views
What is Hand Tools?
Broaching T is a machining process used to produce linear or straight line grooves, flat surfaces or internal/external planar surfaces in a workpiece by means pulling/pushing it horizontally through a stationary multi-tooth cutting tool called a broach. The broach has multiple teeth arranged linearly to remove material in a single pass.
How does Hand Tools work?
In broaching T, the broach tool has specially designed teeth that remove thin layers of material when moved linearly across the workpiece. The broach can be either fixed or moving while the workpiece moves. As the workpiece moves through the broach, individual teeth scrape away thin layers of material to create the desired shape or dimensions. Cutting usually proceeds sequentially from tooth to tooth. Lubrication is applied during broaching to dissipate heat from the cutting zone and flush away swarf or metal chips. Broaching provides a high degree of accuracy and precise dimensional control.
Key Features of Broaching T
- produces straight-line grooves, flat surfaces, or planar internal/external profiles
- removes thin layers of material with each tooth in a single pass for dimensional accuracy
- multitooth broach cuts sequentially along its length for fast removal of material
- processes internal or external surfaces of complicated geometries and profiles
- leaves a smooth finish comparable to grinding in most cases
- capable of large volume production since it is a single-point cutting process
- repeatability and precision of +/- 0.00005" or better can be achieved
Main Types of Broaching T
There are different types of hand tools based on the configuration of the broach tool and the machining direction:
Straight Line Broaching
Straight line Hand Tools involves moving the workpiece linearly through a stationary broach tool. It is used to produce flat, straight surfaces or linear profiles in the workpiece.
Circular Broaching
In circular broaching, the broach tool moves in a circular motion while the workpiece remains stationary. It is used to cut internal ring shapes or polygons in cylindrical workpieces.
Form Broaching
Form broaching uses a broach tool with undulating teeth that follow a contoured profile. It is used to cut complex internal or external shapes in the workpiece in a single pass.
Jumper Broaching
Jumper broaching uses multiple broach stations where the workpiece 'jumps' from one broaching station to the next to incrementally cut deeper into the material with each pass. It allows for deeper cuts than single station broaching.
Key Applications of Broaching T
Some common applications where broaching is employed include:
- Splines (external or internal) for transmission shafts
- Straight or angular keyways
- Flat or contoured surfaces on gears, pulleys or sprockets
- Internal or external splines on hydraulic components
- Flat, angular or contoured surfaces on aerospace components
- Pockets, shoulders and undercuts in dies, molds and fixtures
- Piston grooves and pump liners in automotive and industrial machinery
- Small, high precision bores or chambers in medical implants
Advantages and Limitations of Broaching T
Broaching offers many advantages over other machining processes:
Advantages:
- High production rates possible due to single pass operation
- Excellent accuracy and precision of +/- 0.00005" routinely achievable
- Results in a smooth surface comparable or better than grinding
- Dimensional stability under cyclic loads/operating conditions
- Economical for high volume production of duplicate components
Limitations:
- Suited only for linear or planar cuts, not complex curved contours
- Broach tooling is highly specialized and can be expensive to design/produce
- Significant oversizing of workpiece needed for material removal
- Heat generation during machining can distort precise workpieces
- Not suitable for low production volume due to setup and tooling costs
broaching is an efficient and economical machining process well-suited for high-volume production of linear or planar geometric features on a component. It delivers high precision, smooth finishes and dimensional control at a lower cost compared to other bulk material removal processes like milling or grinding. With the right application of broaching techniques and broach tool design, a variety of complex internal and external profiles can be cut accurately in a single pass.
Explore More Related Article On- Customer Relationship Management Market
For Deeper Insights, Find the Report in the Language that You want.
About Author:
Money Singh is a seasoned content writer with over four years of experience in the market research sector. Her expertise spans various industries, including food and beverages, biotechnology, chemical and materials, defense and aerospace, consumer goods, etc. (https://www.linkedin.com/in/money-singh-590844163)
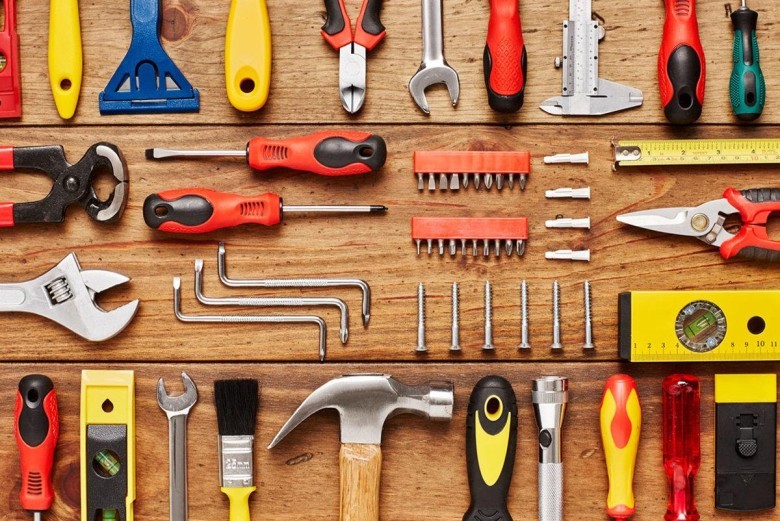
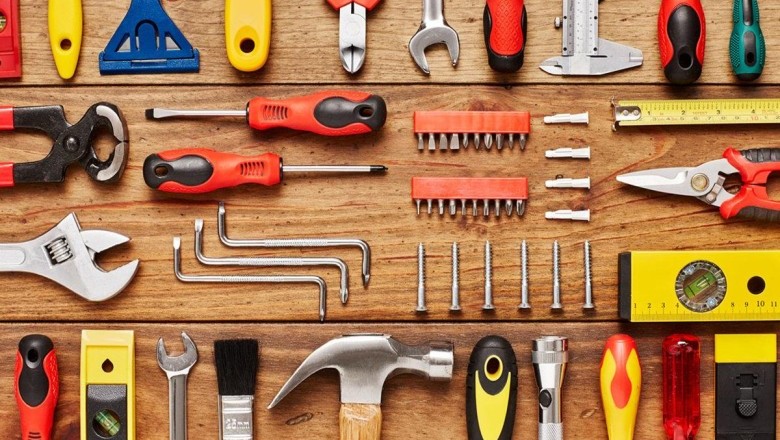

Comments
0 comment