views
Introduction:
The OLED Inkjet Printing Market has revolutionized the display industry, especially in consumer electronics like smartphones, tablets, and television sets. OLED displays are known for their superior picture quality, vivid colors, deep contrasts, and flexibility, which have made them increasingly popular in high-end consumer electronics. However, while OLED displays have seen widespread adoption in small devices, the manufacturing process for large-scale OLED TV displays remains an area of intense research and development. One of the most promising innovations for producing large OLED displays efficiently is inkjet printing.
OLED inkjet printing is an advanced method that uses inkjet technology to precisely deposit organic materials onto substrates, offering substantial advantages over traditional OLED production methods, such as vacuum deposition. For large-scale OLED TV displays, this technology presents both unique opportunities and significant challenges that manufacturers must overcome. In this article, we will explore the potential of OLED inkjet printing for large-scale TV displays, highlighting the challenges and opportunities that come with this cutting-edge technology.
What is OLED Inkjet Printing?
OLED inkjet printing refers to the process of using inkjet technology to print organic materials directly onto a substrate in precise, controlled patterns. Unlike traditional vacuum deposition methods, which require the use of expensive equipment and involve high temperatures in a vacuum chamber, inkjet printing allows for more direct, cost-effective production of OLED panels. The inkjet printing method deposits tiny droplets of organic inks onto substrates, which are then cured to form OLED layers.
In the context of OLED TV displays, inkjet printing can be used to create the light-emitting layers of the display as well as the conductive and protective layers. This printing method provides higher precision and reduces waste by depositing only the required amount of ink. Moreover, OLED inkjet printing opens up possibilities for flexible OLED displays, making it possible to design large-scale TV displays that are thinner, lighter, and more adaptable to different form factors.
Why is OLED Inkjet Printing Ideal for Large-Scale TV Displays?
The large-scale TV display market demands cutting-edge technology to produce high-resolution, large-area, and cost-efficient OLED panels. OLED inkjet printing offers several key advantages over conventional methods for producing large OLED displays:
1. Cost-Effectiveness: Traditional OLED manufacturing methods, such as evaporation or sputtering, are expensive due to the cost of equipment and material wastage. Inkjet printing reduces material waste by precisely depositing ink only where it’s needed, which can drive down the overall cost of production. This cost reduction is particularly important for large-scale OLED TV panels, where every inch of material counts.
2. Precision and Scalability: Inkjet printing allows for high precision, ensuring uniformity in the printed OLED layers. As the OLED industry seeks to scale up production to meet growing demand for large-size TV displays, inkjet printing offers a scalable solution. This method can be adapted for large-area substrates, and the speed of inkjet printing can be increased to meet the volume needs of mass production.
3. Flexibility and Innovation: Inkjet printing is not just for rigid panels; it can also be used to print OLED layers on flexible substrates, enabling new designs for large-screen TVs that are thinner and lighter. Flexible OLED displays can be curved or even rolled up, opening up new possibilities for both form and function.
4. High Resolution: Inkjet printing offers the capability to print OLED materials with high resolution, which is essential for the sharp, high-definition displays required in large-scale TV applications. The ability to precisely print small droplets of ink means that the display’s pixel density and overall image quality can be maintained at the highest standards.
Challenges in Using OLED Inkjet Printing for Large-Scale TV Displays
While the potential of OLED inkjet printing for large-scale TV displays is immense, several challenges must be addressed before it becomes the dominant method in OLED TV manufacturing. These challenges range from material science to production scalability.
1. Material Compatibility and Ink Development
One of the primary hurdles in OLED inkjet printing is developing inks that are compatible with inkjet printing technology while also delivering the desired performance in OLED displays. OLED inks must meet several criteria: they must be highly stable, have the right viscosity for precise deposition, and be capable of forming high-quality layers without degradation.
The organic materials used for OLED displays, such as light-emitting compounds, hole transport layers, and electron transport layers, need to be formulated into inks that flow well through the print head, deposit uniformly, and adhere effectively to substrates. Furthermore, these inks must be carefully developed to prevent clogging or degradation during the printing process, and they must ensure the longevity and durability of the OLED display.
2. Curing and Drying of Printed Layers
Once the ink is deposited onto the substrate, it needs to be cured or dried to form solid OLED layers. Traditional curing methods, such as thermal curing or vacuum baking, may not be suitable for inkjet-printed OLEDs. As a result, manufacturers must develop photonic curing technologies or alternative low-temperature curing methods that ensure the printed layers maintain their properties without damaging the OLED materials.
Additionally, the uniformity of curing becomes even more crucial when working with large-area displays. Uneven curing can result in color inconsistencies, performance degradation, and defective OLED pixels. Therefore, specialized curing techniques and systems must be developed to meet the demands of large-scale OLED production.
3. Resolution and Uniformity in Large Panels
Maintaining high resolution and uniformity in large-scale OLED panels can be challenging. As the size of the panel increases, the consistency of inkjet-printed OLED layers across the entire surface must be ensured. Any inconsistency in ink deposition can result in defects or visual anomalies such as color inconsistencies or dead pixels.
To address this issue, the development of advanced print head technologies and improved software algorithms that control the printing process is essential. Moreover, innovations in multi-head printing and high-speed inkjet printing are necessary to meet the demands of large-format displays without sacrificing print quality.
4. Manufacturing Speed and Scale
Inkjet printing, while precise, is not inherently as fast as traditional OLED manufacturing methods like evaporation deposition, which can coat large areas much quicker. As the demand for large-scale OLED TVs continues to rise, manufacturers need to find ways to speed up the inkjet printing process without compromising quality.
Additionally, scaling inkjet printing to accommodate the production of large OLED panels (e.g., 65 inches and beyond) requires significant advancements in print head design and production line configuration. Manufacturing speed must be optimized for large-scale production while maintaining the required precision and quality.
Opportunities in OLED Inkjet Printing for Large-Scale TV Displays
Despite the challenges, OLED inkjet printing offers significant opportunities for transforming the large-scale TV display market. These opportunities are largely driven by the ongoing advancements in inkjet technology, materials, and manufacturing techniques.
1. Cost-Effective Mass Production
As OLED inkjet printing technology matures, it has the potential to drive down manufacturing costs for large-scale OLED TV displays. The ability to print organic materials directly onto substrates reduces the need for costly vacuum deposition systems and specialized equipment. Furthermore, the precision of inkjet printing minimizes material waste, allowing manufacturers to produce OLED displays more efficiently.
This reduction in production costs could lead to more affordable OLED TVs, making this premium technology accessible to a wider range of consumers. As inkjet printing technology advances, it will become an essential tool for scaling up production and meeting the growing demand for larger OLED displays at competitive price points.
2. Flexible OLED TV Displays
Inkjet printing is particularly well-suited for producing flexible OLED displays, which is a growing trend in the TV market. As consumers seek more versatile and innovative TV designs, flexible OLEDs that can be curved, bent, or even rolled up are gaining popularity. Inkjet printing allows for the creation of flexible substrates that can be used to produce OLED panels with unique shapes and form factors.
This flexibility could open the door to new TV designs and applications, such as foldable screens or wall-mounted OLED displays that can be customized to fit different spaces. Inkjet printing offers the manufacturing scalability needed to produce such innovative products in large quantities.
3. Improved Sustainability
Sustainability is becoming an increasingly important consideration in electronics manufacturing. Inkjet printing technology is inherently more sustainable than traditional methods, as it reduces material waste by using only the required amount of ink. Furthermore, inkjet printing requires less energy than vacuum deposition, contributing to a lower carbon footprint in the production process.
As the demand for eco-friendly products grows, inkjet printing offers a way for manufacturers to produce OLED TVs in a more sustainable and environmentally friendly manner, aligning with global sustainability goals.
Conclusion
The OLED inkjet printing market holds enormous potential for large-scale TV displays, offering key advantages in terms of cost-efficiency, precision, and flexibility. While challenges such as material development, curing processes, and scalability remain, the opportunities for transforming the OLED TV industry are substantial. As manufacturers continue to innovate in inkjet technology, we can expect OLED inkjet printing to play a central role in making large, high-quality OLED displays more affordable, sustainable, and adaptable.
In the coming years, the evolution of inkjet printing for OLED TVs will likely lead to more flexible, scalable, and cost-effective production techniques, paving the way for a new generation of OLED TV displays that offer superior image quality, design flexibility, and energy efficiency. For the consumer electronics industry, this will not only open up exciting possibilities in display design but will also make OLED technology more accessible to consumers worldwide.
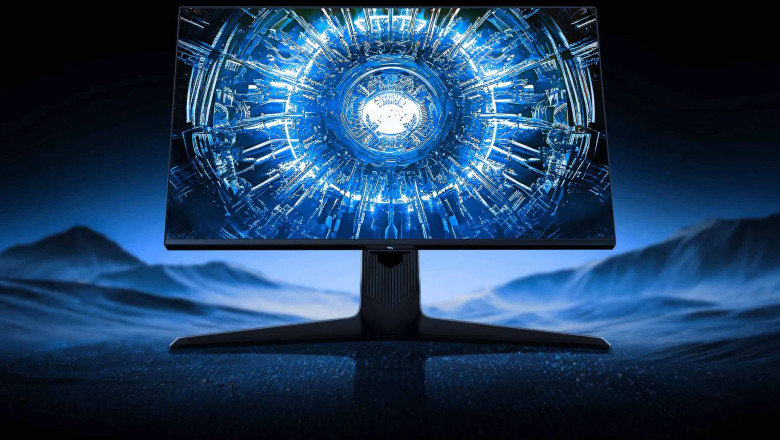

Comments
0 comment