The Taiwan Ceramic Machinery Market: A Hotbed for Innovation with Microwave Sintering on the Horizon
views
Taiwan Ceramic Machinery Market has established itself as a significant player in the global advanced ceramics market, driven by its robust electronics, semiconductor, automotive, aerospace, and medical industries. This demand fuels the dynamic market, which is constantly evolving to meet the increasingly sophisticated needs of ceramic manufacturers.
Key Drivers of the Taiwan Ceramic Machinery Market
Several factors contribute to the expansion of the Taiwan Ceramic Machinery Market:
- Booming Semiconductor Industry: Taiwan is a global leader in semiconductor manufacturing, accounting for a significant percentage of global production. Advanced ceramics are crucial in this sector for producing substrates, insulators, and protective materials that can withstand extreme conditions. This strong domestic demand directly translates to a higher need for specialized ceramic machinery.
- Growing Demand from Other Key Industries: The automotive sector, particularly the burgeoning electric vehicle (EV) market, requires advanced ceramics for batteries, sensors, and power electronics. Similarly, the aerospace and medical industries utilize high-performance ceramics for lightweight structural components and biocompatible implants, respectively.
- Urbanization and Infrastructure Development: Ongoing urbanization and infrastructure projects across the region increase the demand for traditional ceramics like tiles and sanitary ware, further driving the need for efficient ceramic manufacturing equipment.
- Technological Advancements: Continuous innovation in ceramic processing techniques necessitates advanced machinery capable of delivering higher precision, faster production speeds, and improved product quality. This includes the integration of automation and digital technologies into ceramic manufacturing processes.
- Government Support and Initiatives: While specific details of government initiatives directly targeting ceramic machinery manufacturers in Taiwan are less readily available, the overall support for advanced technology and manufacturing within Taiwan indirectly benefits this sector.
Market Trends Shaping the Future
The Taiwan Ceramic Machinery Market is witnessing several key trends:
- Increasing Automation: To enhance efficiency, reduce labor costs, and ensure consistent product quality, there is a growing adoption of automated ceramic machinery. This includes robotic systems for handling, shaping, and finishing ceramic products.
- Integration of Digital Technologies: Concepts like Industry 4.0 are influencing the market, with manufacturers increasingly looking for machinery with advanced sensors, data analytics capabilities, and remote monitoring for optimized production processes.
- Focus on Energy Efficiency and Sustainability: Environmental concerns are pushing the industry towards more energy-efficient machinery and processes, reducing waste and minimizing the environmental footprint of ceramic manufacturing.
- Demand for Customization and Flexibility: End-user industries often require ceramics with specific properties and complex designs. This drives the demand for machinery that offers greater flexibility and customization options.
- Adoption of Advanced Sintering Technologies: While traditional sintering methods remain prevalent, innovative techniques like microwave sintering are gaining traction for their potential to offer significant advantages.
Microwave Sintering Technology: A Paradigm Shift in Ceramic Processing
Microwave sintering technology represents a significant departure from conventional sintering methods that rely on radiant or convective heating. Instead of heating the furnace and then transferring heat to the ceramic material, microwave sintering utilizes electromagnetic energy to directly interact with the material at a molecular level. This results in volumetric heating, where heat is generated uniformly throughout the workpiece.
How Microwave Sintering Works
Microwaves, typically at frequencies of 2.45 GHz or higher, are introduced into a specially designed furnace cavity. The ceramic material, depending on its dielectric properties, absorbs this energy and converts it into heat. The efficiency of this heating depends on factors like the frequency of the microwaves, the dielectric constant and loss tangent of the material, and the strength of the electric field.
Advantages of Microwave Sintering in Ceramic Processing
Microwave sintering offers a compelling array of advantages over traditional sintering techniques:
- Faster Sintering Cycles: Volumetric heating leads to significantly faster heating rates and shorter holding times at the sintering temperature. This can dramatically reduce the overall processing time, leading to increased productivity. For instance, some ceramics that require hours for conventional sintering can be densified in minutes using microwave technology.
- Energy Efficiency: By directly heating the material, microwave sintering can be more energy-efficient as less energy is wasted in heating the furnace chamber itself. Studies have shown potential energy savings of up to 70% compared to conventional methods.
- Improved Microstructure and Properties: The uniform heating in microwave sintering can result in a more homogeneous microstructure with finer grain sizes and reduced porosity. This often translates to improved mechanical properties such as higher density, strength, and toughness.
- Lower Sintering Temperatures: In some cases, microwave sintering can achieve comparable densities at lower sintering temperatures compared to conventional methods. This can be particularly beneficial for materials that are prone to grain growth or decomposition at high temperatures.
- Enhanced Diffusion Kinetics: The interaction of microwaves with the material can enhance diffusion processes at the atomic level, potentially leading to faster densification and improved bonding between particles.
- Flexibility in Operation: Microwave furnaces offer flexibility in terms of the sintering atmosphere and the ability to process different materials in alternating runs without significant changes to the furnace setup.
- Near-Net-Shape Processing: The rapid and uniform heating can minimize dimensional changes and warping during sintering, facilitating near-net-shape processing and reducing the need for extensive post-processing.
Applications of Microwave Sintering in Ceramics
Microwave sintering is finding increasing applications across a wide range of ceramic materials and products:
- Advanced Ceramics: Sintering of alumina, zirconia, silicon carbide, and other advanced ceramics for structural, electronic, and thermal applications. Microwave sintering has shown promise in producing transparent alumina with high density and improved optical properties.
- Bioceramics: Processing of hydroxyapatite and other bioceramics for medical implants and tissue engineering. Microwave sintering can lead to enhanced mechanical properties and biocompatibility.
- Electronic Ceramics: Sintering of dielectric ceramics for capacitors, substrates, and other electronic components. Microwave sintering can improve the dielectric properties and reduce sintering temperatures for these materials.
- Refractory Materials: Microwave sintering is being explored for the production of large-volume ceramic refractories used in industrial furnaces, offering the potential for more homogeneous sintering and improved performance.
- Nanomaterials: Consolidation of ceramic nanopowders to achieve dense nanostructured ceramics with unique properties. Microwave sintering can help control grain growth and maintain the nanoscale features.
- Solid Oxide Fuel Cell (SOFC) Components: Fabrication of electrodes and electrolytes for SOFCs using microwave sintering, potentially leading to improved performance and reduced processing costs.
- Ferrites: Manufacturing of ultra-thin ferrite sheets for electronic applications using microwave sintering, offering precise control over the microstructure.
Challenges and Future Outlook for Microwave Sintering
Despite its numerous advantages, microwave sintering also faces certain challenges:
- Material Dependence: The effectiveness of microwave sintering is highly dependent on the dielectric properties of the material, which can vary with temperature and frequency. Some materials are poor absorbers of microwave energy and may not heat efficiently.
- Heating Uniformity: Achieving uniform heating in large or complex-shaped parts can be challenging due to variations in microwave field distribution within the furnace cavity. Multi-mode and single-mode microwave furnaces are designed to address this issue.
- Scale-Up and Cost: Scaling up microwave sintering from laboratory to industrial production can present engineering challenges and may involve significant capital investment.
- Process Optimization: Developing optimized sintering protocols for different ceramic materials and applications requires careful control of microwave power, frequency, temperature profiles, and furnace atmosphere.
Despite these challenges, the future of microwave sintering in ceramic processing looks promising. Ongoing research and development are focused on addressing the limitations and expanding the range of materials and applications that can benefit from this technology. Innovations in furnace design, microwave power sources, and process control are paving the way for wider industrial adoption.
The Potential Impact on the Taiwan Ceramic Machinery Market
As the demand for high-performance ceramics continues to grow, and as microwave sintering technology matures, we can expect to see an increasing interest and adoption of this technology within the Taiwan Ceramic Machinery Market. Taiwanese manufacturers, known for their technological prowess and adaptability, are likely to explore and integrate microwave sintering capabilities into their offerings.
This could lead to:
- Development of new types of ceramic machinery: Taiwanese companies may start designing and manufacturing specialized microwave sintering furnaces tailored to the needs of various ceramic industries.
- Integration of microwave sintering into existing production lines: Current ceramic machinery manufacturers might incorporate microwave sintering modules into their integrated production systems.
- Collaborations and partnerships: Taiwanese companies may collaborate with international experts and technology providers to accelerate the adoption and advancement of microwave sintering technology.
- Competitive advantage: Early adoption of microwave sintering could provide Taiwanese ceramic manufacturers with a competitive edge in terms of production speed, energy efficiency, and the quality of their advanced ceramic products.
In conclusion, the Taiwan Ceramic Machinery Market is poised for continued growth, driven by the strong demand for advanced ceramics across key industries. Microwave sintering technology, with its potential for faster, more efficient, and higher-quality ceramic processing, represents a significant innovation that could play an increasingly important role in shaping the future of this dynamic market.
As research and development continue to overcome current challenges, the integration of microwave sintering into Taiwan's ceramic manufacturing landscape could unlock new possibilities and further strengthen its position in the global advanced ceramics arena.
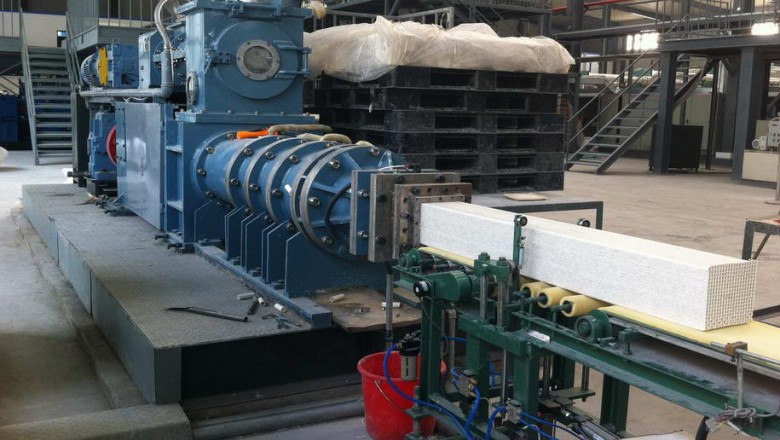

Comments
0 comment