views
Supplier quality management is a crucial aspect of medical device production. Ensuring that suppliers meet rigorous quality standards is essential to maintaining the safety and efficacy of medical devices. Medical device manufacturers must closely monitor and evaluate their suppliers to comply with stringent regulatory requirements and maintain high product standards. Supplier Quality Management Medical Devices is an ongoing process that involves constant oversight, measurement, and collaboration with suppliers. In this blog, we will explore the key metrics used to monitor supplier quality in medical device production and the importance of robust quality management systems.
Evaluating Supplier Quality Through Incoming Material Inspection
In the medical device industry, the quality of raw materials and components directly impacts the safety and performance of the final product. Incoming material inspection is one of the first and most critical metrics to monitor supplier quality. This process involves inspecting materials and components delivered by suppliers to ensure they meet the required specifications before being used in production.
How Incoming Material Inspection Impacts Product Quality
The first step in ensuring supplier quality management medical devices is evaluating the materials that suppliers provide. Raw materials that do not meet quality standards can lead to product defects, delayed timelines, or, worse, compliance issues. By performing thorough inspections, manufacturers can identify problems early, reducing the risk of Quality Control and Quality Assurance failures down the line.
The Role of Statistical Sampling in Material Inspections
For larger shipments of materials, it is often impractical to inspect every item. Statistical sampling is an essential tool in this process. By randomly sampling materials, manufacturers can assess the overall quality of the batch and decide whether to accept or reject it based on the results. This helps manage the cost and time of inspections while still ensuring that product standards are maintained.
Supplier Process Control and Monitoring
Effective supplier quality management involves more than just inspecting raw materials. Monitoring the supplier's processes is also critical to ensuring that quality standards are consistently met throughout production. Suppliers with inadequate or inconsistent processes are more likely to produce defective products that could compromise the final device’s quality and safety.
The Importance of Auditing Supplier Processes
Regular audits of supplier processes are a key metric for monitoring quality. Audits evaluate the efficiency and reliability of suppliers’ quality management systems, ensuring that they adhere to ISO standards or other applicable regulations. During an audit, manufacturers can assess whether the supplier's quality control processes are in place and effective. If a supplier fails to meet expectations, corrective actions can be taken promptly.
Supplier Process Capability and Performance Metrics
Process capability indices (such as Cp and Cpk) are essential metrics used to measure how well a supplier’s processes are performing. These indices compare the natural variability of a process with the allowable limits. Suppliers with high process capability are more likely to consistently deliver high-quality materials that meet specifications, reducing the need for rework and enhancing overall product reliability.
Supplier On-Time Delivery and Lead Time Performance
On-time delivery is another critical metric for monitoring supplier quality in medical device production. Delayed deliveries can disrupt production schedules, increase lead times, and result in higher costs. This is particularly problematic in the medical device industry, where timely product delivery is essential for maintaining regulatory compliance and meeting market demand.
Assessing Lead Time and Delivery Consistency
Lead time refers to the time between when an order is placed and when it is received. Consistent and predictable lead times are vital for maintaining production schedules and avoiding delays. Suppliers who demonstrate high levels of reliability in their delivery schedules are integral to effective supplier quality management medical devices, as they reduce the risk of production delays and ensure that manufacturing deadlines are met.
The Role of Supplier Delivery Metrics in Quality Assurance
In addition to delivery lead times, manufacturers should also track the number of late deliveries, partial shipments, and other delivery-related issues. Monitoring these metrics ensures that suppliers are consistently meeting agreed-upon timelines, which is crucial for maintaining the overall efficiency and quality of medical device production.
Supplier Nonconformance and Corrective Action Tracking
Tracking nonconformance events is a vital part of supplier quality management medical devices. Nonconformances are deviations from quality standards that can occur at any stage of production, from raw materials to the finished product. These events need to be documented, analyzed, and addressed to prevent recurrence.
Managing Nonconformance Through Root Cause Analysis
When a nonconformance occurs, it’s important to conduct a root cause analysis to identify the underlying issue. Whether it’s a material defect, a manufacturing process error, or an oversight in Quality Assurance, understanding the root cause enables manufacturers to implement corrective actions that prevent similar issues in the future. This process is vital for maintaining the quality and safety of medical devices and complying with regulatory standards.
Corrective Action Tracking and Supplier Collaboration
Once a nonconformance is identified, the next step is to track the corrective actions taken by the supplier. Manufacturers should ensure that suppliers implement corrective actions promptly and effectively. By collaborating with suppliers to address nonconformances, manufacturers can improve overall quality and reduce the likelihood of future quality control and quality assurance issues.
Supplier Quality Metrics and Performance Scoring
A comprehensive supplier Quality Management System relies heavily on tracking key performance indicators (KPIs) that measure supplier quality over time. Performance scoring involves assigning numerical values to various metrics, such as defect rates, on-time delivery, and responsiveness to issues. These scores provide a clear picture of each supplier's quality performance.
Key Performance Indicators (KPIs) for Supplier Quality
Defect rates, response times to quality issues, and the percentage of on-time deliveries are some of the most common KPIs used to evaluate supplier performance. By regularly tracking these metrics, manufacturers can identify trends, assess supplier reliability, and make data-driven decisions regarding supplier partnerships.
Supplier Performance Reviews and Ongoing Improvement
Regular performance reviews based on supplier quality metrics are essential for maintaining long-term supplier relationships. These reviews allow manufacturers to provide constructive feedback, assess whether suppliers meet expectations, and identify areas for improvement. Suppliers who demonstrate consistent performance and a commitment to quality improvement are more likely to become long-term partners.
Compliance with Regulatory Standards
In medical device production, adherence to regulatory standards is non-negotiable. Suppliers must comply with industry regulations such as the FDA’s Quality System Regulation (QSR) or ISO 13485, which sets the framework for quality management systems in medical device manufacturing. Ensuring that suppliers follow these regulations is a crucial aspect of supplier quality management medical devices.
The Role of ISO Certification in Supplier Selection
ISO 13485 certification is one of the most critical benchmarks for assessing supplier quality in the medical device industry. Suppliers that are ISO 13485 certified have demonstrated their commitment to maintaining high-quality management systems and adhering to regulatory requirements. Manufacturers should prioritize working with suppliers who hold these certifications to ensure compliance and minimize the risk of non-compliance.
Ensuring Ongoing Compliance Through Supplier Audits
Ongoing supplier audits are essential to verify that suppliers continue to comply with regulatory standards. These audits ensure that suppliers are maintaining their quality management systems and addressing any compliance gaps. Regular audits help maintain a high standard of quality and ensure that manufacturers are always working with compliant suppliers.
The Role of Quality Assurance in Supplier Quality Management
Quality assurance (QA) plays a key role in monitoring and improving supplier quality. QA teams work closely with suppliers to ensure that all materials, components, and processes meet the necessary standards before they are used in production. Integrating supplier quality management with the overall quality assurance process ensures that any potential risks to product quality and safety are identified and mitigated early.
Integrating Supplier Quality Management with Internal QA Systems
Integrating supplier quality management with internal QA systems allows for seamless communication and data sharing between manufacturers and suppliers. This integration ensures that suppliers are aligned with the manufacturer's quality expectations and that any deviations are addressed promptly. This approach helps minimize quality issues and ensures that the final product meets regulatory requirements and industry standards.
Supplier Collaboration and Continuous Improvement in Quality Assurance
Building strong relationships with suppliers is crucial for continuous improvement in quality assurance. By fostering collaboration, manufacturers and suppliers can identify areas for improvement, share best practices, and work together to address quality issues. This partnership leads to higher-quality products and a more efficient manufacturing process.
Why ComplianceQuest’s Software is Essential for Business in 2025
As medical device manufacturers continue to face increasing regulatory pressures, maintaining a robust supplier quality management system is more important than ever. ComplianceQuest’s supplier quality management medical devices software provides a comprehensive platform for monitoring supplier performance, managing nonconformances, tracking corrective actions, and ensuring regulatory compliance. By automating key processes and providing real-time insights into supplier quality, ComplianceQuest enables manufacturers to improve supplier collaboration, reduce risks, and maintain high product quality standards.
In 2025, businesses need a solution that not only helps them manage supplier quality but also ensures ongoing compliance and continuous improvement. ComplianceQuest’s software empowers manufacturers to meet these challenges, providing the tools they need to stay ahead in an increasingly complex and competitive market.
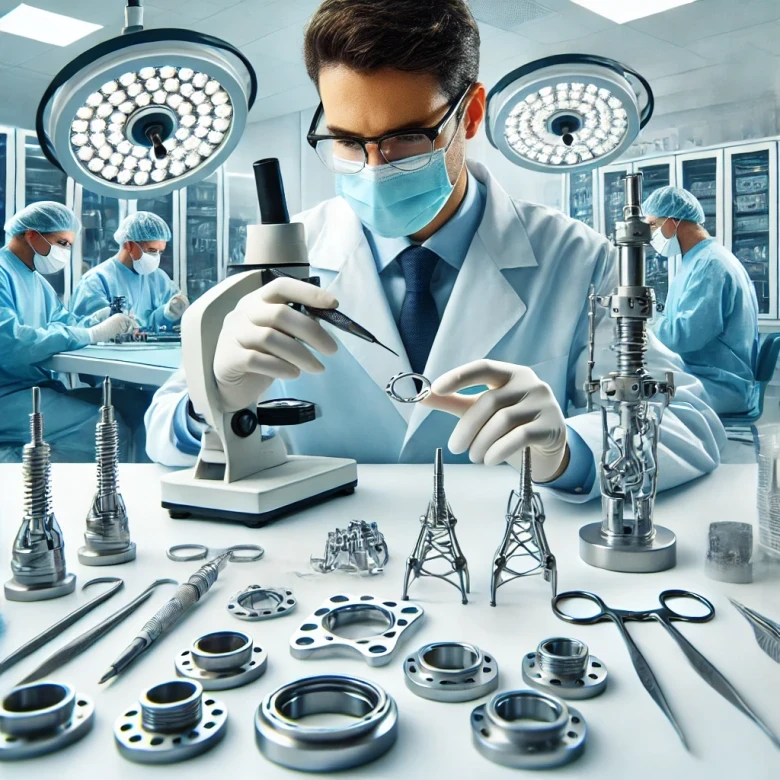
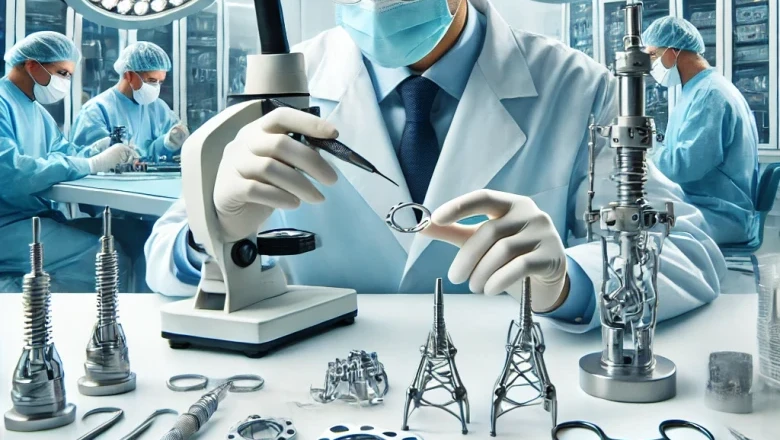

Comments
0 comment