views
The efficiency of industrial systems, driven by automation and the Industrial Internet of Things (IIoT), hinges on constant software updates and real-time management. OTA meaning allows industries to manage devices and applications remotely, reducing the need for manual interventions and costly downtime. This evolution signifies a paradigm shift in how industrial systems operate and interact.
Evolution of Industrial Systems and the Rise of OTA
The dawn of the fourth industrial revolution, or Industry 4.0, has brought forth unprecedented levels of automation, data exchange, and connectivity. As industries embrace IoT, smart devices, and robotics, the need for agile systems capable of continuous optimization has skyrocketed. OTA technology directly addresses this demand by enabling real-time updates and configurations across diverse devices and platforms without the logistical challenge of physical updates.
The integration of OTA into Industrial 4.0 ecosystems ensures seamless synchronization between interconnected devices, empowering businesses to achieve maximum efficiency. OTA’s ability to push software updates instantly across a vast array of devices mitigates the risk of outdated software or inconsistent system behavior, thus improving overall system performance and reliability.
Key Benefits of OTA for Industrial 4.0
Streamlined Software Updates
One of the most significant advantages of OTA technology is its ability to streamline the process of software updates. In traditional industrial settings, software updates often require technicians to manually install patches or upgrade systems, a time-consuming and labor-intensive process. With , these updates can be pushed remotely, saving both time and resources.
Additionally, the updates are delivered automatically, ensuring that all devices across the network are on the same version. This eliminates the risks associated with outdated software, such as security vulnerabilities and inefficient performance.
Enhanced Security Protocols
As industrial systems become more connected, security risks increase. OTA meaning is a critical enabler in fortifying security protocols by ensuring devices are equipped with the latest security patches. Without timely updates, industrial systems become susceptible to cyber-attacks, which can disrupt operations and cause severe financial losses.
OTA enables regular, automated security updates to all connected devices in a timely manner, significantly reducing the risk of data breaches or system failures due to vulnerabilities. This proactive approach to cybersecurity strengthens the overall resilience of the industrial infrastructure.
Reduced Downtime and Increased Productivity
System downtime, whether from software errors, malfunctioning hardware, or outdated software, has an immediate and detrimental effect on productivity. OTA updates help prevent such issues by ensuring that systems are always running the most current software version. In scenarios where maintenance is required, OTA allows for rapid troubleshooting and issue resolution, reducing the time spent on manual interventions.
By minimizing downtime and ensuring optimal system performance, OTA updates contribute to enhanced operational productivity, allowing businesses to maintain a competitive edge in the ever-evolving industrial landscape.
OTA in the Context of Industrial IoT
Importance of OTA for IoT Device Management
The Industrial IoT ecosystem relies heavily on a vast array of connected devices, from sensors to controllers, each of which needs to function harmoniously within the larger system. OTA technology is essential in this context, as it enables seamless updates across devices regardless of their location.
Without OTA, managing software versions across thousands of IoT devices would be a logistical nightmare. OTA allows for centralized control, where updates can be pushed across devices, ensuring that all devices operate with the most current firmware, thus maintaining system integrity.
Real-Time Data Transmission and Updates
Real-time data transmission is a cornerstone of Industrial 4.0, enabling smarter decision-making and operational control. OTA ensures that data from IoT devices is constantly updated and transmitted without requiring manual input. This immediate flow of data enables faster response times to system changes, improving the efficiency and reliability of industrial processes.
With the combination of real-time updates and data transmission, industries can rapidly adapt to changing conditions, minimizing delays and optimizing operations on-the-fly.
Minimizing Operational Risks with OTA Updates
Automated Issue Resolution
OTA technology’s ability to resolve issues automatically is a game-changer in industrial environments. In the event of a malfunction or software bug, the system can detect the issue and trigger an OTA update to resolve the problem. This automated process eliminates the need for manual troubleshooting and reduces the risk of human error.
By automating problem resolution, OTA updates not only improve efficiency but also enhance system reliability, which is vital in critical industrial applications where downtime or failure is costly.
Preventative Maintenance and Troubleshooting
Preventative maintenance is essential in industrial settings, as it minimizes the risk of unexpected equipment failure. OTA updates facilitate preventative maintenance by automatically pushing software updates that can prevent system malfunctions or failures. By addressing issues before they escalate, businesses can ensure continuous operation and avoid costly repairs.
Furthermore, OTA can support remote diagnostics, allowing technicians to troubleshoot issues without being physically present, thus saving time and resources.
OTA as a Tool for Smart Factory Management
Efficiency Boost through Remote Monitoring
In a smart factory environment, the ability to monitor operations remotely is invaluable. OTA enables remote monitoring of all devices, sensors, and systems in real-time, providing managers with a comprehensive overview of operations. This remote access allows for immediate adjustments to optimize system performance and ensure that resources are used effectively.
With OTA updates, system administrators can quickly identify inefficiencies or failures, adjusting processes remotely and thereby improving the factory's overall efficiency.
Optimization of Resources and Energy Usage
Energy efficiency is a major focus in modern industrial environments. OTA helps optimize energy consumption by delivering updates that improve the performance of energy management systems. These updates can enhance system algorithms, fine-tune energy distribution, or even schedule operations to reduce energy waste.
As a result, OTA contributes to both cost savings and sustainability by ensuring that energy resources are used efficiently across all industrial processes.
Overcoming Challenges in OTA Implementation for Industrial Systems
Network Reliability and Security Concerns
While OTA provides numerous benefits, its implementation in industrial systems is not without challenges. One of the main hurdles is ensuring reliable network connectivity across large and often remote industrial sites. Without robust networks, the delivery of updates could be delayed or incomplete, potentially causing system inefficiencies.
Moreover, security concerns surrounding data transmission and storage are critical. Ensuring that OTA updates are delivered securely and that all communications are encrypted is essential to prevent cyber threats from exploiting vulnerabilities.
Compatibility and Integration with Legacy Systems
Many industrial facilities operate with legacy systems that were not designed with OTA capabilities in mind. Integrating these older systems with newer OTA solutions requires careful planning and adaptation. Compatibility issues can arise, particularly when dealing with proprietary or outdated hardware and software.
To overcome these challenges, organizations must invest in technologies that bridge the gap between legacy systems and modern OTA infrastructure, ensuring that all components can communicate seamlessly.
Future Outlook: The Expanding Role of OTA in Industrial 4.0
Integration with AI and Machine Learning
As AI and machine learning continue to evolve, their integration with OTA meaning technology will unlock even greater efficiency gains. AI-driven OTA updates could analyze data from various devices and predict optimal update schedules based on usage patterns and system health, making updates even more intelligent and context-aware.
Machine learning algorithms could also be used to identify potential system failures before they occur, triggering preventative OTA updates to avoid operational disruptions.
Potential of OTA in Global Industrial Networks
The global nature of industrial operations means that OTA technology has vast potential to streamline updates across geographically dispersed sites. OTA enables manufacturers and industrial operators to maintain consistent, up-to-date software versions across all locations, regardless of distance or regional restrictions.
As industrial networks grow more interconnected and widespread, OTA will continue to play a pivotal role in ensuring that global industrial systems are efficient, secure, and adaptable to ever-changing demands.
for more details visit below website
https://www.regamiota.com/
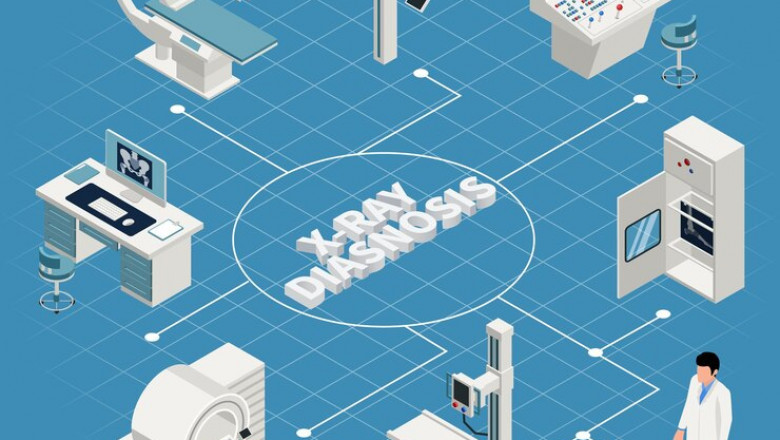

Comments
0 comment