views
Stainless Steel Vessels for Biomanufacturing Processes
Stainless steel is the most commonly used material for bioprocess containers due to its corrosion resistance, durability and compatibility with harsh chemical treatments required for sterilization. Vessels made from stainless steel, such as fermentors and bioreactors, are optimized for growing and processing cell cultures under carefully controlled environmental conditions. The polished interior surfaces allow for thorough cleaning validation requirements.
Bioprocess Containers is inline mixing and mass transfer of gases like oxygen are effectively accomplished through the use of mechanically-driven or static mixers integrated into stainless steel vessels. Typical mixing mechanisms include pitched blade turbines, marine propellers or axial flow impellers capable of providing the shear forces necessary for homogenous cell suspension at industrial production scales. Gas sparging equipment can be customized with multiple ports to achieve the required dissolved oxygen and pH set points within the culture medium.
Automated process controls connected to an array of analytical probes and sensors monitor and regulate parameters like temperature, pH, dissolved oxygen levels and foam formation. These systems ensure process consistency and maximize cell viability, biomass and desired metabolite yields. Data acquisition capabilities allow for batch records and performance trend analysis to optimize manufacturing processes over multiple production runs.
Single-Use Flexible Bioprocess Containers for Small Volume Production
For processes requiring smaller working volumes or frequent product changeovers, single-use flexible containers provide a lower-cost alternative to stainless steel vessels. Constructed from medical-grade plastics like polyvinyl chloride (PVC) or polyethylene, these bags are designed for one-time use to eliminate the time and costs associated with cleaning and validation of reusable vessels between batches.
Compatible mixing systems can be integrated directly into the bag design using impeller inserts connected to motors situated external to the container. Gas sparging tubes and pH/dissolve oxygen probes fit through welded, sterile access ports. Containers are typically pre-sterilized and assembled in a modular, automated manner within isolators to facilitate aseptic transfers during the cell culture process.
Control systems provide the same monitoring and regulatory capabilities as stainless steel bioreactors in a compact footprint well-suited to smaller R&D, clinical or pilot-scale production needs. Single-use technologies simplify process scale-up and change management through a directly scalable bag design. The disposable nature also removes any risks of cross-contamination between product types when using the same processing equipment.
Custom Engineered Bioprocess Containers for Specialty Manufacturing Requirements
In some large-scale industrial applications, standard vessel designs may not adequately accommodate unique raw material inputs, integrated process steps or regulated product outputs. In these situations, custom engineered containers provide optimized solutions. Experienced system integrators work closely with manufacturing clients to precisely define technical requirements and design container configurations using 3D modeling tools.
For instances involving unusual particle sizes or suspensions that require specialized agitation, impellers can be machined with customized blade orientations, dimensions and materials of construction. Internal baffles, probes and injection ports are strategically positioned based on computational fluid dynamics simulations of mixing dynamics.
Containers destined for sterile environments demand careful validation of welded joints and precision-machined process connections to eliminate contamination risks. Where product blending or formulation occurs within a closed system, controllable recirculation loops with CIP functionality maintain batch consistency.
Output storage or buffer tanks incorporate advanced instrumentation, automation and controlled environmental features to assure specified product quality attributes are maintained through packaging and release. Custom vessel design thus provides the process control and flexibility required to economically manufacture niche and high-value specialty products at commercial scales.
In bioprocess containers are available in standardized and customizable configurations optimized for a variety of manufacturing applications from R&D to full commercial production. Careful material selection, integrated processing equipment and advanced process controls allow for scalable and reproducible biomanufacturing under closely regulated conditions.
For Deeper Insights, Find the Report in the Language that You want.
About Author:
Ravina Pandya, Content Writer, has a strong foothold in the market research industry. She specializes in writing well-researched articles from different industries, including food and beverages, information and technology, healthcare, chemical and materials, etc. (https://www.linkedin.com/in/ravina-pandya-1a3984191)
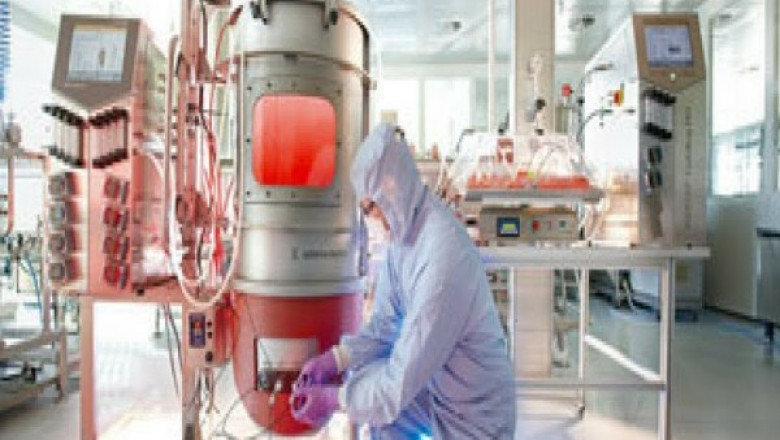

Comments
0 comment