views
Desiccants: The Moisture-Fighters in Pharma & Nutra
In pharmaceuticals and nutraceuticals, moisture is a hidden threat—it can degrade active ingredients, reduce efficacy, and shorten shelf life. That’s where desiccants come in: tiny packets, canisters, or inserts that actively absorb water to keep the contents dry and stable
Common Desiccant Types
1. Silica Gel
- Made of amorphous silicon dioxide beads with pore sizes of ~2.4 nm, silica gel offers a huge internal surface—about 750 m² per gram—enabling it to adsorb up to ~37–40% of its own weight in moisture.
- It's non‑toxic, chemically inert, FDA-approved for food and drug packaging, and stable in most typical storage conditions.
- Works best at moderate to high relative humidity and room temperatures. However, performance can drop at higher temperatures where it may actually release moisture back into the package.
2. Molecular Sieves
- Synthetic zeolites—crystalline aluminosilicates—with precise micropores (e.g. 3Å, 4Å, 5Å, 13X) that selectively adsorb water molecules while excluding larger molecules.
- They provide superior moisture control even at low humidity and high temperatures, maintaining effectiveness across a wide thermal range.
- Preferred where extreme dryness is required—like diagnostic strips or highly moisture-sensitive APIs.
3. Montmorillonite Clay (Activated Clay)
- A natural, cost-effective desiccant made from layered aluminosilicate, capable of adsorbing moisture between its layers.
- It’s suitable for moderate humidity and temperature ranges, though its adsorption capacity is lower than silica gel and molecular sieves (~25%). It also can release moisture at higher temperatures.
4. Activated Alumina & Others
- Activated alumina (porous aluminium oxide) is less common in pharma but useful for gas and liquid drying, and medical device environments needing suppression of moisture and impurities.
- Other chemical desiccants—like calcium oxide, calcium chloride, and activated carbon—can also be used depending on the system, though are more common in industrial contexts.
Why Desiccants Matter in Pharma & Nutra
- Preserve API stability: Moisture can trigger hydrolysis or oxidation of active ingredients, reducing potency and potentially altering efficacy.
- Prevent physical issues: For powders or capsules, humidity can lead to clumping, caking, or brittle shell formation.
- Extend shelf life: By controlling humidity, desiccants help ensure products remain effective throughout intended shelf life.
- Support regulatory compliance: Desiccant materials and packaging must meet FDA, EMA, or other regulatory body standards—ensuring non-toxicity, inertness, and proper packaging labeling and performance documentation.
Matching the Right Desiccant to the Right Product
When choosing a desiccant:
- Assess moisture sensitivity: Highly sensitive items (like effervescent tablets or biodiagnostics) may need molecular sieves; less sensitive goods may safely use silica gel or clay.
- Evaluate storage environment: Hot, humid climates call for molecular sieves due to their high‑temperature stability; stable, moderate conditions may favor silica gel. Clay is best suited for milder scenarios.
- Consider packaging constraints: Sachets, canisters, strip-loading packets, or blister-integrated forms may be required depending on packaging speed and design.
- Calculate the required dose: Determine desiccant amount based on packaging headspace, transmission rates, ambient conditions, and target RH and shelf life.
Advanced & Innovative Desiccant Solutions
The pharma and nutraceutical industries are moving toward smarter, more efficient moisture control options:
- Indicating desiccants: These change color (e.g. cobalt-free indicators) to signal when saturation is reached—helpful for visual quality checks.
- Combination solutions: Blends that integrate molecular sieves with odor‑absorbing activated carbon or dual‑function systems.
- Integrated & polymer-based desiccants: Desiccant-infused barrier films, blister-pack adhesives or liners that eliminate the need for separate sachets.
- Sustainability efforts: Cheaper, eco-friendly materials; recyclable sachets; and energy-efficient regeneration techniques to reduce waste.
Best Practices for Use
- Proper placement: Position desiccants for optimal air exposure—e.g. bottle lids, interior caps, or integrated in blister pack seals.
- Tracking performance: Where applicable, combine with humidity indicators to monitor desiccant saturation.
- Training and compliance: Ensure staff understand safe handling (especially for fine powders) and maintain documentation for GMP and regulatory review.
- Supplier QA: Desiccants should be manufactured under strict quality standards, undergo batch testing, and be sourced from audited suppliers
Desiccant Type |
Adsorption Capacity |
Temperature / Humidity Range |
Notable Features |
Ideal Use Case |
Silica Gel |
~37–40% of weight |
Best at moderate RH, lower temps |
Inert, FDA-approved, cost-effective |
Capsules, general pharma packaging |
Molecular Sieves (e.g. 4A) |
Very high, even at low RH |
High temp & low RH stability |
Precise moisture control, regenerable |
Moisture-sensitive APIs, diagnostics, high‑temp regions |
Montmorillonite Clay |
~25% |
Moderate RH, up to ~120 °F |
Natural, economical |
Nutraceuticals, general supplements |
Activated Alumina / Others |
Varies |
Special cases |
Gas/liquid drying, odor control |
Medical devices, specialty packaging |
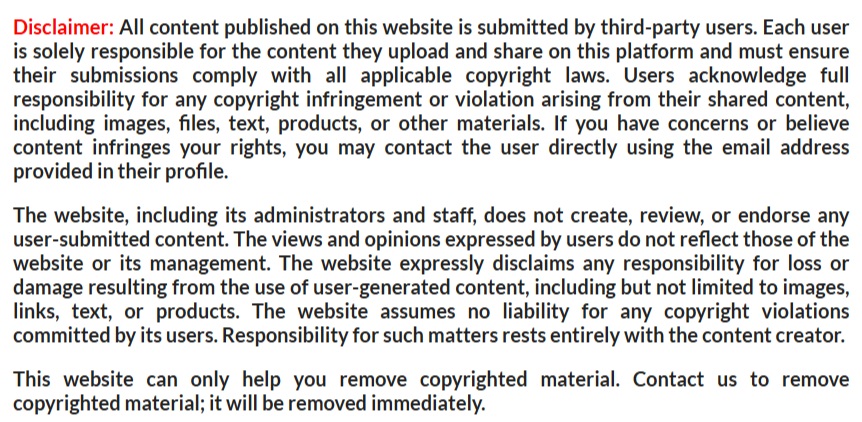