views
The Polyethylene Wax Market can be better understood through a segmentation lens that highlights how various industries utilize different product types.
Introduction: Importance of Market Segmentation
Polyethylene wax (PE wax) is a performance additive with diverse applications across coatings, plastics, rubber, adhesives, and textiles. Given its versatility, understanding the market requires a segmented approach based on product types and end-use industries.
Segmentation not only helps identify high-growth areas but also reveals emerging demands and opportunities for targeted innovation. This blog explores the two primary segmentation criteria—by product type and by end-use industry—that are shaping the global PE wax market.
Segment 1: Product Type Segmentation
PE wax products are classified based on molecular structure, production method, and end-functionality. The major product segments include:
1. High-Density Polyethylene (HDPE) Wax:
Characterized by a higher melting point and hardness, HDPE wax is ideal for tough industrial conditions. It’s used in high-temperature plastic processing and abrasive-resistant coatings.
2. Low-Density Polyethylene (LDPE) Wax:
LDPE wax offers greater flexibility and lower melting points. It’s commonly used in emulsions, adhesives, and low-friction coatings. Its softer structure makes it suitable for textile treatments and wood finishes.
3. Oxidized Polyethylene Wax:
Oxidation enhances emulsification, dispersibility, and adhesion. These waxes are widely used in printing inks, coatings, and polishes. They also act as lubricants in PVC processing and exhibit strong compatibility with polar compounds.
4. Micronized Polyethylene Wax:
Micronized variants are finely ground to improve dispersion in liquid systems. These are preferred in inks, coatings, and paints where smooth surface finish and durability are crucial.
5. Fischer-Tropsch (FT) Wax:
Though not chemically identical to conventional PE wax, FT waxes offer extremely high purity and narrow molecular weight distribution. They are used in specialty packaging, hot-melt adhesives, and food-grade coatings.
Each type serves distinct industrial needs, and product selection often depends on the application’s temperature range, surface requirements, and processing methods.
Segment 2: End-Use Industry Segmentation
Polyethylene wax finds applications in a wide range of industries, each with its unique requirements:
1. Plastics Industry:
This segment dominates overall consumption. PE wax acts as a lubricant and dispersing agent, improving processing efficiency, extrusion flow, and surface quality in PVC, PE, and polypropylene products.
2. Packaging Industry:
The packaging sector uses PE wax in films, laminates, and hot-melt adhesives. It ensures seal integrity, enhances printability, and improves resistance to abrasion and moisture.
3. Printing Inks and Coatings:
In this segment, PE waxes improve slip, gloss, and scratch resistance. Micronized and oxidized variants are especially popular in offset and flexographic inks.
4. Rubber and Tire Industry:
PE wax reduces mold sticking, enhances flow, and provides anti-blocking properties during rubber processing. It improves uniformity in products like hoses, seals, and tires.
5. Adhesives and Sealants:
Hot-melt adhesives benefit from PE wax’s ability to adjust viscosity, increase flexibility, and improve adhesion properties—vital in packaging, construction, and woodworking.
6. Textiles:
PE wax provides lubrication, softening, and water repellency in textile processing. It’s used in thread conditioning and fabric finishing.
7. Polishes and Lubricants:
In surface polishes, PE wax adds shine, durability, and slip resistance. In industrial lubricants, it serves as a thickener and friction reducer.
8. Others:
Emerging segments include cosmetics, electronics, and pharmaceuticals. These industries demand ultra-pure and functionalized waxes for specialized applications.
Regional Preferences in Segments
Segmentation also varies across regions based on industrial maturity and market needs:
-
North America & Europe: Higher use of oxidized and micronized waxes for advanced coatings, adhesives, and industrial applications. Sustainability drives demand for bio-based alternatives.
-
Asia-Pacific: Dominated by packaging, plastic, and textile industries. LDPE and HDPE waxes are in high demand due to growing domestic manufacturing.
-
Latin America & Middle East: Expanding packaging and construction industries are leading to greater adoption of PE waxes, especially for adhesives and plastic applications.
Understanding these regional preferences enables producers to tailor supply and marketing strategies more effectively.
Strategic Insights for Stakeholders
A segmentation-focused approach offers several strategic benefits:
-
Product Developers: Can create specialized waxes for high-demand segments like automotive coatings or bio-based packaging.
-
Marketers: Gain insights into which industries and regions need more education or product sampling.
-
Investors: Identify high-growth verticals like adhesives or printing inks for targeted capital deployment.
-
Distributors: Can focus logistics and inventory efforts on the most in-demand wax types.
Conclusion: Segmentation Reveals the Bigger Picture
The segmentation of the polyethylene wax market by product type and end-use industry provides a clearer understanding of where growth is occurring and why. As industries continue to diversify and demand specialized performance, segment-based insights will be key to staying competitive in the global PE wax market.
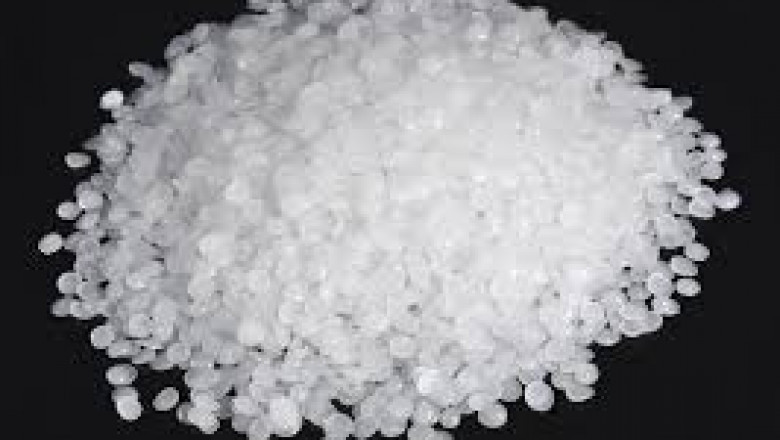
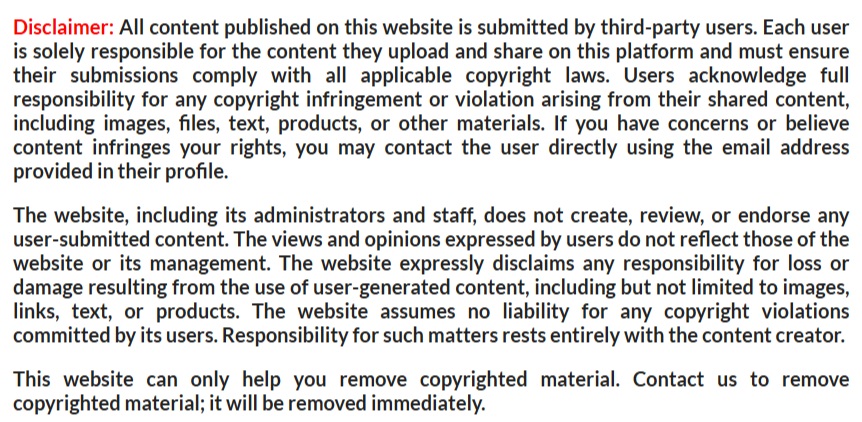
Comments
0 comment