views
When it comes to selecting materials for piping and tubing in demanding industrial environments, Stainless Steel 316 series — particularly 316, 316L, and 316Ti — consistently stands out as a top choice. These grades offer superior corrosion resistance, excellent mechanical properties, and long-term durability, making them ideal for a wide range of industries including chemical processing, marine applications, food and beverage production, and pharmaceuticals.
But what makes these stainless steel grades so special? Let’s take a closer look.
Understanding the 316 Series Stainless Steel
The 316 family of stainless steel is an austenitic alloy that contains molybdenum — a key element that enhances its corrosion resistance, especially against chlorides and other industrial solvents.
316 Stainless Steel
This is the standard molybdenum-bearing grade. It offers excellent resistance to pitting and crevice corrosion, making it suitable for harsh environments such as coastal areas or chemical plants.
316L Stainless Steel
The "L" stands for "low carbon." 316L contains a lower carbon content than 316, which reduces the risk of carbide precipitation during welding. This makes it ideal for welded structures or applications requiring extensive fabrication.
316Ti Stainless Steel
This grade includes titanium, which stabilizes the structure of the steel at high temperatures. 316Ti is especially valuable in environments where the steel will be exposed to sustained high temperatures, as the titanium prevents grain boundary corrosion that might occur in standard 316.
Why Industries Choose 316/316L/316Ti Pipes and Tubes
1. Superior Corrosion Resistance
One of the primary reasons industries rely on the 316 series is its high resistance to chloride-induced corrosion. Whether in salty marine environments or in chemical processing plants with aggressive solvents, these stainless steel grades maintain their integrity far longer than many alternatives.
2. Weldability and Fabrication
316L, in particular, is prized for its excellent weldability. It can be easily welded without the risk of intergranular corrosion, making it suitable for complex piping systems and pressure vessels.
3. High Temperature Strength
316Ti steps up where high heat is involved. The addition of titanium ensures the material can handle elevated temperatures without losing strength or becoming brittle, making it a preferred choice for heat exchangers and furnace components.
4. Hygiene and Cleanability
In industries like food processing, pharmaceuticals, and biotechnology, cleanliness is non-negotiable. The smooth, non-porous surface of 316 stainless steel is easy to clean and resistant to bacteria, making it compliant with strict hygiene standards.
5. Longevity and Cost Efficiency
Though the initial cost of 316 series stainless steel pipes and tubes may be higher than some alternatives, their longevity and low maintenance requirements often lead to significant cost savings over time. Fewer replacements, lower downtime, and reduced risk of failure add up to better overall value.
Common Industrial Applications
-
Chemical Processing Equipment
-
Marine Piping Systems
-
Pharmaceutical and Food-Grade Tubing
-
Oil and Gas Pipelines
-
Heat Exchangers and Condensers
-
Architectural and Structural Components
Conclusion
For industries where reliability, safety, and durability are critical, Stainless Steel 316/316L/316Ti pipes and tubes provide unmatched performance. Whether you're dealing with corrosive chemicals, high temperatures, or strict hygiene standards, the 316 family offers the strength and resilience needed to get the job done right.
As demand grows for high-performance materials that can withstand the rigors of modern industry, it's no surprise that the 316 stainless steel series continues to be a trusted and preferred choice across the globe.
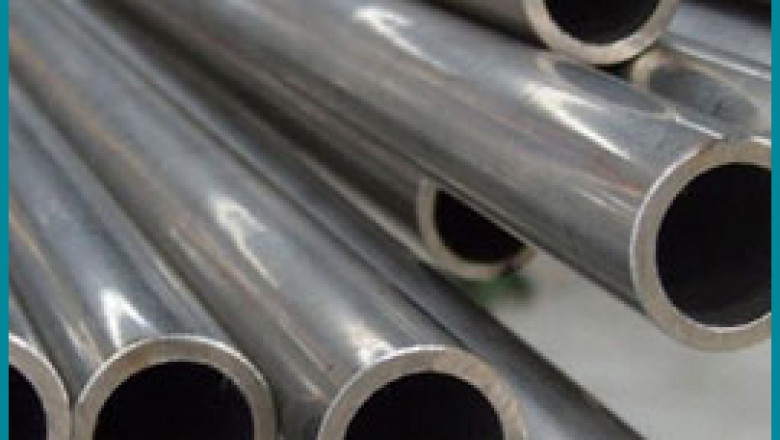
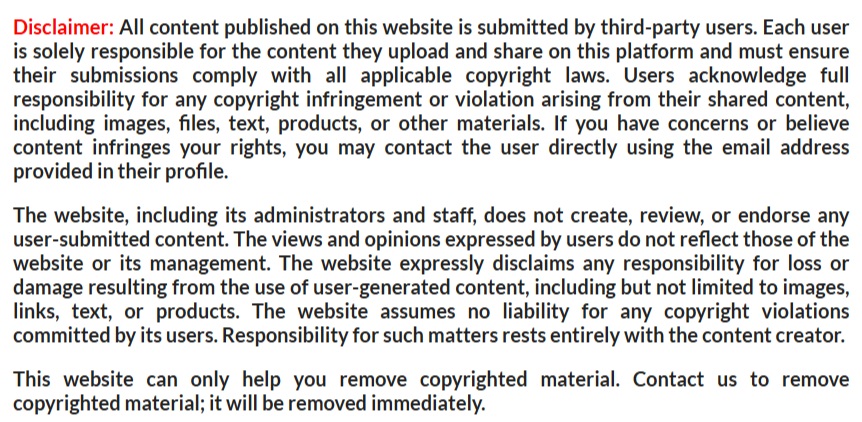
Comments
0 comment