views
Introduction
The 3D printing stainless steel market is growing rapidly as industries embrace metal additive manufacturing for its strength, precision, and design flexibility. With applications spanning aerospace, automotive, healthcare, and industrial sectors, stainless steel has emerged as a preferred material due to its excellent mechanical properties and corrosion resistance. However, despite the market’s promising future, several challenges and barriers continue to impact its pace of growth and global adoption.
This article explores the key issues slowing down progress in the stainless steel 3D printing market and what it will take to overcome them.
Market Overview
In 2023, the 3D printing stainless steel market was valued at approximately USD 500 million, with projections suggesting it could surpass USD 1.2 billion by 2030. This growth is driven by increasing demand for complex, durable parts and advancements in additive manufacturing technology. However, a number of critical obstacles must be addressed for the market to reach its full potential.
Key Challenges and Barriers
1. High Equipment and Material Costs
One of the biggest barriers to entry in the 3D metal printing market is the high upfront investment in machines and materials. Industrial-grade 3D printers capable of producing stainless steel parts can cost hundreds of thousands of dollars, and stainless steel powders like 316L and 17-4 PH are significantly more expensive than raw metal stock used in traditional manufacturing.
Impact:
-
Limits adoption among small and mid-sized manufacturers
-
Slows down scalability for high-volume production
2. Slow Production Speed
Compared to traditional methods such as casting or CNC machining, 3D printing stainless steel can be time-consuming, especially for large or highly detailed parts. While innovations like binder jetting and multi-laser systems are improving speeds, additive processes are still relatively slow for mass manufacturing.
Impact:
-
Unsuitable for high-volume production runs
-
May hinder ROI for time-sensitive industries
3. Lack of Industry Standards and Certification
For mission-critical sectors like aerospace, medical, and automotive, strict regulatory standards apply. While organizations like ASTM and ISO are working on standardizing additive manufacturing, the current landscape lacks consistent frameworks for certifying 3D printed stainless steel parts.
Impact:
-
Slows adoption in regulated industries
-
Increases the cost and time needed for part validation and testing
4. Material and Process Limitations
Although stainless steel is a popular material, not all alloys are equally suitable for 3D printing. Variations in powder quality, particle size distribution, and flowability can affect the printability and final mechanical properties. Additionally, post-processing—such as heat treatment, surface finishing, and support removal—adds complexity and cost.
Impact:
-
Quality inconsistency between batches
-
Increased dependency on skilled technicians and advanced QA/QC systems
5. Skills Gap and Talent Shortage
Operating advanced metal 3D printers and optimizing part design for additive manufacturing requires specialized skills in CAD, materials science, and engineering. Many regions still lack adequate training programs to meet the growing demand for skilled professionals in metal additive manufacturing.
Impact:
-
Delays in project execution and scaling
-
Limits widespread adoption across industries
6. Supply Chain Fragmentation
Unlike traditional manufacturing, where supply chains are well-established, the 3D printing stainless steel ecosystem is still evolving. There’s often a disconnect between hardware providers, material suppliers, software developers, and end users.
Impact:
-
Inefficiencies in workflow integration
-
Slower product development cycles
Additional Concerns
-
Environmental impact of metal powder production
-
Data security risks associated with digital part files
-
Intellectual property (IP) protection in decentralized production models
Strategies for Overcoming Barriers
To realize the full potential of the 3D printing stainless steel market, coordinated efforts are needed across the ecosystem:
-
Cost reduction through material recycling and process optimization
-
Development of industry-wide standards and regulatory frameworks
-
Investments in education and training for AM professionals
-
Collaborative platforms to align software, hardware, and materials
-
Research in alloy development tailored for additive manufacturing
Conclusion
The 3D printing stainless steel market holds immense promise—but unlocking its full potential will require overcoming a range of technical, economic, and regulatory challenges. As innovations continue and the ecosystem matures, these barriers will gradually diminish, opening up broader applications and driving industrial transformation. For stakeholders across the value chain, addressing these pain points will be crucial to staying competitive in the evolving landscape of metal additive manufacturing.

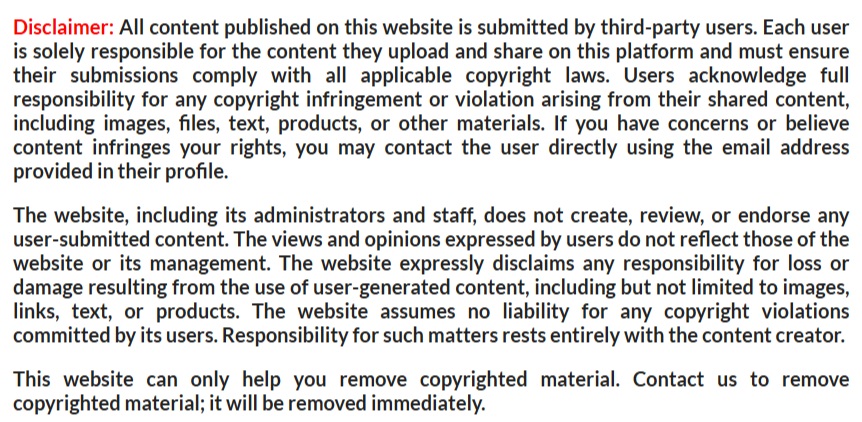
Comments
0 comment