views
CNC Press Brake
In modern manufacturing, automation plays a crucial role in improving efficiency and accuracy. The integration of automation in CNC Press Brake machines has significantly enhanced productivity, making metal bending operations faster, more precise, and cost-effective. Leading Bending Machine Manufacturers are developing advanced automated systems to streamline the bending process, reducing human error and operational downtime. Whether using a Mechanical Press Brake or a hydraulic system, automation is transforming the way manufacturers handle metal fabrication.
1. Increased Speed and Efficiency
Automation in CNC Press Brake machines reduces cycle times, allowing for faster bending operations. Traditional manual setups require constant adjustments, leading to delays. However, automated CNC controls optimize machine settings instantly, eliminating the need for repetitive reconfigurations. As a result, manufacturers experience higher throughput with minimal waste, enhancing overall production efficiency.
2. Enhanced Precision and Consistency
Manual bending operations are prone to errors due to human inconsistencies. An automated CNC Press Brake ensures every bend is executed with precision, thanks to real-time monitoring and adaptive controls. These machines use advanced sensors and backgauge systems to maintain accuracy, ensuring uniformity across large production runs. A reliable Bending Machine Manufacturer integrates laser-based measuring systems that further enhance precision.
3. Reduction in Material Waste
Material waste can significantly impact production costs. Automation minimizes errors and improves repeatability, ensuring that every metal sheet is bent correctly on the first attempt. With features like automatic angle correction and intelligent material positioning, a Mechanical Press Brake equipped with automation reduces material wastage, leading to substantial cost savings for manufacturers.
4. Improved Safety Standards
Automated CNC Press Brake machines come with advanced safety features such as laser guarding, light curtains, and emergency stop systems. These safety measures protect operators from potential hazards, reducing workplace injuries. Unlike manual press brakes, automated systems require minimal human intervention, decreasing the chances of accidents.
5. Reduced Dependency on Skilled Labor
The shortage of skilled labor is a challenge for many manufacturing companies. Automation eliminates the need for highly skilled operators by simplifying the machine's operation. Even less-experienced workers can efficiently operate an automated CNC Press Brake, as the system performs complex calculations and adjustments automatically. This reduces training costs and improves workforce efficiency.
6. Remote Monitoring and Data Analysis
Modern automated Mechanical Press Brake machines are equipped with IoT capabilities, allowing remote monitoring and performance analysis. Manufacturers can track real-time data on production efficiency, machine wear, and maintenance needs. This predictive maintenance approach minimizes downtime and extends the machine’s lifespan, ensuring consistent productivity.

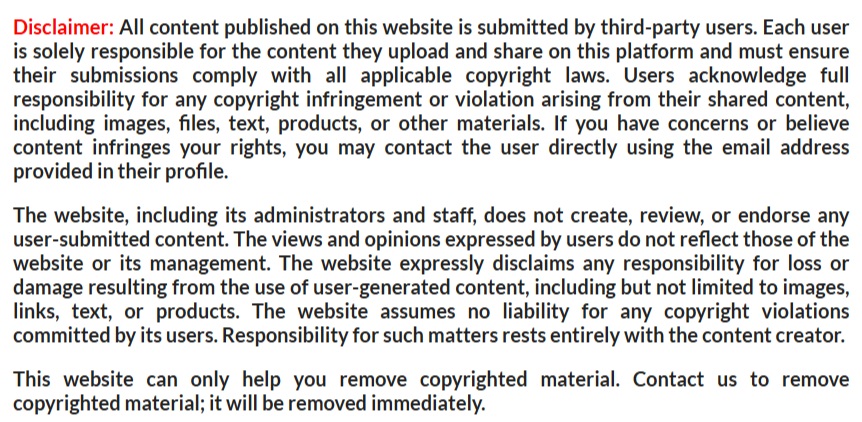
Comments
0 comment