views
Aluminum’s Versatility in Manufacturing
Aluminum is one of the most widely used metals in the world due to its versatility and favorable properties. While aluminum is lightweight, it is also very strong, durable, and corrosion-resistant - making it perfect for a variety of applications. One manufacturing process that takes advantage of these great aluminum qualities is extrusion.
Extrusion allows aluminum to be shaped into almost any form while maintaining its strength. A heated aluminum billet is forced at high pressure through a shaped die to create a continuous profile. This allows complex and intricate shapes to be produced in a single production step. Extrusion is economical for high-volume production runs and lends aluminum products strength without adding excessive weight.
Common Extruded Aluminum Products
Some of the most common extruded aluminum products include:
- Window and door frames: Aluminium Extrusion frames are lightweight, strong, and resist corrosion, making them a popular material for windows, doors, skylights, and storefronts. Their seamless design also improves weather resistance.
- Automotive parts: Extruded aluminum is commonly used in cars for bumpers, wheels, drive shafts, pedals, and more. Its strength-to-weight ratio is ideal for automotive applications seeking to improve fuel efficiency.
- Building panels and siding: Durable extruded aluminum siding resists dents and never needs to be painted. It is a low-maintenance choice that holds up well to various climates.
- Heat sinks: Thin extruded fins maximize surface area and effectively dissipate heat generated by electronics and industrial equipment. This allows for more compact designs.
- Transport and shipping containers: Shipping containers, truck trailers, airplane components, cargo vessels - all benefit from extruded aluminum's durability and corrosion resistance.
- Industrial tooling and machinery: Extruded aluminum structural parts provide strength without excessive heft in industrial equipment like lathes, milling machines, and robotic arms.
Adaptable Manufacturing With Aluminum Extrusion
Aluminum extrusion can be customized in various ways depending on the specific part or product requirements:
- Shape: Dies can be designed to produce an endless array of profiles from simple rounds/squares to complex multi-sided shapes with undercuts or hollow sections.
- Wall thickness: Thinner walls minimize weight while thicker walls add strength. Graded wall thicknesses are possible too.
- Finishes: Mill-finish extrusions may undergo secondary processes like anodizing, powder coating, cladding with other metals.
- Post-processing: Extrusions can be cut, bent, machined, punched, or joined to other pieces to create assemblies.
- Alloys: Different aluminum alloys like 6063, 6061, 5005, etc. provide a range of properties for different load requirements.
This adaptability and versatility has made aluminum extrusion popular across many manufacturing industries. Mechanical properties can be tailored as needed through alloy selection and wall thickness variations. Shapes are limited only by the ability to design and fabricate production dies.
Ensuring Quality With Process Control
Strict process control is important in aluminum extrusion to maximize quality. Key factors include:
- Billet preheating: Aluminum must reach the right temperature, typically 600-650°C, to extrude smoothly at low force. Insufficient heating causes defects.
- Homogenous billet temperature: Hot and cold spots lead to varying die pressures and non-uniform extrusion.
- Die assembly: Precise dies manufactured to tight tolerances minimize flash and waste. Proper lubrication and maintenance extends die life.
- Extrusion speed: Too fast and aluminum cools too quickly, while too slow reduces productivity and allows more defects to form.
- Finishing processes: Operations like cutting must not distort the shape or weaken the extrusion in any way.
With proper control of these variables, manufacturers can achieve extrusion yields above 90% and meet tight dimensional tolerances of +/-0.05mm. This level of control and consistency has been integral to aluminum extrusion’s growing role across many industries.
As manufacturing continues to evolve, so do the possibilities for extruded aluminum products. New alloy formulations further enhance properties. Advances in die design allow more intricate hollow or multi-profile extrusions. Automation and process monitoring technologies boost quality and yields. These factors suggest aluminum extrusion will play a vital role shaping innovation for years to come. With aluminum’s favorable mix of attributes and extrusion’s design freedom, the applications for this manufacturing process are virtually limitless. The future remains bright as extruded aluminum solutions continue enabling progress across countless industries.
Choose your Preferred language for better understanding-
About Author-
Ravina Pandya, Content Writer, has a strong foothold in the market research industry. She specializes in writing well-researched articles from different industries, including food and beverages, information and technology, healthcare, chemical and materials, etc. With an MBA in E-commerce, she has an expertise in SEO-optimized content that resonates with industry professionals. (https://www.linkedin.com/in/ravina-pandya-1a3984191)
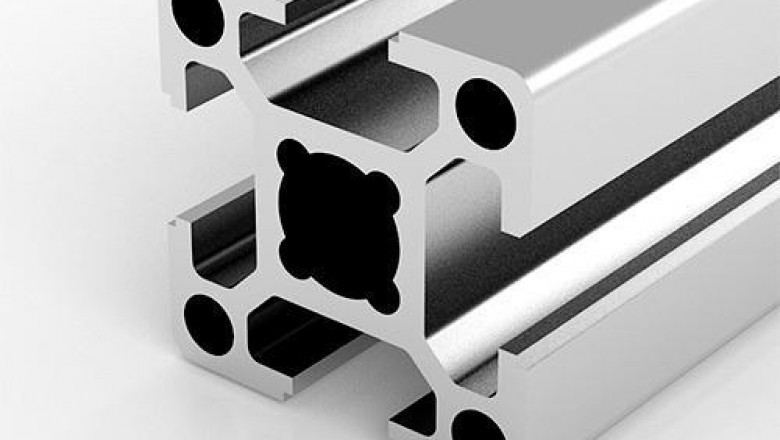

Comments
0 comment