views
Aluminum is one of the most commonly used metals across industries due to its durability, lightweight properties, and corrosion resistance. However, when it comes to enhancing its aesthetic appeal and extending its lifespan in extreme environments, powder coating is the go-to finishing solution. Brands like Decoral America have championed advanced powder coating techniques that not only protect aluminum but also offer design versatility for countless applications.
Whether you're in construction, manufacturing, architecture, or consumer goods, understanding the aluminum powder coating process is essential for achieving both performance and visual excellence. This guide breaks down the entire process step-by-step and explores its benefits, applications, and maintenance needs.
What Is Aluminum Powder Coating?
Powder coating is a dry finishing technique where a fine powder made of resin and pigment is electrostatically applied to a metal surface—in this case, aluminum. After application, the coated aluminum is cured in an oven, which causes the powder to melt and fuse into a uniform, protective, and decorative finish.
Unlike liquid paint, powder coating contains no solvents and emits negligible volatile organic compounds (VOCs), making it a more environmentally friendly option.
Step-by-Step Process of Powder Coating Aluminum
1. Surface Preparation
The first and most crucial step in the aluminum powder coating process is thorough surface preparation. Any dirt, oil, oxidation, or residue on the metal must be removed to ensure optimal coating adhesion.
Key surface preparation techniques include:
-
Degreasing: Using solvents or alkaline solutions to remove oil and contaminants.
-
Etching or chemical cleaning: Removes natural aluminum oxide that forms on the surface.
-
Rinsing: Ensures the metal is free from cleaning agents.
-
Chromate or non-chromate conversion coating: Enhances corrosion resistance and improves powder adhesion.
2. Drying
Once cleaned, the aluminum is thoroughly dried to prevent water spots or moisture from interfering with the application. Some facilities use heated drying tunnels to speed up this process.
3. Electrostatic Powder Application
Using an electrostatic spray gun, powder particles are charged and sprayed onto the grounded aluminum surface. The electrostatic attraction ensures that the powder adheres uniformly, even on complex shapes or intricate designs.
4. Curing in the Oven
After application, the coated aluminum is placed in a curing oven, typically set between 350°F and 400°F (175°C–205°C), depending on the powder type. The heat melts the powder and creates a smooth, durable finish that bonds to the metal.
Curing time usually ranges from 10 to 20 minutes, but precise timing is critical—under-curing or over-curing can affect coating performance.
5. Cooling and Inspection
Once cured, the aluminum is allowed to cool naturally. The final step includes visual inspection and quality control checks for color consistency, thickness, adhesion, and finish integrity.
Benefits of Powder Coating Aluminum
1. Durability
Powder-coated aluminum is highly resistant to scratches, chipping, corrosion, fading, and wear. This makes it ideal for outdoor furniture, architectural facades, and high-traffic surfaces.
2. Environmentally Friendly
Powder coating is a clean process with nearly zero VOC emissions, no hazardous waste, and overspray that can often be recycled. This makes it a sustainable choice for eco-conscious industries.
3. Aesthetic Versatility
Available in a wide array of colors, finishes (matte, gloss, textured), and even wood grain or metallic effects, powder coating allows design flexibility that suits modern architecture and consumer trends.
4. Cost-Effective Long-Term
While initial costs may be higher than traditional painting, the longevity and low maintenance of powder-coated aluminum lead to reduced long-term costs.
Common Applications of Powder-Coated Aluminum
Powder-coated aluminum is used in a wide range of industries due to its strength, finish options, and weather resistance. Some popular applications include:
-
Architectural Components: Window frames, curtain walls, railings, and louvers
-
Consumer Products: Outdoor furniture, light fixtures, bicycles
-
Automotive Parts: Wheels, trim, bumpers
-
Electronics and Appliances: Enclosures, hardware, panels
-
Industrial Equipment: Machinery parts, storage units, safety barriers
Maintenance Tips for Powder-Coated Aluminum
Proper maintenance extends the life and appearance of powder-coated aluminum. Fortunately, upkeep is minimal:
-
Regular Cleaning: Wash surfaces with a mild detergent and water to remove dust and debris.
-
Avoid Harsh Chemicals: Do not use abrasive pads, solvents, or strong alkaline cleaners.
-
Inspect for Damage: Address chips or scratches promptly to prevent corrosion in exposed areas.
For high-exposure environments (coastal, industrial), more frequent cleaning may be necessary to remove salt or pollutants that can degrade the coating over time.
Choosing the Right Powder Coating
When selecting powder coatings for aluminum, consider the following:
-
Type of Resin: Epoxy, polyester, polyurethane, and hybrid powders all offer different levels of UV resistance, chemical protection, and flexibility.
-
Finish and Color Requirements: Aesthetic goals and branding might influence gloss levels or color vibrancy.
-
Performance Standards: Look for certifications such as AAMA 2604/2605 for architectural coatings.
Working with an experienced coating provider ensures your aluminum surfaces meet the performance and design goals of your project.
Conclusion
Powder coating is more than just a finishing step—it's a vital process that enhances the strength, longevity, and visual impact of aluminum components across countless industries. From sleek modern architecture to rugged industrial uses, powder-coated aluminum offers unbeatable benefits in durability and design.
As the demand for sustainable, high-performance finishes continues to rise, the aluminum powder coating process stands out as a smart, eco-friendly choice. With proper application and minimal maintenance, your aluminum components can retain their beauty and functionality for decades to come.

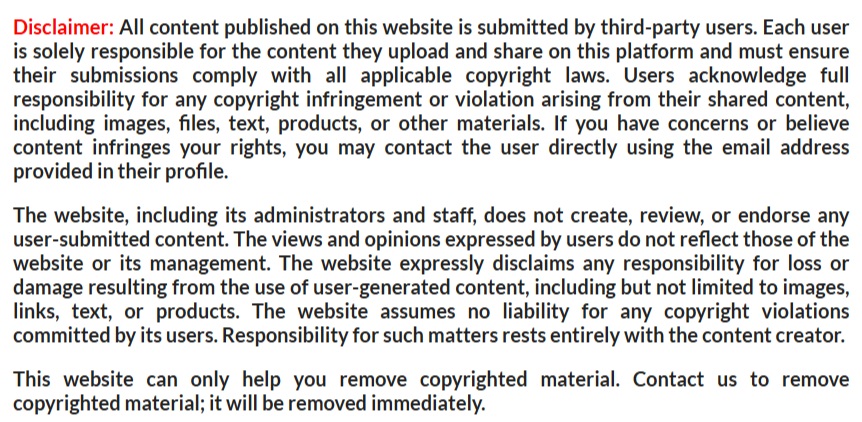
Comments
0 comment