views
It is essential for processing raw materials. Maintaining your machinery is vital to its longevity, performance, and cost-effective downtime. This article will give you top tips on maintaining your aggregate equipment in Winnipeg.
Establishing A Regular Maintenance Schedule
A consistent maintenance program is essential to keep aggregate equipment running smoothly. Regular inspections will help you identify and fix potential problems before they become more serious. Create a Checklist that includes the following:
Daily Checks: Inspect bearings, belts, filters, and the lubrication level.
Weekly Maintenance: Check for wear of components like screens.
Monthly and Quarterly Service: Perform a more comprehensive check, including an oil change, alignment inspections, and replacement of worn parts.
A preventative maintenance schedule will reduce the likelihood of unexpected breakdowns while increasing operational efficiency.
Lubricate Your Equipment Properly
Proper lubrication will reduce friction, minimize wear, and prevent overheating. Manufacturers have different lubrication recommendations for their machines. These are the best practices to follow:
Use Correct Oil: Choose oils and greases for heavy-duty machines.
Maintain lubrication intervals: Check and replenish your lubricant regularly to avoid damage.
Seals And Joints Check: Ensure that the seals on your joints and seals are in place to prevent contamination.
Lubricating moving parts properly can increase their lifespan and improve the efficiency of your equipment.
Monitor Alignment And Vibration
In aggregate equipment, excessive vibrations or misalignments can lead to significant damage. Vibrations cause components to loosen, imbalances to occur, and wear. To resolve this:
Perform Vibration Assessment: Use sensors or monitoring tools to detect abnormal vibrations.
Check the Alignment: Regularly check and align conveyor belts. Crushers. Screens.
Secure Bolts: Inspect, tighten, and secure bolts, screws, and fasteners.
Early detection of alignment problems and vibrations and their correction can reduce the cost of repairs.
Keep Equipment Clean
Dust, debris, and material accumulation are common in aggregate operation and can negatively affect equipment performance. Cleaning your machines will prevent wear, overheating, and blockages. Cleaning your machine regularly includes:
Clean Up After Each Shift: Remove any dust, rocks, or residue from conveyors.
Check Filters: Remove or replace dirty air filters to maintain engine performance.
Maintain Clean Lubrication Points: Keep grease points free of debris and dirt to ensure proper lubrication.
A clean machine operates more efficiently. It also reduces the chance of long-term damage.
Monitor Electrical Systems
Electrical systems power many essential components in aggregate equipment. Faulty or damaged wiring, connectors, or moisture could lead to a breakdown or safety hazard. Check:
Electrical Wiring: Check for frayed wiring, loose connectors, or corroded connections.
Chargers: Make sure that the batteries are charged and free of corrosion.
Control Panels: Look for warning lights or error messages that could indicate underlying problems.
Routine electrical checks help maintain equipment performance and prevent dangerous malfunctions.
Train Operators
In equipment maintenance, a trained team is the first line of defense. Operators familiar with proper maintenance and use techniques are better able to spot issues early. Training should focus on:
Proper operation: Teach operators how to use the equipment without over- or under-using it.
Identifying Early Warning Signs: Train staff to recognize unusual noises, vibrations, or leaks.
Basic Skills: Provide Training on Essential Daily Checks and Minor Repairs.
A knowledgeable team will help extend equipment life and reduce costly downtime.
Record Maintainance Logs
It is vital to maintain detailed records for all maintenance activities to track the health status of your aggregate equipment. Use logs:
Tracking Repairs and Inspecting: Documentation of what was checked out, repaired, or changed.
Identify Recurring Problems: Spot patterns when equipment fails or wears out.
Schedule Future maintenance: Use records to predict when component servicing may be required.
Digital tools and programs can simplify your logging and keep you on the maintenance schedule.
Perform Seasonal Inspections
Aggregate equipment is subject to additional stress during extreme weather conditions. Seasonal checks help to prepare machines for harsh environments.
Maintaining Your Vehicle: Look for damage from freezing and use antifreeze.
Winter Maintenance: Check overheating and radiators for buildup.
Equipment continues to function reliably by adjusting maintenance efforts to seasonal conditions.
Conclusion
Maintenance is key to maximizing your equipment's performance, reducing downtime, and extending its lifespan. You can ensure that your equipment is in optimum working condition by maintaining a consistent maintenance schedule, inspecting the worn parts, training your team, and following an inspection plan. Proactive maintenance is important to avoid expensive repairs and replacements. These tips will help your business run smoothly.
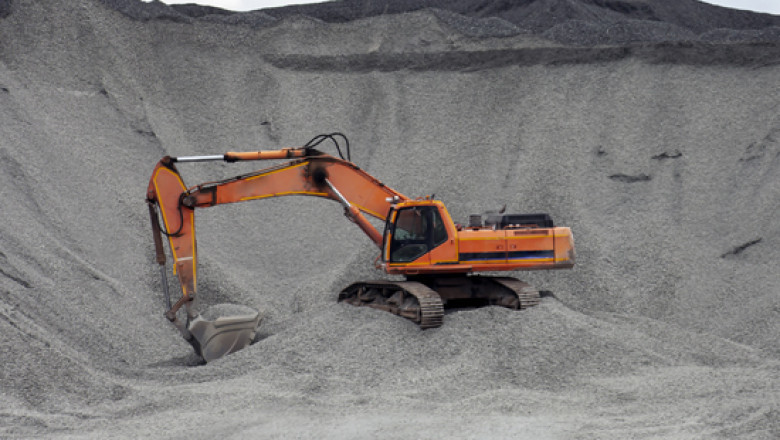

Comments
0 comment