views
Wafer Handling Robots: Revolutionizing the Global Semiconductor Supply Chain
Introduction:
In the ever-evolving world of semiconductor manufacturing, wafer handling robots have emerged as pivotal components in enhancing efficiency, precision, and automation. As the semiconductor industry continues to grow in response to rising global demand for electronics, artificial intelligence, and cloud computing, wafer handling robots are playing a crucial role in ensuring the smooth operation of wafer fabrication and processing. This article delves into the significance of robotic wafer handling, its applications in semiconductor manufacturing, and how it is shaping the future of the global semiconductor supply chain.
What is Wafer Handling?
Wafer handling refers to the process of transporting, positioning, and manipulating semiconductor wafers throughout the various stages of the manufacturing process. A wafer is a thin, flat disc made of semiconductor material, typically silicon, that serves as the substrate for fabricating integrated circuits (ICs). The handling of wafers is an essential step in the semiconductor manufacturing process, as these delicate wafers must be moved with high precision to avoid contamination, breakage, or damage.
Traditional Wafer Handling Challenges
Historically, wafer handling has been a manual or semi-automated process, relying on human operators or simple robotic systems. However, this approach has several challenges:
· Risk of Contamination: Wafers are highly sensitive to contamination. Even microscopic dust particles or oils from human hands can affect the quality of the final product.
· Inconsistent Precision: Manual handling can introduce inconsistencies in wafer placement, potentially leading to defects or yield losses.
· Labor Shortages and Costs: Manual labor is both time-consuming and expensive. Moreover, as the semiconductor industry continues to scale, the need for skilled labor is increasing, leading to workforce shortages.
· Increased Complexity: As wafer sizes and the complexity of integrated circuits grow, the need for precision in handling has become even more critical.
In response to these challenges, the semiconductor industry has increasingly turned to wafer handling robots as a solution to automate, optimize, and elevate the wafer handling process.
The Role of Wafer Handling Robots in Semiconductor Manufacturing
Robotic wafer handling systems are designed to automate the transport, alignment, and positioning of wafers during different stages of semiconductor fabrication, from photolithography to etching, deposition, and testing. These robots are equipped with specialized tools and sensors to handle wafers with extreme precision, ensuring that each step in the process is executed flawlessly.
Key Features of Wafer Handling Robots
1. High Precision: Robots are equipped with vision systems and advanced control algorithms that ensure accurate wafer placement and alignment, minimizing the risk of defects or errors.
2. Automation: Wafer handling robots are capable of working autonomously 24/7, eliminating the need for human intervention and significantly improving throughput and productivity.
3. Cleanroom Compatibility: Semiconductor fabrication occurs in ultra-clean environments, where contamination must be avoided at all costs. Wafer handling robots are designed to operate in these sterile conditions, ensuring contamination-free handling.
4. Scalability: Robots can be integrated into existing semiconductor production lines or scale to meet the demands of higher-volume production.
5. Cost-Effectiveness: By automating wafer handling processes, manufacturers can reduce labor costs, improve yield rates, and lower the risk of costly errors.
Applications of Wafer Handling Robots
Wafer handling robots are used in various stages of semiconductor manufacturing, including:
1. Wafer Loading and Unloading: Robots are responsible for loading and unloading wafers from process equipment like furnaces, etchers, and photolithography machines. They ensure the wafers are properly aligned before entering each step of the production process.
2. Wafer Sorting: Robots can sort wafers based on their specifications or quality levels. This sorting process is vital for ensuring that only the best wafers proceed to the next stage.
3. Wafer Inspection: Many wafer handling robots are equipped with optical inspection systems that check the quality of the wafers for defects or contamination, ensuring that only flawless wafers continue through the manufacturing process.
4. Wafer Cleaning: Robots are also used in cleaning operations, ensuring that wafers are free from contamination or particles before they move to the next production stage.
5. Wafer Transportation: In large semiconductor fabs, robots play a central role in transporting wafers between different stations, ensuring that each wafer follows its predetermined path with minimal human interaction.
Impact on the Global Semiconductor Supply Chain
The global semiconductor supply chain is a complex network involving the production, assembly, testing, and distribution of semiconductor devices across multiple regions. The rise of wafer handling robots has brought about significant improvements in various facets of this supply chain, particularly in terms of speed, precision, and consistency.
1. Enhancing Production Speed and Efficiency
Wafer handling robots have drastically improved production speed by automating time-consuming tasks. Unlike manual handling, robots can perform these tasks quickly and with greater accuracy, reducing the cycle time for each wafer. The automation of wafer handling also allows semiconductor fabs to run at full capacity, increasing throughput and minimizing production downtime.
This is especially important in the context of high-demand periods, such as during the launch of new consumer electronics or other semiconductor-driven technologies. With faster production timelines, semiconductor manufacturers can meet market demand more efficiently, reducing lead times and ensuring timely product availability.
2. Addressing Labor Shortages
The semiconductor industry is facing a global labor shortage, particularly in regions where manufacturing capabilities are expanding. Labor costs in many advanced economies are rising, and there is a growing shortage of skilled workers to manage complex manufacturing processes. Wafer handling robots help mitigate these challenges by reducing reliance on human workers for repetitive, labor-intensive tasks.
In addition to improving labor efficiency, robotic systems allow human operators to focus on higher-value tasks, such as troubleshooting and system optimization, rather than spending their time on manual handling.
3. Improving Yield and Reducing Defects
In semiconductor manufacturing, even the smallest error can lead to defective products and costly waste. Wafer handling robots, with their precise motion control and automated inspection systems, significantly reduce the risk of human error, which can lead to defects in the wafer or in the final semiconductor devices.
By improving the consistency and accuracy of wafer handling, robots help optimize the overall yield in semiconductor fabrication. This reduction in defects ultimately translates to cost savings and higher-quality products, which is especially important in a highly competitive market.
4. Reducing Operational Costs
The automation of wafer handling not only leads to improved productivity but also significantly reduces operational costs. As robots are able to work continuously without breaks and can perform tasks faster than humans, semiconductor fabs can operate more efficiently, which drives down the per-unit cost of manufacturing.
Additionally, robotic systems reduce the need for specialized labor, which can be expensive in regions with high labor costs. Automation also reduces the risk of accidents and equipment damage, helping to lower the overall cost of maintaining production lines.
5. Supporting Scalability and Flexibility
As demand for semiconductors continues to rise globally, the ability to scale production quickly is becoming more critical. Wafer handling robots are integral to the scalability of semiconductor manufacturing. They can easily be integrated into existing systems or expanded to meet increased production requirements, without the need for significant changes to the overall facility infrastructure.
Moreover, the adaptability of wafer handling robots allows semiconductor manufacturers to quickly pivot to new production lines or processes, depending on market demand or technological advancements.
The Future of Wafer Handling Robots
The future of wafer handling robots is closely tied to advancements in technology, such as artificial intelligence (AI), machine learning, and robotics. These technologies are enabling robots to become more intelligent, autonomous, and capable of performing increasingly complex tasks.
Integration with AI and Machine Learning
As AI and machine learning continue to evolve, wafer handling robots will become more capable of predictive maintenance, adaptive learning, and process optimization. Robots can analyze data in real-time to predict when a piece of equipment might fail or when a process might be suboptimal, allowing for quicker interventions and reducing downtime.
Collaboration with Human Workers
While robots will continue to handle the bulk of wafer handling tasks, there will likely be greater collaboration between robots and human operators in the future. Human workers will be able to focus on high-level decision-making and system management, while robots handle the routine, repetitive tasks that were once time-consuming and error-prone.
Miniaturization and Higher Precision
As semiconductor devices continue to shrink in size and become more intricate, wafer handling robots will need to evolve as well. The future of wafer handling robots will likely see more precise and smaller robots that can handle smaller wafers and more delicate components. The focus will be on enhancing robotic precision to match the increasing demand for smaller, more powerful semiconductors.
Conclusion
Wafer handling robots have become indispensable in the modern semiconductor industry. By improving speed, efficiency, and precision, these robots are helping manufacturers meet the growing global demand for semiconductors while minimizing defects, reducing costs, and addressing labor shortages. As the semiconductor industry continues to grow and innovate, wafer handling robots will play an even more crucial role in supporting the complex global supply chain and ensuring that the next generation of electronic devices can be produced with greater accuracy, efficiency, and reliability.
See the full article: https://www.nextmsc.com/blogs/wafer-handling-robots-market-trends
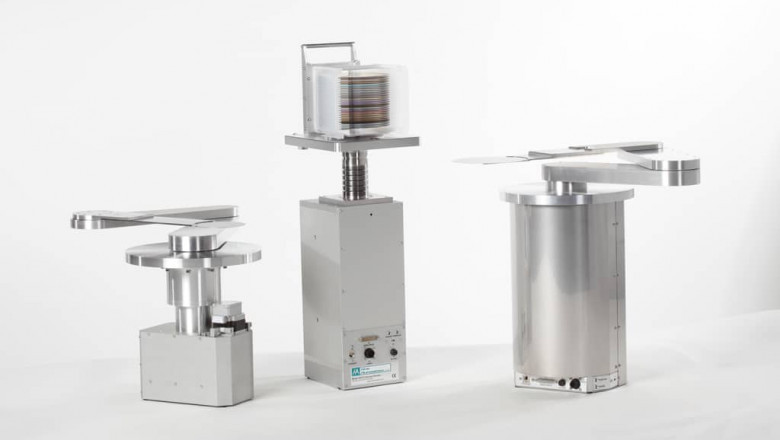

Comments
0 comment