views
The offshore oil & gas welding market is entering a transformative decade, fueled by rising global energy demands, surging infrastructure investments, and groundbreaking advancements in robotic welding technologies. According to recent analysis, the global market was valued at US$ 3.3 billion in 2023 and is projected to grow at a CAGR of 5.9% from 2024 to 2034, reaching approximately US$ 6.1 billion by the end of the forecast period.
Market Drivers: Energy Security & Technological Adoption
1. Surge in Oil & Gas Infrastructure Investment
As nations prioritize energy security amid fluctuating global dynamics, investment in oil & gas infrastructure is accelerating. According to Our World in Data, global primary energy consumption rose from 122,000 TWh in 2000 to 173,000 TWh in 2019 — a testament to the world’s growing energy appetite.
In February 2024, India-based Vedanta announced a US$ 4 billion investment to double oil & gas production capacity. Such large-scale investments are propelling demand for reliable, high-performance offshore welding solutions to support infrastructure development, particularly in deepwater and harsh environments.
2. Rise of Robotic Welding Solutions
The demand for precision, safety, and speed in offshore welding has ushered in a new era of robotic welding systems. These solutions, often powered by laser vision sensing, enhance weld quality and operational safety in difficult-to-access or hazardous offshore environments.
Robots enable continuous operations between multiple workstations, increasing efficiency and minimizing downtime. Additionally, AI-enabled robotic systems are now capable of detecting welding parameters like temperature, pressure, and seam alignment in real-time, ensuring consistency in demanding subsea tasks.
One notable development is the MR4WELD mobile robotic solution developed by Comau and Fincantieri, introduced in 2023. This mobile unit is designed to perform precision welding during vessel construction and can be adapted for broader offshore applications.
Welding Technologies Driving Offshore Efficiency
Offshore welding is not a one-size-fits-all approach. It incorporates a range of technologies depending on application, material, and location.
- Arc Welding and Resistance Welding are widely used in rig construction and maintenance.
- Laser Welding is gaining ground for its speed and precision, especially in automated environments.
- Flux-Cored Arc Welding (FCAW) and Submerged Arc Welding (SAW) are becoming popular due to their deep penetration, stability, and minimal fume emissions.
FCAW, for instance, offers high deposition rates and works efficiently with CO₂ shielding, which is cost-effective and supports deep welds. SAW, on the other hand, ensures clean welds with minimal arc exposure — ideal for long-duration subsea projects.
Regional Outlook: North America Leads
According to 2023 data, North America dominates the offshore oil & gas welding market, thanks to its expansive oil & gas production infrastructure.
The U.S. is a global powerhouse with over 500,000 active wells and is one of the top three petroleum producers. In 2022 alone, U.S. dry natural gas production reached 36.35 trillion cubic feet, setting a new annual record.
This surge in output requires ongoing maintenance and construction of offshore rigs, pipelines, and processing platforms — each of which relies heavily on welding operations. Consequently, the region’s demand for advanced welding technologies, particularly robotic and underwater solutions, is expected to rise steadily.
Competitive Landscape: Innovation Takes Center Stage
Leading market players are focusing on durability, cost-efficiency, and automation to gain a competitive edge. Companies such as ESAB, Lincoln Electric, Miller Electric, Fronius International GmbH, and Hypertherm Inc. are introducing innovative consumables and automated systems tailored to offshore needs.
For example, in February 2024, Alleima launched SAF 3007, a next-gen super-duplex stainless steel alloy engineered for subsea umbilicals. This alloy offers superior corrosion resistance and strength, outperforming existing solutions like SAF 2507 — an essential innovation for deepwater welding applications.
Similarly, Express Engineering invested in precision welding technology to boost its subsea capabilities, demonstrating how companies are aligning with industry demands for high-performance, corrosion-resistant welding in extreme environments.
Final Thoughts
The offshore oil & gas welding market is poised for robust growth as the world leans into energy security, infrastructure modernization, and automation. From robotic arms to AI-powered sensors and cutting-edge alloys, the fusion of technology and energy is reshaping how offshore welding is approached.
As energy demands rise and offshore projects become more complex, the welding industry must continue to innovate — ensuring safer, faster, and more sustainable solutions. For stakeholders across the value chain, the next decade represents not just a growth opportunity, but a chance to lead a new era of industrial excellence.
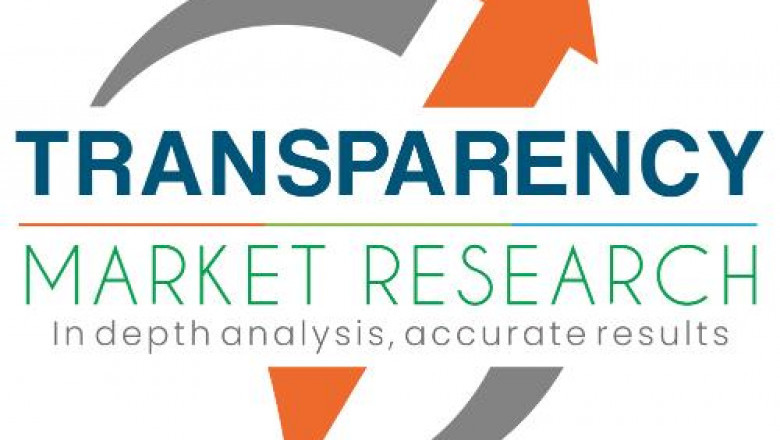

Comments
0 comment