views
CNC bending machines have changed metal fabrication by offering the best results, efficiency, and consistency in making difficult bends. But if you want to get maximum accuracy with these machines then it requires more than advanced technology. However, it requires detailed attention, proper setup and regular maintenance. Any kind of minor inaccuracies may cause costly errors and material waste, whether you produce simple or difficult materials. In this article, you will explore more about the CNC bending machine for sheet metal and how it can help to improve your performance.
6 Tips to Maximize Accuracy with Your CNC Bending Machine
1. Choose the Correct Tool
The use of proper tools brings accuracy. It is crucial to use the correct die and punch for the material and blend requirements. The V-die opening must match the material thickness and type to reduce deformation and ensure accurate bends. Moreover, high-quality tooling also requires consistent maintenance over time.
2. Material Preparation Matters
Bad quality material can lead to poor results even if you are using a highly accurate machine. You must ensure that metal sheets are uniform in thickness and imperfection-free. However, some variation in material properties like hardness or grain direction can affect your metal bends.
3. Calibrate Regularly
Regular calibration is necessary for your CNC bending machine. Over time, sensors and components of your machine can drift out of alignment which can lead to inaccuracies. Moreover, daily maintenance and adjustments help you to maintain control over angles and dimensions.
4. Use CNC Software Features
There are many CNC machines that come with advanced features that help optimize the bending process easily. You must learn these features like bend allowance calculations, automatic spring-back compensation, and more. Moreover, inserting the right material data into the software allows you to adjust for factors with accuracy.
5. Input Quality Control Measures
It is necessary to ensure accuracy while doing in-process inspections and final quality checks. You can use precision measuring tools like angle finders and others to verify bends. You can create a feedback loop where operators can make corrections timely which minimizes rework and waste.
6. Perform Preventive Maintenance
A well-maintained machine delivers better results over time. You just need to follow the manufacturer's recommended maintenance schedule. It may include lubricating moving parts, checking hydraulic systems, and replacing worn components. If you use these preventive maintenance techniques, it will minimize inaccuracy and maintain your machine’s performance.
Conclusion
CNC bending machines with a combination of proper tooling, quality materials, and timely maintenance help in maximizing the accuracy of your work. Manufacturers can easily achieve the best results if they make an investment in training and follow the right tips. If you want to upgrade your shop or start any new business, then it is important to identify your equipment needs. You can consider using a reputable brand to buy and sell industrial equipment to replace your outdated machine. To know more in detail, visit Industrial Machinery Company today!


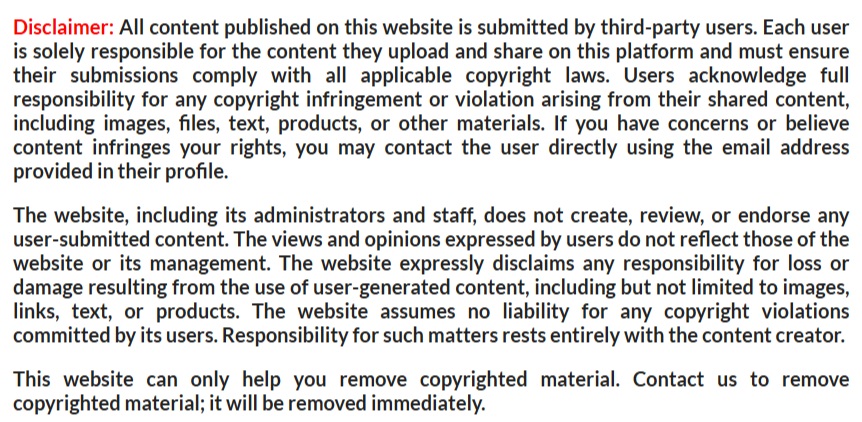
Comments
0 comment