views
In-Plant Logistics Market for E-commerce: Meeting the Demands of Speed and Accuracy
Introduction:
In recent years, the rapid growth of e-commerce has put significant pressure on supply chains, particularly in the areas of order fulfillment and logistics. With consumers expecting faster delivery times and more accurate shipments, businesses are increasingly turning to in-plant logistics solutions to meet these demands. In-plant logistics for e-commerce have become an integral part of ensuring that warehouses and distribution centers operate at peak efficiency, providing both speed and accuracy in logistics processes. In this article, we will explore how In-Plant Logistics Market operations are evolving to meet the fast-paced demands of e-commerce, focusing on key innovations like automation, real-time tracking, and warehouse management systems.
The Importance of In-Plant Logistics in E-commerce
In-plant logistics refers to the management of materials and products within a company's warehouse or manufacturing facility. This includes the processes of receiving, storing, picking, packing, and shipping orders. As e-commerce continues to grow, the demand for efficient and effective in-plant logistics becomes even more crucial. With customers increasingly expecting fast, reliable delivery, businesses must ensure that their in-plant logistics operations can handle the complexities of large order volumes, complex inventories, and the need for swift order fulfillment.
Order fulfillment is at the core of e-commerce operations. The ability to quickly and accurately process orders can make or break a company's reputation and profitability. Consumers want fast, precise deliveries, and any errors or delays in fulfilling their orders can lead to negative customer experiences and lost business. Therefore, in-plant logistics solutions need to be designed with speed and accuracy in mind to meet the heightened expectations of e-commerce consumers.
Automation: Revolutionizing In-Plant Logistics for E-commerce
One of the most significant developments in in-plant logistics for e-commerce has been the integration of automation. Automation technologies are helping businesses streamline their operations, reducing human error, and increasing overall efficiency. Automated systems like robotic picking, sorting, and packing are becoming more common in e-commerce warehouses, providing significant improvements in speed and accuracy in logistics.
Robotic picking systems, for example, use artificial intelligence (AI) and machine learning to identify and retrieve products from shelves more efficiently than human workers. These robots can navigate complex warehouse layouts, locate products quickly, and reduce the time it takes to process orders. By minimizing human error and eliminating the need for manual labor, automated picking systems help businesses fulfill orders more quickly and accurately, improving overall operational efficiency.
Automated sorting systems also play a crucial role in in-plant logistics for e-commerce. These systems can quickly sort large volumes of products based on various criteria, such as size, weight, and destination. This helps reduce bottlenecks in the fulfillment process and ensures that orders are processed as quickly as possible. Automated packing systems further enhance this process by automatically packaging products in the most efficient way, reducing waste and ensuring that items are securely packaged for transit.
Real-Time Tracking: Enhancing Visibility and Control
In today’s fast-paced e-commerce environment, real-time tracking has become an essential feature of in-plant logistics. With consumers demanding up-to-the-minute updates on their orders, businesses need to provide greater visibility into the fulfillment process. Real-time tracking allows companies to monitor inventory, track order progress, and identify potential issues before they escalate.
Warehouse management systems (WMS) that integrate real-time tracking capabilities are now commonplace in modern e-commerce logistics. These systems enable businesses to track inventory levels, monitor the movement of goods throughout the warehouse, and update order statuses in real-time. This level of visibility helps improve the accuracy of order fulfillment and reduces the chances of errors, such as shipping incorrect items or sending orders to the wrong locations.
Real-time tracking also allows businesses to respond more quickly to unexpected disruptions. For example, if an item is out of stock or there’s an issue with an order, the system can flag the problem immediately, allowing warehouse managers to take corrective action. This helps prevent delays and ensures that customers receive their orders on time, which is essential for maintaining customer satisfaction and loyalty.
Warehouse Management Systems: The Backbone of Efficient In-Plant Logistics
Warehouse management systems (WMS) are the backbone of modern in-plant logistics operations. These systems provide the tools needed to manage the entire logistics process, from receiving and storing products to picking, packing, and shipping orders. WMS software helps optimize warehouse operations by automating tasks, improving inventory control, and ensuring accurate order fulfillment.
In the context of e-commerce, WMS solutions are increasingly being integrated with other technologies, such as automation and real-time tracking systems. This creates a unified platform that enables businesses to streamline their logistics operations, reduce manual labor, and improve overall efficiency. With WMS, e-commerce businesses can better manage inventory, optimize order picking routes, and ensure that products are shipped out in the most efficient manner.
For example, advanced WMS software can analyze historical data to determine the most efficient layout for a warehouse, ensuring that products are stored in locations that make them easy to access. Additionally, WMS can prioritize orders based on factors such as shipping deadlines, customer preferences, and inventory levels, helping businesses meet tight delivery timelines.
Meeting the Demands of Speed and Accuracy
As e-commerce continues to grow, so do the demands for speed and accuracy in logistics. Consumers expect faster delivery times, and businesses must meet these expectations without compromising on the accuracy of their orders. In-plant logistics operations must evolve to accommodate these demands, leveraging the latest technologies and practices to ensure efficient and error-free order fulfillment.
One of the key strategies for meeting these demands is the implementation of advanced forecasting and demand planning tools. By using data analytics and machine learning algorithms, businesses can better predict customer demand, optimize inventory levels, and ensure that they have the right products available at the right time. This helps reduce stockouts and ensures that products are readily available for order fulfillment, ultimately improving delivery speed and accuracy.
Another important aspect of meeting the demands of speed and accuracy is the optimization of order picking processes. In e-commerce warehouses, the order picking process is often one of the most time-consuming and labor-intensive tasks. By using technologies like voice picking, pick-to-light systems, and automated guided vehicles (AGVs), businesses can speed up the order picking process and reduce the risk of errors.
Voice picking systems, for example, allow workers to receive instructions via headset, guiding them to the correct location in the warehouse to pick the necessary items. This eliminates the need for workers to reference paper picking lists, which can be time-consuming and prone to errors. Pick-to-light systems use lights and displays to direct workers to the correct products, further reducing the time spent on order picking and increasing accuracy.
Challenges in In-Plant Logistics for E-commerce
Despite the many benefits of in-plant logistics for e-commerce, businesses still face several challenges in implementing and maintaining efficient logistics operations. One of the primary challenges is the high initial cost of automation and technology integration. While automation can significantly improve efficiency and reduce labor costs in the long term, the upfront investment can be substantial, especially for smaller businesses.
Another challenge is the need for continuous staff training. As new technologies are implemented, warehouse workers must be trained to use these systems effectively. This requires an investment in training programs and ongoing support to ensure that employees can keep up with changes in technology and processes.
Finally, businesses must also navigate the complexities of inventory management. With e-commerce orders often involving smaller quantities of products spread across multiple channels, managing inventory can be challenging. Accurate inventory tracking and forecasting are essential to avoid stockouts and overstocking, which can result in missed sales opportunities or increased costs.
Conclusion
In-plant logistics for e-commerce have become a critical component of meeting the demands of speed and accuracy in today’s fast-paced marketplace. As e-commerce continues to evolve, businesses must adopt new technologies and practices to keep up with consumer expectations. Automation, real-time tracking, and warehouse management systems are key to optimizing in-plant logistics operations, reducing errors, and improving order fulfillment efficiency.
By embracing these innovations, businesses can enhance their supply chain operations, ensure faster delivery times, and provide a more accurate and reliable service to customers. The future of in-plant logistics for e-commerce looks bright, with continued advancements in automation and technology paving the way for even greater levels of efficiency and customer satisfaction.
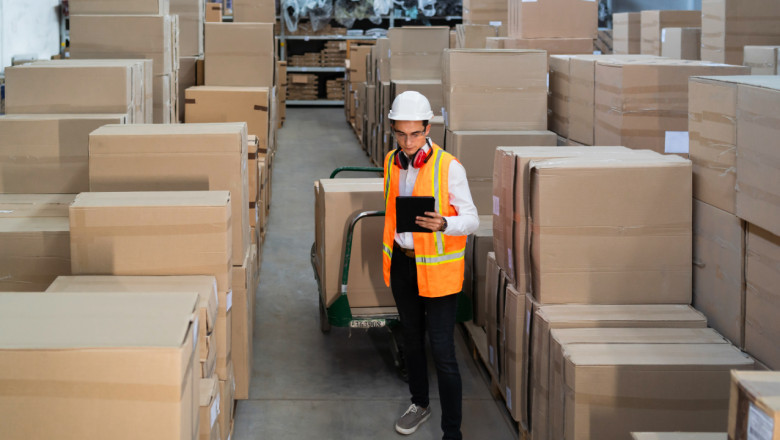

Comments
0 comment