views
Investment casting has undergone significant advancements over the years, driven by technological innovations and evolving industrial demands. Today, the process is more precise, efficient, and versatile than ever before. The rise of 3D printing technology, for example, has enabled the creation of more complex patterns and molds, reducing lead times and increasing design flexibility. Automation and robotics are further enhancing production speed and consistency, while sophisticated computer-aided design (CAD) software allows for even greater accuracy in modeling and simulation. Additionally, the focus on sustainability has led to the development of eco-friendly materials and processes, minimizing waste and energy consumption. As industries like aerospace, automotive, and medical devices continue to push the boundaries of innovation, investment casting is adapting, making it a crucial player in the future of high-performance manufacturing.
Why Investment Casting Is the Preferred Choice for Precision Components
Investment casting is the preferred method for producing precision components due to its ability to create intricate designs with high accuracy and minimal post-production machining. This process allows manufacturers to produce complex shapes and detailed geometries that would be difficult or impossible to achieve with traditional casting methods. The fine surface finish achieved through investment casting reduces the need for additional finishing, saving both time and cost. Moreover, it provides exceptional dimensional consistency, ensuring that each component meets tight tolerances. The versatility of materials used in investment casting, including high-performance alloys, further enhances its appeal, making it ideal for industries like aerospace, automotive, and medical devices where reliability and precision are paramount. As a result, investment casting has become the go-to
Understanding the Role of Investment Casting in Modern Manufacturing
Investment casting companies plays a critical role in modern manufacturing by offering a precise and efficient method for producing complex, high-performance components. Unlike traditional casting methods, investment casting allows for the creation of intricate shapes and fine details with minimal material waste, making it ideal for industries that require both precision and reliability. The process, which involves creating a wax model, coating it with a ceramic shell, and then melting the wax to leave a hollow mold, ensures that each part meets strict quality standards and tight tolerances. This versatility allows investment casting to be used across various sectors, including aerospace, automotive, medical devices, and energy, where advanced materials and high-quality finishes are essential. As the demand for more intricate, lightweight, and durable parts continues to grow, investment casting remains a cornerstone of modern manufacturing, enabling innovation and high-performance engineering solutions.
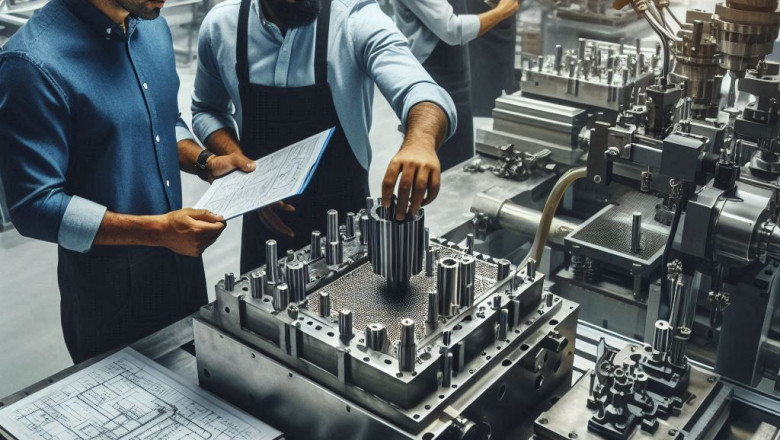
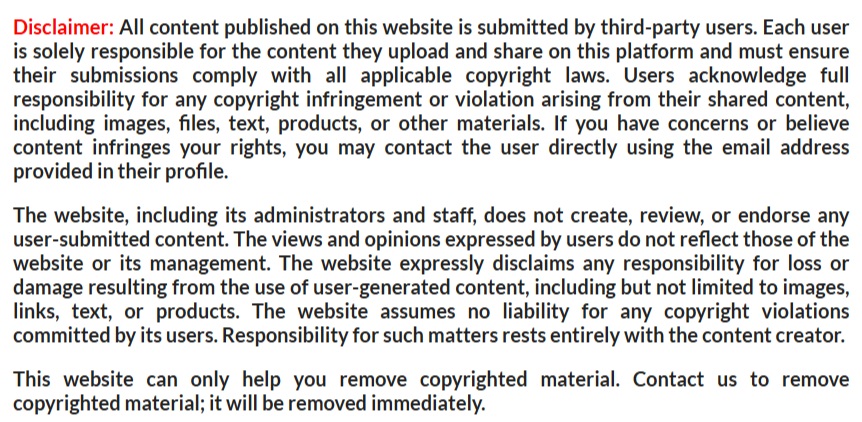
Comments
0 comment