views
The Evolution of Vacuum Material Handling Equipment in Modern Manufacturing
As manufacturing processes have become more sophisticated, the demand for efficient, safe, and automated material handling solutions has surged. One area that has seen significant advancement over the years is vacuum material handling equipment. From simple lifting aids to complex, integrated automation systems, vacuum technology has transformed how materials are moved, positioned, and handled across various industries.
This article explores the evolution of vacuum material handling equipment, its growing role in modern manufacturing, and the technological advancements that continue to shape its development.
What Is Vacuum Material Handling Equipment?
Vacuum material handling equipment is a system that uses suction generated by a vacuum to lift, move, and position various materials, including glass, metal sheets, plastic, wood, and even porous items like cardboard or bags. These systems typically consist of a vacuum generator, suction pads or cups, and a control unit. They may be manual, semi-automated, or fully integrated into robotic systems.
Unlike mechanical handling systems, vacuum equipment offers a non-damaging and highly adaptable solution that reduces worker strain, enhances efficiency, and improves product safety.
Early Use of Vacuum Handling
The early versions of vacuum material handling equipment were basic and primarily used for lifting flat, smooth materials such as glass and sheet metal. These systems relied on compressed air or simple electric vacuum pumps to generate suction. Though relatively limited in application, they provided a safer alternative to manual lifting in industries where delicate or heavy components required careful handling.
Initial designs were often bulky and not easily portable, restricting their use to stationary setups. Still, they represented a significant improvement in workplace ergonomics and material handling safety.
Expansion into Diverse Industries
As industries diversified, so did the need for more adaptable vacuum systems. By the late 20th century, vacuum material handling equipment had expanded beyond the glass and metal industries and found its place in:
-
Food processing (for lifting packaged goods and ingredients)
-
Pharmaceuticals (for handling cleanroom-grade components)
-
Warehousing and logistics (for cartons, sacks, and irregular shapes)
-
Electronics manufacturing (for delicate circuit boards and assemblies)
These broader applications prompted manufacturers to improve vacuum system efficiency, develop better sealing technologies, and design modular configurations to meet different operational needs.
Technological Advancements in the 21st Century
With the onset of Industry 4.0 and increasing automation in manufacturing, vacuum material handling equipment underwent a technological transformation. Several key innovations have propelled the industry forward:
1. Integration with Automation and Robotics
Modern systems are now frequently integrated with robotic arms and automated guided vehicles (AGVs), allowing for seamless material transfer in production lines. Programmable vacuum units enable precise and repeatable motion, reducing error rates and labor costs.
2. Smarter Control Systems
Advances in sensors and control software have given vacuum handling equipment real-time responsiveness. Load sensors, safety interlocks, and intelligent vacuum regulation ensure optimal performance and operational safety.
3. Improved Energy Efficiency
Old vacuum systems often relied on constant high power, leading to energy waste. Newer models use energy-on-demand technology that activates suction only when needed, significantly reducing power consumption.
4. Adaptability to Complex Materials
Innovations in suction cup design and material science now allow vacuum systems to handle textured, curved, and even porous surfaces. This has opened the door to using vacuum material handling equipment in packaging, textiles, and construction industries.
Benefits Driving Adoption in Modern Manufacturing
Manufacturers continue to invest in vacuum material handling equipment for several key reasons:
-
Increased productivity – Automated vacuum systems can handle repetitive tasks faster than manual labor.
-
Improved workplace safety – Reduces the risk of injury from lifting heavy or awkward loads.
-
Product quality protection – Minimizes damage to sensitive or fragile materials during handling.
-
Labor cost reduction – Reduces the number of personnel required for material transport.
-
Compliance with ergonomic standards – Helps manufacturers meet occupational health regulations.
These advantages align with the goals of modern manufacturing—efficiency, safety, and quality—all of which are essential for competitiveness in a global market.
Sustainable and Green Manufacturing
Another factor driving the evolution of vacuum material handling equipment is the shift toward sustainable manufacturing. Electric and pneumatic vacuum systems with low energy usage contribute to greener factory operations. Furthermore, their ability to handle recyclable and delicate materials without damage reduces waste and supports lean manufacturing practices.
Manufacturers are also designing equipment with recyclable components and longer service lives, further enhancing sustainability.
The Future of Vacuum Material Handling Equipment
As manufacturing continues to advance, so too will the capabilities of vacuum material handling equipment. Some emerging trends to watch include:
-
AI and machine learning integration for predictive maintenance and process optimization
-
Collaborative robot (cobot) compatibility to support human-machine interaction
-
Wireless control systems for remote and mobile operations
-
Customizable, 3D-printed vacuum pads for industry-specific tasks
-
Augmented reality (AR) tools to assist in equipment maintenance and training
These developments aim to make vacuum material handling not only more powerful but also more intuitive and accessible to a wider range of industries.
Conclusion
The evolution of vacuum material handling equipment reflects the broader transformation of manufacturing from labor-intensive processes to intelligent, automated, and efficient systems. What began as a niche solution for flat, fragile materials has grown into an indispensable part of factories, warehouses, and logistics centers around the world.
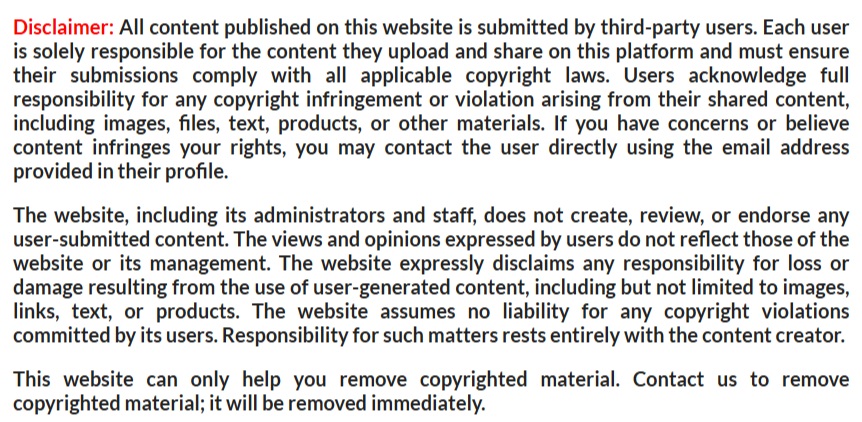