views
Introduction:
The Europe Ceramic Machinery Market is undergoing a technological transformation driven by Industry 4.0, which integrates digitalization, IoT, and predictive maintenance to enhance efficiency, reduce downtime, and optimize production. As the demand for high-quality ceramic products grows, manufacturers are investing in smart factories that leverage cutting-edge technologies to improve productivity and sustainability.
The Impact of Industry 4.0 on the European Ceramic Sector
Industry 4.0 represents the fourth industrial revolution, characterized by the adoption of automation, artificial intelligence (AI), and interconnected systems in manufacturing. In the ceramic sector, these technologies are reshaping traditional processes, making them more intelligent, flexible, and efficient.
Key Technologies Driving Industry 4.0 in Ceramic Manufacturing
-
Digitalization – The integration of smart software and cloud-based systems to manage and optimize production.
-
Internet of Things (IoT) – Smart sensors and connected devices that enable real-time monitoring of machinery and processes.
-
Predictive Maintenance – AI-driven analytics that detect potential equipment failures before they occur, reducing downtime and costs.
-
Automation and Robotics – Use of robotic arms and automated machinery to enhance precision and speed in ceramic production.
-
Big Data and AI Analytics – Real-time data analysis for improved decision-making and process optimization.
How Digitalization is Transforming Ceramic Manufacturing
1. Smart Production Lines and Process Optimization
Modern ceramic factories are implementing fully digitalized production lines equipped with AI-powered software to monitor and control every stage of manufacturing. From raw material processing to kiln firing and glazing, digital systems ensure consistent quality, minimal waste, and higher productivity.
-
Example: Advanced software solutions analyze kiln temperature fluctuations and adjust parameters automatically to optimize firing efficiency.
-
Impact: Reduces energy consumption, ensures uniform product quality, and minimizes defects.
2. Cloud-Based Monitoring and Remote Operations
Cloud computing enables remote monitoring and control of ceramic production facilities. Factory managers can access real-time data from any location, allowing them to:
-
Detect inefficiencies in production.
-
Make real-time adjustments.
-
Improve collaboration across multiple manufacturing sites.
The Role of IoT in the European Ceramic Industry
1. Smart Sensors for Real-Time Monitoring
IoT-powered smart sensors are being embedded in ceramic machinery to monitor:
-
Temperature and humidity levels in kilns.
-
Pressure and flow rates in material processing systems.
-
Wear and tear of machine components.
2. Enhanced Quality Control and Defect Detection
IoT-enabled cameras and AI-driven vision systems are revolutionizing quality control by:
-
Detecting surface imperfections and micro-cracks in ceramic products.
-
Analyzing color consistency and glaze application.
-
Providing real-time feedback to adjust production parameters instantly.
3. Energy Efficiency and Sustainability
With increasing environmental regulations, IoT is playing a crucial role in energy conservation:
-
Smart IoT systems monitor energy consumption and suggest efficiency improvements.
-
Sensors optimize kiln firing schedules, reducing fuel usage and CO₂ emissions.
-
Automated lighting and HVAC systems adjust based on occupancy and production needs.
Predictive Maintenance: Reducing Downtime and Enhancing Productivity
One of the biggest challenges in ceramic manufacturing is machine breakdowns, leading to costly production halts. Predictive maintenance powered by AI and IoT is addressing this issue.
1. AI-Powered Machine Learning for Maintenance Predictions
AI-driven algorithms analyze vast amounts of data collected from machinery sensors to:
-
Predict when a machine component is likely to fail.
-
Schedule maintenance only when necessary, avoiding unnecessary servicing.
-
Reduce unplanned downtime and prevent costly repairs.
2. Digital Twin Technology for Virtual Equipment Monitoring
A digital twin is a virtual replica of a physical machine, allowing manufacturers to:
-
Simulate different operating conditions before implementing changes in the real world.
-
Identify inefficiencies and potential failures before they impact production.
-
Improve production planning by analyzing historical data and trends.
Automation and Robotics in Smart Ceramic Factories
1. Robotic Arms for Precision Manufacturing
Automation is streamlining ceramic production with robotic arms capable of handling tasks such as:
-
Material handling and shaping – Reducing human labor and ensuring uniformity.
-
Automated glazing and decorating – Applying intricate patterns with high precision.
-
Stacking and packaging – Speeding up warehouse operations and logistics.
2. AI-Driven Decision-Making for Process Control
Machine learning models analyze real-time production data to:
-
Optimize glaze thickness and material composition for durability.
-
Adjust kiln settings to minimize thermal stress on ceramic products.
-
Reduce material wastage and improve sustainability.
The Role of Big Data and AI in Smart Ceramic Factories
1. Data-Driven Insights for Process Improvement
By collecting and analyzing big data, manufacturers can:
-
Identify patterns and inefficiencies in ceramic production.
-
Develop predictive models for demand forecasting.
-
Optimize raw material procurement, reducing costs and waste.
2. AI-Enabled Supply Chain Management
AI is improving the ceramic supply chain by:
-
Predicting demand fluctuations and adjusting production accordingly.
-
Optimizing inventory levels, reducing overproduction and storage costs.
-
Enhancing supplier collaboration, ensuring timely raw material delivery.
Case Study: CeramTec GmbH’s Smart Factory Initiatives
CeramTec GmbH, one of Europe’s leading ceramic manufacturers, is embracing Industry 4.0 with:
-
AI-powered quality control systems for defect detection.
-
IoT-enabled energy-efficient kilns to reduce environmental impact.
-
Automated robotic arms for precision shaping and glazing.
-
Big data analytics for predictive maintenance and supply chain optimization.
Challenges and Future Opportunities in Smart Ceramic Factories
Challenges
-
High Initial Investment – Upgrading to smart factories requires significant capital.
-
Complex Integration – Merging legacy systems with digital infrastructure is challenging.
-
Cybersecurity Risks – Increased connectivity exposes manufacturers to potential cyber threats.
Opportunities
-
Enhanced Productivity – Automated systems improve efficiency and reduce labor costs.
-
Sustainability Gains – Smart technologies help manufacturers meet environmental regulations.
-
Competitive Advantage – Early adopters of Industry 4.0 will lead the European ceramic market.
The Future of Industry 4.0 in European Ceramic Manufacturing
The European ceramic machinery market is embracing Industry 4.0 to stay competitive in a rapidly evolving industry. Future developments will include:
-
Increased AI Integration – AI will take on more decision-making roles in production optimization.
-
5G Connectivity in Factories – Faster data transmission for real-time process adjustments.
-
Expansion of Digital Twins – More companies will use virtual simulations to improve efficiency.
Conclusion
The future of ceramic manufacturing in Europe is being shaped by Industry 4.0, with digitalization, IoT, and predictive maintenance revolutionizing production processes. Smart factories are enhancing efficiency, reducing waste, and ensuring sustainability, positioning European manufacturers at the forefront of global ceramic innovation. Companies like CeramTec GmbH are leading the charge, showcasing how advanced technologies can create a smarter, greener, and more competitive ceramic industry.
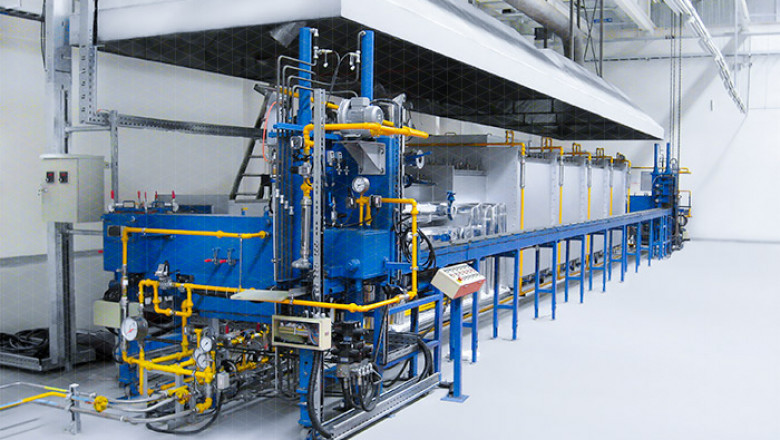

Comments
0 comment