views
Papermaking is a complex and dynamic process with many possibilities of adjustments and influences in a complex production plant. By high level automation and production monitoring it is possible to increase the efficiency of the process. Starting the papermaking in the wet end area, the monitoring of the charge environment (particle charge and zeta potential) is extremely important.
Unclear charge conditions can lead to losses in product quality, disturbances in the production process and higher consumption of additives. A permanent control is especially important if different chemical additives are used, which are supposed to ensure a well-functioning production process and certain quality requirements of the base paper and finished product. Having information about the charge conditions available helps to optimize the dosage of additives throughout the complete wet-end process and allows the mill technicians and engineers to get a good overview of the status.
Test devices, which provide this necessary information, are for example the CAS touch! Charge Analyzing System and the FPA touch! Fiber Potential Analyzer. These devices are used in the lab and their application is an old hat for papermakers. Beside the used proven methods, both devices offer features for an effective, user-friendly and intuitive handling. Especially chemical suppliers appreciate their small size and light weight for convenient transportation. They are ready for immediate use after unpacking, as no additional components need to be assembled.
However, as the automation and digitalization play an increasing role in the paper industry, as in most other industries too, automatic measurements, which provide reliable and accurate real-time data of the process, get more and more important to meet sustainable, ecological and resource-efficient requirements. Such online measurements have several advantages at the same time: it is not necessary to get samples from the machine and measure them, the results are available in real-time, which allows an immediate intervention in the process, if the process is not running well or quality issues occur. These real-time data cannot only be transferred to the process control system; they can also be transferred to any data cloud anywhere in the world, which enables networked handling of issues by experts, who do not necessarily have to be onsite.
Click for full Information: https://www.pulpandpaper-technology.com/articles/online-zeta-potential-measurement-in-the-wet-end-process
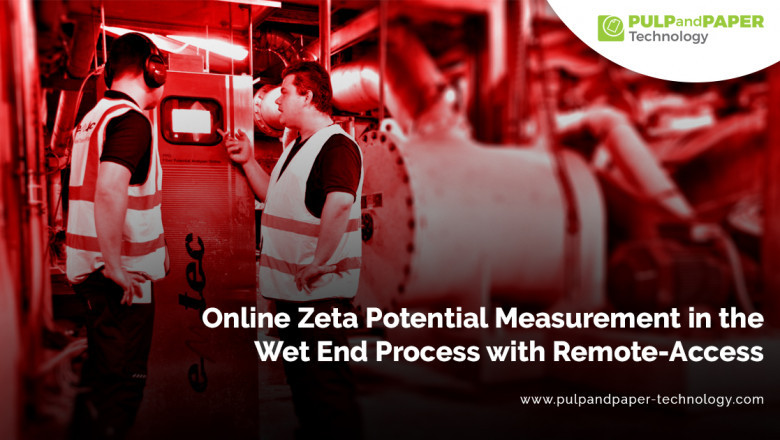
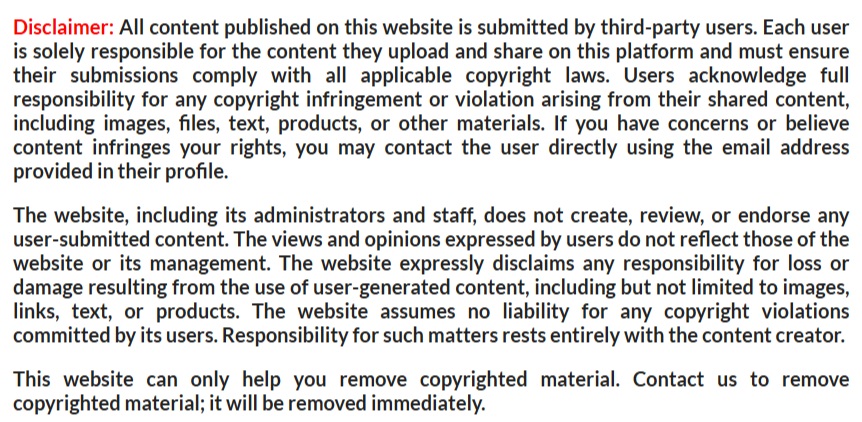
Comments
0 comment