views
The dry battery electrode market is quickly becoming a focal point in the global energy storage ecosystem. As industries demand more sustainable, efficient, and high-performance battery production methods, dry electrode technology is gaining traction for its ability to eliminate harmful solvents, reduce energy use, and streamline manufacturing. Market intelligence surrounding this space reveals not only growth opportunities but also a rapidly shifting landscape driven by innovation, regulation, and strategic investment. Stakeholders across the battery value chain must stay informed to remain competitive in this accelerating market.
1. Industry Shifts Driven by Sustainability and Regulatory Mandates
One of the most significant insights from current market intelligence is the growing emphasis on green manufacturing. Dry electrode technology aligns closely with environmental mandates across regions like the European Union, the United States, and parts of Asia. These policies support solvent-free processes and low-emission production lines. Companies that adopt dry electrode manufacturing not only reduce their carbon footprint but also future-proof their operations against tightening environmental regulations.
This sustainability imperative is not just regulatory but also market-driven, with investors and end-users increasingly favoring environmentally responsible brands. As ESG (Environmental, Social, and Governance) metrics become more critical in evaluating corporate performance, adopting dry electrode technologies gives manufacturers a reputational and financial edge.
2. Competitive Intelligence: Key Players and Strategic Moves
Market intelligence reveals that major battery manufacturers are racing to adopt and refine dry electrode technologies. Companies such as Tesla, Panasonic, and LG Energy Solution are developing or acquiring proprietary processes to maintain technological leadership. Startups like 24M Technologies and Electrovaya are also becoming significant disruptors by offering scalable, efficient dry electrode platforms.
Key strategic moves include:
-
Joint ventures between automotive OEMs and battery makers
-
Licensing of dry coating intellectual property
-
Partnerships with material science firms to improve electrode compatibility
This competitive activity signals growing confidence in dry electrode adoption and the potential for long-term commercial viability.
3. Demand Intelligence: Target Applications and Market Penetration
The market is seeing increased adoption of dry battery electrodes in high-growth applications:
-
Electric Vehicles (EVs): Automakers are pushing for lighter, energy-dense batteries that can be produced faster and with fewer environmental impacts.
-
Stationary Energy Storage Systems (ESS): As grids incorporate more renewable energy, the need for scalable, high-performance storage is growing.
-
Consumer Electronics: Smartphones, laptops, and wearables benefit from dry electrode technology due to its form factor flexibility and energy efficiency.
Understanding where demand is highest—and where it's headed—is essential for manufacturers looking to align production capabilities with future market needs.
4. Technological Intelligence: Material and Process Innovations
Technological evolution remains a core component of the dry battery electrode market’s intelligence landscape. Innovations include:
-
Use of solid electrolytes for compatibility with dry-coated electrodes
-
Development of binder-free and additive-free electrode materials
-
Laser compression and calendaring for enhanced electrode density
-
Hybrid electrode technologies for flexible applications
These innovations are helping overcome long-standing challenges such as material compatibility and process uniformity. As R&D investment grows, breakthroughs in energy density and cycle life are expected to redefine product offerings.
5. Investment and Funding Intelligence
Capital flow into the dry battery electrode segment is accelerating. Venture capital firms, government programs, and corporate R&D budgets are all being directed toward advancing this technology.
Examples include:
-
U.S. Department of Energy (DOE) grants for dry electrode pilot lines
-
EU funding for clean battery initiatives under the Green Deal
-
Private equity investments in startups offering next-gen battery materials
This funding is essential not just for innovation but for scaling manufacturing capacity, especially as market leaders move from lab-scale to gigafactory-level production.
6. Regional Intelligence and Market Hotspots
Insights into regional performance show that adoption patterns vary widely:
-
North America: A hub for innovation and pilot projects, driven by government incentives and EV demand.
-
Europe: Strong policy support for green manufacturing is leading to faster commercial adoption of dry technologies.
-
Asia-Pacific: The region continues to lead in battery manufacturing capacity and is rapidly integrating dry processing lines to stay competitive globally.
Regional intelligence helps stakeholders identify supply chain opportunities, talent pools, and infrastructure readiness for expansion.
7. Barriers and Strategic Considerations
While the outlook is promising, several challenges remain:
-
High upfront costs for transitioning from wet to dry manufacturing
-
Limited standardization in dry electrode processes
-
Need for workforce training and technical knowledge in dry processing
Smart players are addressing these through strategic alliances, automation investments, and government partnerships to ease the transition.
Conclusion
The dry battery electrode market is not just an emerging trend—it is becoming a central pillar in the future of sustainable energy storage. Market intelligence highlights a landscape full of opportunity but also marked by complexity and rapid change. From material innovations and evolving regulations to competitive dynamics and regional readiness, understanding these moving parts is essential. Businesses that can interpret and act on these insights will be best positioned to lead in the global shift toward greener, faster, and more resilient battery manufacturing systems.
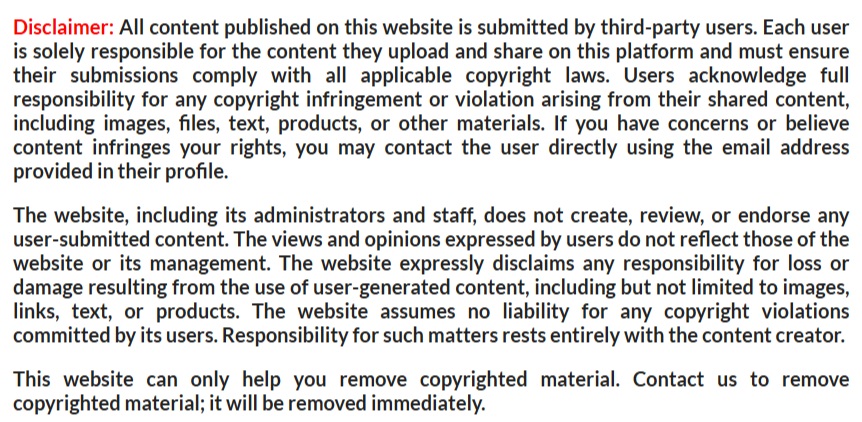