
Industry 4.0 emphasizes intelligent automation, where DCS solutions leverage IoT-enabled sensors, AI algorithms, and digital twins to improve process control. This enables manufacturers and energy providers to achieve higher efficiency, reduce downtime, and enhance predictive maintenance capabilities.
2. Data-Driven Decision Making
DCS platforms are now integrated with big data analytics and AI, allowing real-time monitoring and optimization of industrial operations. AI-driven insights help operators detect anomalies, optimize workflows, and reduce energy consumption.
3. Cyber-Physical Systems (CPS) and Digital Twins
Digital twin technology is revolutionizing DCS by enabling virtual models of industrial processes. These cyber-physical systems allow for simulation, testing, and optimization of plant operations before implementation, improving safety and reducing costs.
4. Edge Computing for Real-Time Processing
Edge computing is playing a crucial role in enhancing DCS performance by processing data closer to the source. This reduces latency and ensures real-time responsiveness, critical for industries like oil & gas, power generation, and manufacturing.
Impact of IoT on DCS Market
1. Seamless Interconnectivity and Remote Monitoring
IoT-enabled DCS solutions facilitate remote monitoring and control of industrial processes, allowing operators to access data and manage systems from anywhere. This has become increasingly important in ensuring business continuity and reducing operational costs.
2. Enhanced Predictive Maintenance
With IoT integration, DCS solutions can continuously collect and analyze machine data to predict equipment failures before they occur. This reduces unplanned downtime and extends asset lifespan, improving overall efficiency.
3. Cloud-Based DCS Solutions
Cloud computing is reshaping DCS architecture, allowing for scalable, flexible, and cost-effective automation solutions. Cloud-based DCS platforms enable industries to store and analyze vast amounts of operational data securely.
4. Cybersecurity Challenges and Solutions
As IoT-connected DCS systems expand, cybersecurity threats become a major concern. Modern DCS solutions incorporate multi-layered security protocols, AI-driven threat detection, and encrypted communication to protect critical infrastructure from cyberattacks.
Future Opportunities and Challenges
Opportunities:
-
Expansion of smart factories and smart grids powered by IoT and AI-driven DCS solutions.
-
Growth of 5G-enabled industrial automation, improving data transmission speeds and connectivity.
-
Increased adoption of sustainable, energy-efficient automation systems.
Challenges:
-
Integration complexity with existing legacy systems.
-
High initial investment costs for Industry 4.0-ready DCS solutions.
-
Cybersecurity risks due to increased connectivity and IoT adoption.
Conclusion
The integration of Industry 4.0 and IoT is revolutionizing the DCS market, making industrial automation smarter, more efficient, and more interconnected. As businesses strive for greater operational efficiency, remote management, and predictive capabilities, DCS providers must innovate to meet these demands. Moving forward, companies that leverage AI, cloud computing, and cybersecurity in their DCS solutions will lead the future of industrial automation.
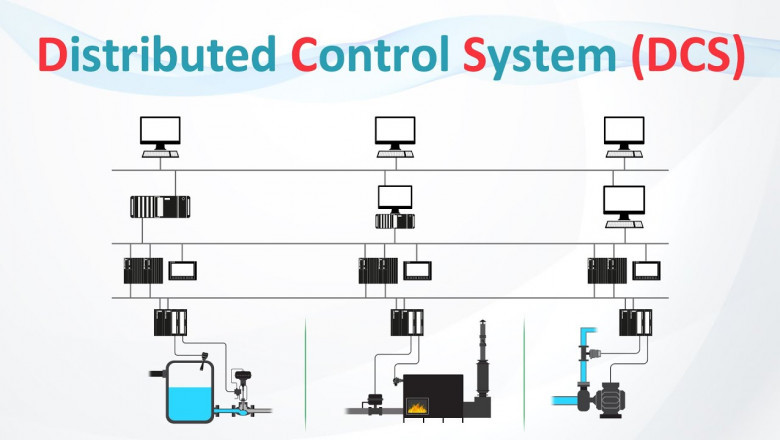

Comments
0 comment