views
The Metal Pail Market is highly influenced by various external factors, with raw material costs being one of the most significant determinants. The price of metals, including steel and aluminum, which are the primary raw materials for manufacturing metal pails, can fluctuate due to various global economic, political, and supply chain factors. These fluctuations directly impact production costs, supply chains, and market dynamics, influencing the final pricing and availability of metal pails.
In this blog, we will analyze the effect of raw material price fluctuations on the Metal Pail Market, focusing on how these changes affect manufacturers and consumers and how businesses can adapt to this volatility.
Impact of Raw Material Price Fluctuations on Production
Raw materials are the backbone of the manufacturing process for metal pails, and any fluctuation in their prices can significantly influence the production costs and overall profitability of manufacturers. The two most commonly used materials in the production of metal pails are steel and aluminum, both of which are subject to market volatility.
1. Steel Prices and Their Influence on Metal Pail Production Costs
Steel is one of the most widely used materials in metal pail manufacturing due to its durability and strength. The price of steel is affected by a variety of factors, including:
-
Supply Chain Disruptions: Events such as natural disasters, strikes, or political instability in key steel-producing regions can lead to sudden increases in steel prices.
-
Demand and Global Consumption: Steel prices tend to rise when demand increases in industries such as construction, automotive, and manufacturing, all of which are major consumers of steel.
-
Energy Costs: Steel production is an energy-intensive process. Rising energy costs, particularly in regions that depend on coal or gas for manufacturing, can cause steel prices to rise, directly affecting the cost of metal pails.
When steel prices rise, metal pail manufacturers face higher production costs, which can lead to increased prices for consumers. This, in turn, may impact demand, as customers may seek more affordable alternatives.
2. Aluminum Price Fluctuations and Their Impact on Manufacturing
Aluminum is another key material used in metal pail production, especially for lightweight and corrosion-resistant pails. Similar to steel, aluminum prices are influenced by several factors:
-
Global Aluminum Supply and Demand: The global aluminum market is often affected by supply-demand imbalances. In recent years, there has been a push toward more sustainable practices, with growing demand for recycled aluminum, which can sometimes create supply shortages.
-
China’s Role in the Global Market: China is the world’s largest producer and consumer of aluminum. Any changes in production levels, trade policies, or tariffs in China can have significant repercussions on global aluminum prices.
-
Environmental Policies: The introduction of stricter environmental regulations in key aluminum-producing countries can increase the costs of production, leading to higher aluminum prices. These regulations often require manufacturers to adopt cleaner production technologies, which can increase operational costs.
As with steel, fluctuations in aluminum prices can cause significant changes in the production costs of metal pails. Manufacturers often have to pass these additional costs on to consumers, which can reduce demand or force businesses to adjust their pricing strategies.
How Manufacturers Adapt to Raw Material Price Volatility
Manufacturers of metal pails must be able to navigate the challenges posed by raw material price fluctuations. Many companies adopt strategies to mitigate these effects and maintain profitability.
1. Hedging and Long-Term Contracts
One common strategy employed by manufacturers to protect themselves from volatile raw material prices is hedging. By entering into long-term contracts with suppliers, manufacturers can lock in prices for steel and aluminum, thus providing greater price stability over time. These contracts help shield businesses from sudden price hikes in the raw materials market.
-
Hedging Strategies: Hedging through financial instruments, such as futures contracts, allows manufacturers to lock in prices for raw materials in advance. While this may not eliminate all risks associated with price fluctuations, it can provide a buffer against severe market volatility.
2. Efficient Supply Chain Management
A more efficient and diversified supply chain can help manufacturers better absorb price fluctuations. By sourcing materials from multiple suppliers and regions, companies can reduce the risk of being overly dependent on one source, which may be more vulnerable to price hikes due to local economic conditions or geopolitical events.
-
Diversification of Suppliers: Relying on a mix of local and international suppliers can help mitigate risks associated with supply chain disruptions. In addition, manufacturers can explore alternative raw material suppliers that may offer more competitive pricing or more favorable payment terms.
3. Investing in Technology and Automation
Investing in technology and automation can help manufacturers reduce their overall production costs, making it easier to absorb price fluctuations in raw materials. By improving production efficiency, manufacturers can offset the impact of higher material costs and maintain competitive pricing.
-
Automation for Cost Reduction: Automation technologies in manufacturing can significantly reduce labor costs, optimize production processes, and increase output efficiency. This can help offset rising raw material costs and keep the final prices of metal pails more stable.
4. Product Innovation and Design Changes
Another strategy employed by manufacturers is innovating in product design to reduce material consumption. For example, designing lighter or smaller metal pails can help lower material costs, even when raw material prices are rising.
-
Material Substitution: In some cases, manufacturers may also explore alternative materials that are less expensive but still offer similar durability and functionality. This can help maintain product quality while mitigating the impact of raw material price fluctuations.
Consumer Implications: Pricing and Availability
While manufacturers may be able to implement strategies to minimize the effects of raw material price fluctuations, the impact on consumers is inevitable. Price hikes in raw materials like steel and aluminum often lead to increased production costs, which can translate to higher prices for metal pails. This has several implications:
1. Increased Packaging Costs for Industries
For industries that rely heavily on metal pails, such as food, chemicals, and pharmaceuticals, rising packaging costs can affect overall operational expenses. Companies may have to pass these costs on to consumers, leading to higher prices for end products. This could influence market dynamics, as companies seek to balance cost increases with customer demand for affordable products.
2. Supply Chain Disruptions
Raw material price fluctuations often lead to supply chain disruptions, particularly in times of significant price volatility. Manufacturers may struggle to maintain inventory levels or meet production deadlines, leading to delays in product availability. This can affect industries that depend on timely delivery of packaging materials, such as those in the food and beverage industry.
3. Alternative Packaging Options
As metal pail prices rise, some businesses may look for alternative packaging solutions, including plastic or composite containers. While metal pails offer certain advantages in terms of durability and recyclability, price-sensitive industries may be forced to consider alternatives if metal pail prices continue to increase.
Conclusion: Navigating Raw Material Price Volatility
The Metal Pail Market faces significant challenges related to raw material price fluctuations. Steel and aluminum prices, influenced by a range of global factors, directly impact the production costs of metal pails. Manufacturers must adapt by employing strategies such as hedging, supply chain diversification, and investing in technology to mitigate these price fluctuations. At the same time, consumers and industries that rely on metal pails must be prepared for potential price increases and supply chain disruptions.
As the global market continues to evolve, the Metal Pail Market will need to remain agile in response to raw material price fluctuations while continuing to meet the demand for durable, eco-friendly packaging solutions.
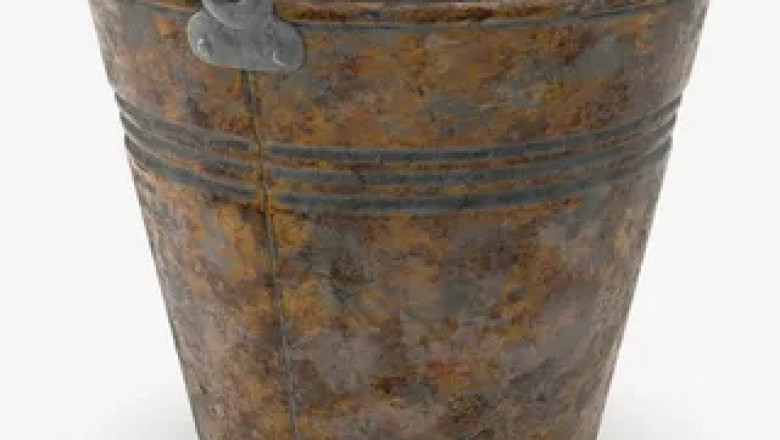

Comments
0 comment