views
1. Pre-Installation Inspection
Before any tubing goes in:
-
Verify Material Certificates: Always check that your 316 SS tubing comes with an MTC (Material Test Certificate) confirming compliance with ASTM A213/A269/A312 standards.
-
Check Dimensions & Surface: Measure outer diameter, wall thickness, and inspect for any scratches, dents, or surface imperfections that could compromise corrosion resistance.
2. Proper Handling & Storage
-
Avoid Contamination: Store tubing off the ground on clean, dry racks and cover with protective sheeting.
-
Prevent Damage: Don’t drag lengths across rough surfaces—use padded slings or carts for transport.
3. Cutting & Deburring Techniques
-
Use Sharp Tools: A fine-tooth saw or high-quality tube cutter leaves a clean cut with minimal work hardening.
-
Deburr Thoroughly: Remove burrs from inside and outside edges to prevent flow disruptions and local corrosion sites.
4. Joining Methods
-
Butt Welding: For permanent joints, use TIG welding with proper heat input and filler rod matching 316 SS. Ensure post-weld pickling to restore corrosion resistance.
-
High-Quality Fittings: If using compression or flare fittings, choose 316 SS-rated connectors and tighten to manufacturer torque specs to avoid galling.
5. Support & Alignment
-
Spacing: Install supports every 1–1.5 meters for horizontal runs and every 0.5–1 meter for vertical sections.
-
Adjustment for Expansion: Incorporate spring-type clamps or expansion loops in long runs to accommodate thermal movement.
6. Leak Testing
-
Hydrostatic Test: Pressurize the system to 1.5× operating pressure for 30 minutes and inspect for leaks.
-
Pneumatic Test: Use dry nitrogen or air with a soap-bubble inspection for small leaks—never exceed safe pressure limits.
7. Routine Maintenance & Inspection
-
Visual Checks: Quarterly inspections for signs of pitting, discoloration, or mechanical damage.
-
Clean-In-Place (CIP): For sanitary systems, follow recommended chemical cleaning cycles to remove deposits without harming the passivation layer.
-
Re-Passivation: If surface damage occurs, re-passivate with a nitric- or citric-acid bath to restore chromium oxide protection.
Conclusion
By following these installation and maintenance guidelines, you’ll ensure your 316 SS seamless tubing delivers optimal performance, minimizes downtime, and protects your investment. Whether in chemical plants, marine systems, or food-grade processes, well-handled and properly maintained tubing is the backbone of any critical fluid or gas conveyance system.
Types OF Steel Tube
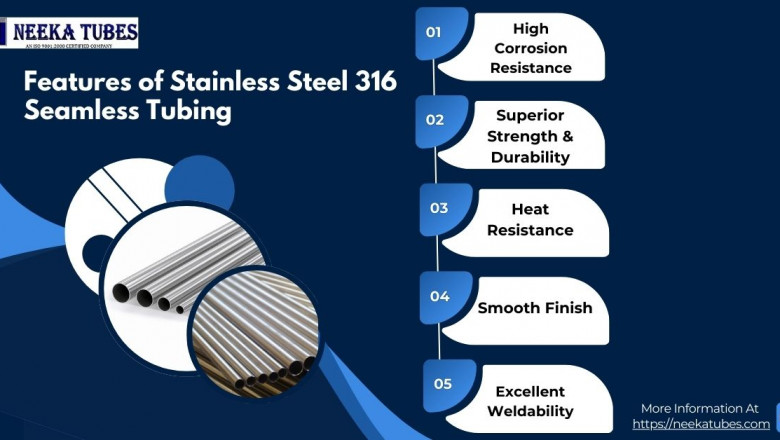

Comments
0 comment