views
In today’s fast-paced world, a single power glitch can bring production to a halt. For industries like textile machinery manufacturing, OEMs, utility providers, and exporters of electrical components, outdated power infrastructure isn’t just inconvenient—it’s costly.
To stay competitive, you need a system that’s not only reliable today but ready for tomorrow’s load. That’s what futureproofing is all about.
1. Know Your Load Limits
Many plants run close to capacity without realizing it. Regular audits show where your system is strained and which components need replacing or reinforcing.
2. Modernize What Matters
Focus on practical upgrades—transformers, stabilizers, switchgear, and power factor panels. These are the heart of your power flow and pay for themselves through better efficiency.
3. Prepare for Expansion
Adding machinery or extending operations? Design your power system to handle a bigger load from the start. This avoids expensive rewiring or panel upgrades later.
4. Protect Against Downtime
Blackouts and voltage drops cost more than equipment—they cost trust and timelines. Smart stabilizers, auto-changeover systems, and strong transformers keep your operation running even when the grid stumbles.
5. Choose a Partner Who Knows Your Industry
Not every vendor gets the needs of a textile plant or an OEM. You need a partner that designs for your specific loads, layout, and goals—not just sells off-the-shelf solutions.
You don’t need to overhaul your entire setup. Small, smart steps—done right—can help you build a stronger, more efficient system that’s ready for what comes next.
Many forward-looking companies in power distribution, manufacturing, and exports are already taking these steps—with help from specialists in industrial power solutions like
👉 Jindal Electric & Machinery Corporation
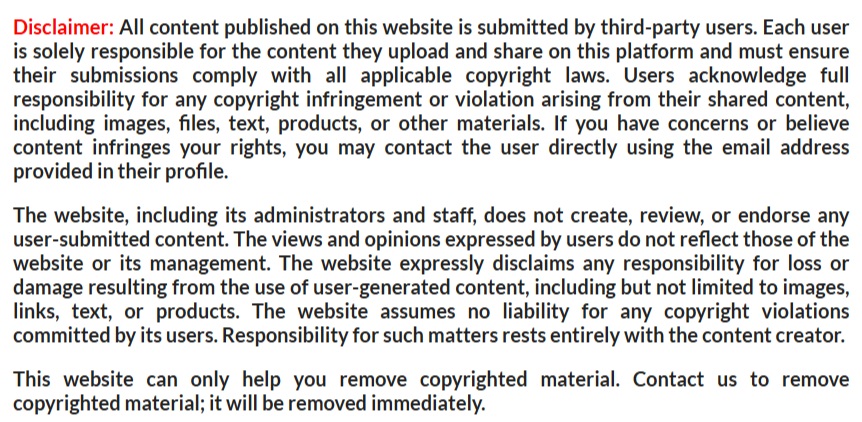