views
Success in today’s marketplace hinges on a company’s ability to deliver quality without compromise.
Success in today’s marketplace hinges on a company’s ability to deliver quality without compromise. That’s where quality management comes into play—a methodical approach that integrates strategic thinking with operational discipline to meet and exceed standards. It ensures that excellence isn’t left to chance but is the result of thoughtful planning and execution.
At its heart, quality management is about building systems that work right the first time. Quality assurance focuses on designing those systems to prevent errors, while quality control ensures that what is produced or delivered matches expectations. This proactive and reactive balance helps organizations reduce costs, increase efficiency, and boost satisfaction.
This framework consists of four essential elements: quality planning, quality assurance, quality control, and quality improvement. Planning identifies key goals and quality benchmarks. Assurance ensures those targets are achievable through proper processes. Control compares actual outcomes to those goals, and improvement seeks new ways to enhance performance. Together, they form a comprehensive cycle that drives continuous progress. Businesses that adopt this system can consistently deliver reliable results, adapt to change, and maintain a competitive edge.
Quality Management Systems (QMS)
A quality management system (QMS) is a structured collection of processes and policies focused on fulfilling customer requirements and elevating satisfaction levels. Aligned with organizational goals and ISO standards, a QMS documents procedures, roles, and resources needed to implement and maintain quality practices
ISO 9001 Standard
ISO 9001, part of the ISO 9000 family, specifies the requirements for a robust QMS. Certification under ISO 9001 demonstrates a commitment to systematic quality assurance, rigorous documentation, and regular internal and external audits—offering competitive advantages and fostering consumer trust.
Total Quality Management (TQM)
Total Quality Management (TQM) extends quality practices across every department—production, sales, finance, and beyond—to cultivate a culture where continuous improvement is everyone’s responsibility. TQM emphasizes leadership commitment, employee involvement, and data-driven decision-making to deliver products and services of exceptional value.
Companies like Toyota leveraged TQM principles to pioneer the Kanban system, achieving lean inventory management and rapid turnaround times—proof that a holistic quality culture can yield transformative results.
Quality Management Methodologies
PDCA Cycle (Plan–Do–Check–Act)
The PDCA cycle, also known as the Deming cycle, is an iterative framework for controlling and continuously improving processes. Organizations plan objectives, execute plans, evaluate outcomes, and act on insights—then repeat the cycle to drive incremental gains and prevent recurring issues.
Six Sigma
Six Sigma is a data-driven methodology aimed at reducing process variation and eliminating defects. Introduced by Motorola in 1986, Six Sigma projects follow DMAIC (Define, Measure, Analyze, Improve, Control) or DMADV (Define, Measure, Analyze, Design, Verify) roadmaps to achieve quantifiable improvements in quality and efficiency.
Lean Management
Lean enterprise focuses on maximizing customer value by eliminating non-value-added activities (waste). Rooted in the Toyota Production System, Lean employs tools such as value stream mapping and 5S to optimize workflows, reduce costs, and accelerate delivery.
Implementing a Quality Management System
- Assess Current State: Conduct a gap analysis to benchmark existing processes against QMS requirements.
- Define Quality Policy and Objectives: Establish measurable goals aligned with customer needs and regulatory standards.
- Document Processes: Create clear procedures, work instructions, and flowcharts to standardize operations.
- Train and Empower Employees: Provide quality assurance training and foster a culture of accountability.
- Monitor and Audit: Regularly evaluate process performance using key quality indicators and conduct internal audits.
- Continuous Improvement: Use corrective actions, root-cause analysis, and management reviews to refine processes.
Benefits of Quality Management
- Enhanced Customer Satisfaction: Deliver consistent product quality and build trust.
- Operational Efficiency: Reduce rework and waste, lowering costs and boosting throughput.
- Regulatory Compliance: Maintain up-to-date documentation and meet industry standards.
- Competitive Advantage: Differentiate offerings through certified quality and superior performance.
Role of Quality Management Software
Modern quality management software automates document control, audit scheduling, nonconformance tracking, and CAPA workflows—enabling real-time visibility into quality metrics. By centralizing quality data, organizations can make faster, evidence-based decisions and accelerate continuous improvement.
Ready to elevate your quality assurance and control processes? Discover how ToolkitX’s Quality Management Software can help you implement a scalable, ISO-aligned QMS. Visit https://toolkitx.com/campaign/quality-management/ to schedule a demo and start your journey toward operational excellence.
Frequently Asked Questions
1. What’s the difference between quality assurance and quality control?
Quality assurance focuses on the processes and standards designed to prevent defects, while quality control involves the inspection and testing activities that detect and correct defects in products or services.
2. How does ISO 9001 certification benefit my business?
ISO 9001 certification signals to customers and partners that your organization adheres to internationally recognized quality standards, improving credibility, market access, and customer trust.
3. How long does it take to implement a QMS?
Implementation timelines vary by organization size and complexity but typically range from 3 to 12 months—from initial gap analysis to full integration of documented processes and employee training.
4. Can small businesses adopt Six Sigma?
Yes. Six Sigma methodologies can scale to organizations of all sizes. Small teams often focus on targeted DMAIC projects to achieve quick wins in process improvement before expanding their scope.
5. What key metrics should I track in my QMS?
Common QMS metrics include defect rates (DPMO), on-time delivery, audit nonconformances, customer complaint rates, and process cycle times—each aligned with your quality objectives.

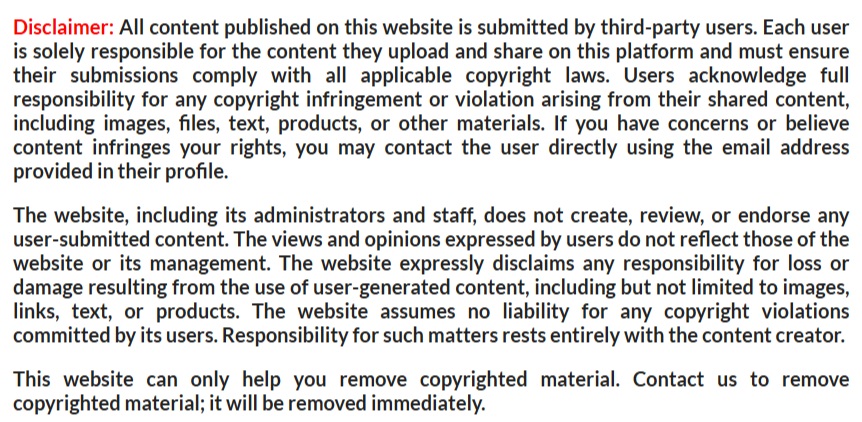
Comments
0 comment